Micro waterjet bridges the gap between EDM and Micro Laser
Cutting narrow incisions with ultra-high precision in high density materials using waterjet technology requires a specific waterjet cutting process: the Fine Abrasive Waterjet process (FAWJ). The first FAWJ cutting head was developed by Water Jet Sweden in 2008
Fine Abrasive Waterjet bridges the gap
To enable such levels of precision you need two things: (1) a cutting head and cutting process for FAWJ cutting, and (2) a machine built for extreme accuracy. The NCM 10 Micro from Water Jet Sweden fulfils both of those requirements.
FAWJ cutting process for 0.2 mm incisions
The first micro waterjet cutting head was developed by Water Jet Sweden in 2008. It is a high precision cutting tool producing one of the most precise abrasive water jets in the world. The unique cutting head enables an abrasive jet diameter down to 0.2 mm. The FAWJ cutting process requires very fine abrasives of 230-240 mesh and a special CNC controlled dosage abrasive feeder.
Machine table designed for ± 0.008 accuracy
To reach the levels of accuracy required in micro part manufacturing, the NCM 10 water jet has a number of unique design features to create a rigid table that withstands temperature fluctuations:
Mineral Casting Bearlit table frame - a table frame made of a composite material with exceptional stiffness that withstands vibrations and temperature fluctuations. The frame is integrated in the machine construction and motion system as a complete unit.
Rubber suspended stainless steel water catcher - the free-standing catcher solution prevents vibrations and temperature variations from influencing the cutting process. Stainless steel makes it maintenance free.
Renishaw Invar Scale in X and Y - with a Renishaw Absolute Linear Encoder fitted in both X and Y axes you have a micrometer scale with an extremely low expansion coefficient and ultra-high resolution.
Prepared for any kind of fixtures
The palettized cutting table makes it easy to install fixtures and presses for different types of machining. Maximum table size is 1x1 m which covers most cutting applications. The cutting table is fixed into the table frame to enable ultra-high precision cutting.
"There are many suppliers who state that they offer micro cutting machines, but not many can offer a true micro part cutting tool with 0.2 mm incision combined with ± 0.008 accuracy," says Tony Rydh, co-founder and CTO at Water Jet Sweden.
Fine Abrasive Waterjet Cutting vs. EDM
Extruder tool matrix
Tempered tool steel, 15 mm
NCM 10
Max. speed 11 mm/min
Min. speed 4 mm/min
Cutting accuracy: 0.02 mm
Manufacturing time: 1 h 30 min
Prime cost: € 180
EDM:
Speed: 1 - 2 mm/min
Accuracy: About 0.001 mm
Manufacturing time: > 8 hours
Prime cost: € 480
About Water Jet Sweden AB
A successful pursuit of measurable customer benefits
Back in 1993, we produced our Machines in a private garage. Today we serve customers in more than 40 countries. Our native town of Ronneby in southern Sweden has become a R & D cluster of global renown, where the scientific establishment, the water jet industry and the business community join efforts to develop the water jet cutting technology of tomorrow.
Our ultimate end product is customer value, and the benefits our machines and service can offer are highly measurable in terms of time, money, product quality and sustainability.
For more information, please contact:
Water Jet Sweden AB
Lennart Svensson, MD or Klas Wallström, CMO
Teknikvägen 4
S-372 38 Ronneby Sweden
Tel: +46 457 455 440
E-mail: sales@waterjet.se
http://waterjetsweden.com
Featured Product
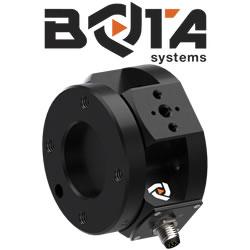
Bota Systems - The SensONE 6-axis force torque sensor for robots
Our Bota Systems force torque sensors, like the SensONE, are designed for collaborative and industrial robots. It enables human machine interaction, provides force, vision and inertia data and offers "plug and work" foll all platforms. The compact design is dustproof and water-resistant. The ISO 9409-1-50-4-M6 mounting flange makes integrating the SensONE sensor with robots extremely easy.
No adapter is needed, only fasteners! The SensONE sensor is a one of its kind product and the best solution for force feedback applications and collaborative robots at its price. The SensONE is available in two communication options and includes software integration with TwinCAT, ROS, LabVIEW and MATLAB®.