Bringing Autonomous Vessels to Open Water: Velodyne Lidar Supports the Next Generation of AV Developers in Maritime RobotX Challenge
Velodyne Sponsorship of RoboNation Brings State-of-the-Art Lidar Technology and Skills to Future Engineers
At the 2018 Maritime RobotX Challenge, Velodyne Lidar, Inc. contributed mentorship and lidar sensors to 15 university teams competing in an autonomous maritime competition. Held in Honolulu, Hawaii in December 2018, RobotX brought together teams from universities in the United States, Australia, China, Japan, Taiwan, and Singapore.
Participating teams built their vessels from the ground up, equipping them with propulsion, sensor, and control systems. Velodyne's Puck™ and Ultra Puck™ lidar sensors were the key perception components enabling the vessels to operate autonomously.
During the competition, the teams' autonomous boats demonstrated navigation and control, obstacle avoidance, location and sequence, identification and docking, detection and delivery, underwater recovery, and situational awareness. Each team created a website, technical design paper, presentation, and video to showcase their work.
National University of Singapore was awarded the competition's top prize, while Australia's Queensland University of Technology finished second, and Embry-Riddle Aeronautical University, based in Daytona Beach, Fla., placed third.
"Through the Maritime RobotX Challenge, next-generation engineers learn how lidar 3D perception empowers autonomous vessels," said Mike Jellen, President and Chief Commercial Officer, Velodyne Lidar. "It is a privilege to work with these remarkable students as they reinvent maritime technology."
RobotX is an international, university-level competition designed to broaden student exposure to autonomous vehicle (AV) and robotic technologies in the maritime environment. The event was organized by RoboNation, a non-profit organization that seeks to empower students to use Science, Technology, Engineering, and Math (STEM) to learn about the wider world. Velodyne is a RoboNation sponsor.
"This competition encourages student interest in autonomous robotic systems operating in the maritime domain, with an emphasis on the science and engineering of cooperative autonomy," said Daryl Davidson, Executive Director, RoboNation. "Velodyne's involvement in this event allows the students to gain experience with a state-of-the-art lidar and gives the company the opportunity to network with the top students in the world learning about autonomy. This is the technology that leading research and commercial organizations are using to bring exciting autonomous innovations to market today."
About Velodyne Lidar
Velodyne provides the smartest, most powerful lidar solutions for autonomy and driver assistance. Founded in 1983 and headquartered in San Jose, Calif., Velodyne is known worldwide for its portfolio of breakthrough lidar sensor technologies. In 2005, Velodyne's Founder and CEO, David Hall, invented real-time surround view lidar systems, revolutionizing perception and autonomy for automotive, new mobility, mapping, robotics, and security. Velodyne's high-performance product line includes a broad range of sensing solutions, including the cost-effective Puck™, the versatile Ultra Puck™, the perfect for L4-L5 autonomy Alpha Puck™, the ADAS-optimized Velarray™, and the groundbreaking software for driver assistance, Vella™.
About RoboNation, Inc.
RoboNation is a nonprofit organization whose mission is to provide a pathway of hands-on educational experiences that empower students to find innovative solutions to global challenges. We envision a world where technology unites people to learn, share, and create. www.robonation.org
Featured Product
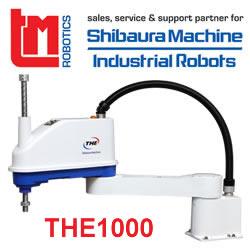
TM Robotics - Shibaura Machine THE SCARA range
The THE range from Shibaura Machine is an extensive line up of SCARA robots. Available in four arm lengths THE400 (400mm), THE600 (600mm) and the most recent THE800 (800mm) and THE1000 (1000mm), this range is suitable for assembly, handling, inspection and pick and place processes in varied industrial applications. The THE1000 boasts a 20kg payload capacity and an impressive 0.44 second cycle time, providing high speeds for processes with large components. In fact, the range has been recognised for as the price-to-performance leader compared to other SCARA models in its price range due to its impressive speed versus payload capacity.