Universal Robots and VersaBuilt to Launch New Direct Interface for Cobots and CNC Machines at ATX West
The leader in collaborative robots showcases solutions for fast cobot integration through the UR+ platform including VersaBuilt’s new communication interface for Haas CNCs and the patented workholding system MultiGrip™. Also, on display are Visumatic’s Collaborative Screw Driving Package and XPAK’s new box erector, ROBOX
Manufacturers struggling to get CNC machines to communicate directly with their collaborative robot now have a solution: VersaBuilt's CNC Communication URCap is a simple yet powerful interface for machine tending applications with Universal Robots. Launching at Universal Robots' booth 4605 at the ATX West show February 5-7 in Anaheim, CA, the URCap allows a UR cobot to easily execute any machining program stored on the CNC directly through the cobot's own teach pendant. Initially launching for Haas CNC machines, VersaBuilt will develop UR interfaces for other popular CNC makes later this year.
"CNC machine tending is one of the most popular tasks to automate with collaborative robots"
The Haas CNC Communication URCap will soon be available through the UR+ platform, a showroom of products all certified to integrate seamlessly with UR cobots. The URCap maintains all Haas safety interlock features and works with Haas, VersaBuilt, and other third-party automatic door openers. "VersaBuilt is excited to partner with Universal Robots to provide machine shops with automation solutions designed for high mix CNC manufacturers," says Albert Youngwerth, CEO of VersaBuilt Robotics, a company helping machine shops automate thousands of part numbers of all shapes and sizes in turning and milling applications.
Another testament to this mission is VersaBuilt's patented MultiGrip™ workholding system, soon available through the UR+ platform. MultiGrip™ includes an automatic vise, machinable jaws and an end-of-arm tool for the UR robot. MultiGrip™ was developed to address the frustration experienced when working with traditional robot grippers and CNC vises. "We ended up asking ourselves: why can't the robot and CNC use the same jaws?" explains Youngwerth. His team developed the unique workholding system that allows the robot and the CNC to share a set of MultiGrip™ machinable jaws for infeed, outfeed and CNC machining, resulting in reduced engineering costs, easier robot programming, faster setup time, and enhanced processing capabilities.
Regional Sales Director for Universal Robots' Americas Division, Stuart Shepherd, emphasizes the importance of better integration tools for cobots and CNCs. "CNC machine tending is one of the most popular tasks to automate with collaborative robots," he says. "But there's still hurdles to overcome in achieving seamless integration. VersaBuilt's two new products are important tools in addressing this. We're excited to welcome them to the UR ecosystem and share their solutions with the ATX audience."
Visumatic's showcases cobot-controlled screw driving
Joining VersaBuilt in the UR+ pipeline is Visumatic's VCM-3X.2 Collaborative Screw Driving Package delivering repeatable joining operations handled directly through the UR cobot's teach pendant. The system communicates to a screw driver control that handles a wide range of different screw driving feeds and routines. The VCM is bundled with pre-programmed fault recovery logic and Visumatic's field-proven power bit advance, bit position sensors and fastener delivery confirmation.
XPAK ROBOX - first solution for random case erecting
Visitors at UR's ATX booth can also experience the first solution for random robotic case erecting, the XPAK ROBOX™. The box erector, powered by a UR10e cobot arm allows packagers to randomly erect any box in their suite on-demand without changeover. The collaborative design not only enables the operator to safely and intuitively interface with the machine, ROBOX also realizes approximately 60% reduction in terms of the footprint required for a similar machine using more conventional robotic technology requiring fencing.
The UR10e is the largest cobot in Universal Robots new flagship line of cobots, the e-Series, showcased for the first time at the ATX West show. The e-Series sets a new standard for cobots, adding built-in force/torque sensing, unrivaled safety features, and improved precision for faster integration in a wider range of future-proofed applications.
"The e-Series strengthens the core principles defining collaborative robots: fast set-up, easy programming, flexible deployment, safe operation, and a quick ROI," says Stuart Shepherd. "End-users with complex applications and diverse or uncertain future needs will benefit from the e-Series platform and our unique UR+ ecosystem, knowing that their investment will be able to grow with them as their needs change," he explains, referencing the rapidly expanding UR+ portfolio that now includes more than 120 certified UR+ products and close to 400 approved companies in its developer program.
About Universal Robots
Universal Robots was co-founded in 2005 by the company's CTO, Esben Østergaard - the 2018 Engelberger Award Winner - who wanted to make robot technology accessible to all by developing small, user-friendly, reasonably priced, flexible industrial robots that are safe to work with. Since the first collaborative robot (cobot) was launched in 2008, the company has experienced considerable growth with the user-friendly cobot now sold worldwide. The company, which is a part of Teradyne Inc., is headquartered in Odense, Denmark, and has subsidiaries and regional offices in the United States, Germany, France, Spain, Italy, Czech Republic, Turkey, China, India, Singapore, Japan, South Korea, Taiwan and Mexico. In 2017, Universal Robots had a revenue of USD 170 million. For more information, please visit www.universal-robots.com or read our blog at blog.universal-robots.com.
Featured Product
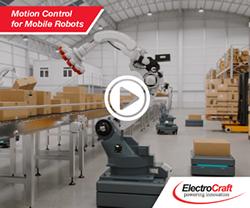