ACEINNA Launches Tiny, MEMS-based, OpenIMU330 Inertial Measurement Unit
-Industry’s first easy to integrate, cost effective triple redundant IMU for developing navigation & localization solutions for autonomous vehicles -For Developers Creating Guidance and Navigation Systems for Autonomous Vehicles, Robots, Drones, and Industrial, Construction, and Agricultural Machinery
ACEINNA (https://www.aceinna.com) today announced the new ACEINNA OpenIMU330B, a MEMS based, small form factor high-performance 6-DOF inertial measurement unit that enables autonomous vehicles to accurately stay on track during turns and complicated maneuvers. Measuring only 11mm x 15mm x 3mm, the ACEINNA OpenIMU330B is designed for use in automotive ADAS and autonomous systems as well as for electronic stability control and Lane Keep Assist functions.
This triple-redundant architecture, combined with the small, low-cost packaging, is intended to meet the challenging performance, reliability and cost requirements of the automotive market including the areas of Autonomous Vehicles, Self-Driving Taxis/Delivery Vehicles. ADAS Systems, Electronic Stability Control, Lane Keep Assist applications, etc.
"We are making it possible to quickly design in and integrate IMU guidance technology to AVG solutions critical for Level 3 ADAS systems," says Mike Horton, CTO of ACEINNA. "This is the first and only affordable, highly compact and triple redundant IMU module on the market."
The OpenIMU330B triple-redundant sensor architecture consists of three independent, 3-Axis Accelerometer and 3-Axis Gyros for excellent accuracy and reliability. By embedding a triple-redundant sensor array, the OpenIMU330 is able to use ACEINNA's proprietary voting scheme to utilize only valid sensor data. Any defective sensor output or errant dataset can be ignored or de-rated in importance. This architecture ensures the highest possible quality level and simultaneously improves the performance. The Bias Instability and Angular Random Walk of the rate sensors are 2o/hr and 0.2 o/√hr.
The OpenIMU330 is powered by an ARM M4 CPU with a Floating Point Unit. The OpenIMU330B module runs the OpenIMU open-source stack that includes an optimized full-state Kalman Filter for Attitude and GPS-Aided Position-Velocity-Time (PVT) measurement. A free tool-chain based on VS Code supports PC, MAC, and Ubuntu.
Technical features include a Triple Redundant, 3 axis MEMS angular rate sensor, Triple Redundant, High Performance 3 axis MEMS Accelerometer, Open Source Tool Chain and Custom Algorithms, ARM M4 CPU and built in 16-State Open Source Extended State Kalman Filter. The ACEINNA OpenIMU330B also includes Automotive Grade ASIL-B Version, SPI and UART interfaces, Wide Temp Range, -40C to +85C, High Reliability, and an open community & development support.
Development tools - Embedded navigation applications can be quickly developed on PC, MAC, and Ubuntu and deployed to run on OpenIMU hardware. ACEINNA Navigation Studio developer tools and GUI are found on our developer site: developers.aceinna.com
Much more detailed information about the OpenIMU330B can be found at https://www.aceinna.com/inertial-systems/OpenIMU330B Engineering samples and evaluation kits are available to qualified customers by contacting Aceinna Inc. directly.
ABOUT ACEINNA
ACEINNA Inc., is a leading provider of sensing solutions for automotive, industrial, telecom, datacenter and cloud infrastructure, consumer appliances, agricultural and construction markets.
ACEINNA's precise positioning solutions are MEMS based, open-source, inertial sensing systems that are leading the industry by enabling easy-to-use, centimeter-accurate navigation systems for the autonomous revolution. ACEINNA's isolated current sensor product family is based on an AMR technology that enables industry leading accuracy, bandwidth and step response in a simple, cost effective single-chip form factor. ACEINNA has R&D facilities in San Jose, CA; Andover, MA; and Chicago, IL; as well as manufacturing facilities in Wuxi, China.
Featured Product
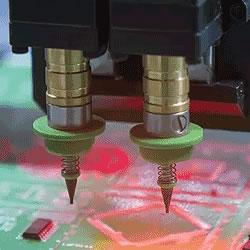