13,000th Dürr robot set for GM in Korea
New paint shop for General Motors
SOUTHFIELD, Mich., Sept. 19, 2019 - The 13,000th robot manufactured by Dürr will be taking up residence in a new paint shop for General Motors in Changwon, Korea. This is the first installation of the new Dürr robot generation for GM. The robot equipment is part of Dürr's biggest order in Korea to date.
The 13,000th robot manufactured by Dürr is an EcoRP E043i, and will be used to paint the interior of passenger cars at GM in Changwon. The celebration of this specific robot is special for many reasons: it is the first time Dürr's new generation three robot will be used at GM. GM relies on fully automated painting with the latest application technology. The equipment for the new paint shop, which Dürr was commissioned to build, includes a total of 78 third-generation robots. The total order is also the biggest order Dürr has received to date as a general contractor in Korea. GM will put the planned plant into in 2021, and paint the new Chevrolet Spark as well as compact SUVs using the 3-wet method.
The EcoRP E043i and 033i painting robots will handle painting the interior and exterior of the car bodies in Changwon. Seven-axis robots with the latest EcoBell3 atomizer technology will paint the interiors of the vehicle bodies with extremely high precision and flexibility. Their enhanced mobility mean they can reach even difficult-to-access places effortlessly. The exteriors will be painted using six-axis robots. Dürr's application technology, such as the EcoBell Cleaner D2 atomizer cleaner, stands for state-of-the-art processes with low VOC emissions. The interplay of the dosing pump, color changer, atomizer, and atomizer cleaner ensures fast and efficient color changes within just 15 seconds, reducing paint loss and flushing agent consumption when changing color.
The solvents are removed from the exhaust air using an Ecopure® RTO regenerative thermal exhaust air purification system together with the Ecopure® CRC VOC concentrator from Dürr.
In the existing factory in Changwon, Dürr designed the plant to be over three levels with two painting lines for a total volume of 60 vehicles per hour. GM thought one step ahead when designing the plant by providing space for a later, two-tone painting line.
The construction of the plant also represents Dürr's biggest order in Korea. A decisive factor for GM was the geographical proximity. Dürr is implementing the project in close cooperation between the headquarters in Germany and the Korean subsidiary in Seoul. Having contact partners directly on-site means that Dürr can provide efficient and highly qualified service locally.
"We're proud that GM chose us for this important project. This shows the high customer benefit of the new features of the third-generation robots: top quality and availability with optimized costs," explains Dr. Lars Friedrich, member of the Board of Management of Dürr Systems AG and responsible for the Application Technology Division.
About The Dürr Group
The Dürr Group has been established in the United States since 1970 and currently employs approximately 880 people. From the Campus with a state-of-art validation, testing, and training center in Southfield, MI, Dürr USA represents four of the five divisions. Paint and Final Assembly Systems offers equipment for painting and assembly processes, while Application Technology provides paint, sealants and adhesives application systems. Dürr's Clean Technology Systems division is the global leader in air pollution control, noise abatement systems, and battery electrode coating lines. It has three headquarters locations in the US: Durr Systems, Southfield, MI; Durr MEGTEC, LCC, De Pere, WI; and Durr Universal, Inc., Stoughton, WI. The subsidiary Schenck USA Corporation, based in Deer Park, NY, offers balancing machines, vibration, and condition-monitoring systems and services for general industry. The customers of Dürr USA include automotive and commercial vehicle manufacturers, as well as their suppliers, and a diverse group of other industries like the chemical or wood industry. HOMAG Machinery North America operates the production facilities for HOMAG Group in Grand Rapids, MI, which is also the base for the sales and service company Stiles Machinery Inc. The HOMAG Group produces machinery and equipment for the woodworking industry.
The Dürr Group is one of the world's leading mechanical and plant engineering firms with extensive expertise in automation and digitization/Industry 4.0. Its products, systems and services enable highly efficient manufacturing processes in different industries. The Dürr Group supplies sectors like the automotive industry, mechanical engineering, chemical, pharmaceutical and woodworking industries. It generated sales of € 3.87 billion in 2018. In October 2018, the Dürr Group acquired the industrial environmental technology business of US-based company Babcock & Wilcox, comprising the Megtec and Universal brands. Since then, it has over 16,400 employees and 108 business locations in 32 countries. The Group operates in the market with five divisions:
• Paint and Final Assembly Systems: paint shops and final assembly systems for the automotive industry
• Application Technology: robot technologies for the automated application of paint, sealants and adhesives
• Clean Technology Systems: air pollution control, noise abatement systems and battery coating lines
• Measuring and Process Systems: balancing equipment as well as assembly, testing and filling technology
• Woodworking Machinery and Systems: machinery and equipment for the woodworking industry
Featured Product
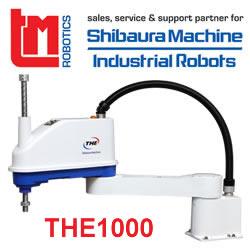
TM Robotics - Shibaura Machine THE SCARA range
The THE range from Shibaura Machine is an extensive line up of SCARA robots. Available in four arm lengths THE400 (400mm), THE600 (600mm) and the most recent THE800 (800mm) and THE1000 (1000mm), this range is suitable for assembly, handling, inspection and pick and place processes in varied industrial applications. The THE1000 boasts a 20kg payload capacity and an impressive 0.44 second cycle time, providing high speeds for processes with large components. In fact, the range has been recognised for as the price-to-performance leader compared to other SCARA models in its price range due to its impressive speed versus payload capacity.