Dürr Presents EcoProFleet as the First Automatic Guided Vehicles for the Paint Shop of the Future
The resulting cost benefits are all the greater the more varied and individual the bodies are that are being constructed and painted. Downtimes caused by sudden malfunctions are also reduced to a minimum since AGVs can be redirected to a different workstation or a different painting booth.
SOUTHFIELD, Mich., August 29, 2019 - Automobile production of the future is moving away from the production line and toward modular workstations. An important feature is flexible Automatic Guided Vehicles, or AGVs for short. Dürr presented, for the first time, an AGV specifically designed for paint shops as a new solution for more intelligent production at its Open House, which recently took place at the company's headquarters in Bietigheim-Bissingen, Germany. EcoProFleet combines tried-and-tested industrial components with innovative designs, like a new energy storage concept. This means that the AGV is ready for operation around the clock - without breaks for charging at the power outlet
Whether it's small cars or SUVs, electric motors or combustion engines, the range of vehicle models painted in a plant is ever-increasing. Manufacturers want to be able to easily integrate new vehicle types into the production process. This desire for flexibility and scalability is pushing linear production to its limits. The necessary migration to modular production is requiring manufacturers to rethink production logistics. In rigid painting lines, the process time for car bodies depends on the model that requires the longest time in the individual stations; this results in waiting times for other bodies, which can be avoided with a modular process. Instead of transporting bodies using conveyor technology laid inflexibly in the ground, they are moved independently and in parallel formation between work decks; as in spot repair, polishing, or intermediate storage. EcoProFleet enables a modular painting process in which different processing times for the car bodies no longer cause waiting times. The resulting cost benefits are all the greater the more varied and individual the bodies are that are being constructed and painted. Downtimes caused by sudden malfunctions are also reduced to a minimum since AGVs can be redirected to a different workstation or a different painting booth.
"Scalability and flexibility are becoming increasingly important in paint shops. With EcoProFleet we have designed the first AGV for paint shops and thus created an important enabler for these requirements," says Jens Reiner, Director R&D and Product Management at Dürr, describing the significance of the new development.
Exact fulfillment of paint-specific requirements
EcoProFleet is the first AGV that has been specifically optimized for the needs of paint shops. Its paint and solvent resistant platform is just 225 mm high. This low height means that the AGVs can go under all typical workstations and conveyor systems in order to drive a car body into a workstation, hand over, or pick up bodies; thus working together perfectly at the interfaces. In order to transport the heavy loads, the EcoProFleet AGV is designed with an unladen weight of 850 kg in good proportion with the maximum load capacity of 1,000 kg. The integrated technology with laser scanner and safety limit speed guarantees a high level of safety.
Intelligent concept for energy supply and control
The energy storage concept with Supercap Technology enables smart logistics tailored precisely to the painting process. EcoProFleet uses super capacitors as energy stores, which charge within 1.5 minutes. The charging points are installed strategically in the plant layout where the AGV would be stationary for passing off or picking up a body. This short time frame is enough to supply the super caps with more than enough energy for the next section. Compared with a battery-powered fleet, where a fixed number of transport systems always have to be kept plugged into a power outlet for hours, the major benefit of EcoProFleet's energy concept is that all the AGVs are always on the move and working. This is guaranteed by a sophisticated control system, connected to DXQcontrol, the central production control technology from Dürr. Dürr offers a consistent, intelligent, control system across all levels for the use of AGVs in paint shops; the device control for physical control of the individual AGVs, the fleet control for route planning, and the higher-level order planning are transparently linked via interfaces. This allows AGVs to fully exploit their potential as a flexible and efficient transport system.
EcoProFleet is not only functionally impressive but also attractive; its design won the prestigious IF Design Award.
The Dürr Group has been established in the United States since 1970 and currently employs around 880 people. From the new Campus with a state-of-art validation, testing, and training center in Southfield, MI, Dürr USA represents four of the five divisions. Paint and Final Assembly Systems offers equipment for painting and assembly processes, while Application Technology provides paint, sealants and adhesives application systems. Dürr's Clean Technology Systems is the global leader in air pollution abatement and energy efficient technologies. The subsidiary Schenck Trebel Corporation, based in Deer Park, New York, offers balancing machines, vibration and condition monitoring systems and services for the general industry. The customers of Dürr USA include automotive and commercial vehicle manufacturers as well as their suppliers, and a diverse group of other industries. The HOMAG Machinery North America operates the production facilities for the HOMAG Group in Grand Rapids, MI, which is also the base for sales and service company Stiles Machinery Inc. The HOMAG Group is the world's leading manufacturer of machines and systems for the wood-processing industry and trades.
The Dürr Group is one of the world's leading mechanical and plant engineering firms with extensive expertise in automation and digitization/Industry 4.0. Its products, systems and services enable highly efficient manufacturing processes in different industries. The Dürr Group supplies sectors like the automotive industry, mechanical engineering, chemical, pharmaceutical and woodworking industries. It generated sales of € 3.87 billion in 2018. In October 2018, the Dürr Group acquired the industrial environmental technology business of US-based company Babcock & Wilcox, comprising the Megtec and Universal brands. Since then, it has over 16,400 employees and 108 business locations in 32 countries. The Group operates in the market with five divisions:
• Paint and Final Assembly Systems: paint shops and final assembly systems for the automotive industry
• Application Technology: robot technologies for the automated application of paint, sealants and adhesives
• Clean Technology Systems: air pollution control, noise abatement systems and battery coating lines
• Measuring and Process Systems: balancing equipment as well as assembly, testing and filling technology
• Woodworking Machinery and Systems: machinery and equipment for the woodworking industry
Featured Product
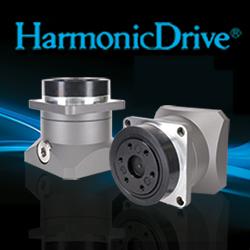