AUTONOMOUS MOBILE ROBOTS IN A JUST-IN-TIME PRODUCTION ENVIRONMENT
Mobile robots are currently seen as a critical component of ‘Industry 4.0' and their adoption rate into production processes is expected to increase in the next few years. With the release of their Fleetware management software, Sorion enables seamless integration of robots into the manufacturing environment.
Mobile robots working in a team
Until recently, robots have mainly been used in a fixed manner, with each robot performing a simple, repetitive task. While this approach is suitable for many logistics and production applications, it cannot be applied in just-in-time manufacturing environments, where product variability and sequencing demand a dynamic route/mission assignment.
For example, in a production environment AMRs can be used to move subassemblies and components between manufacturing cells. This requires a flexible management system for mission assignment, with real time adaptation to changing demands: on-route mission reassignment / cancellation. Sorion's Fleetware suite was designed to overcome this challenge.
Factory Integration
Fleetware links the operation of AMRs with the overall workflow, processes and environmental systems of a facility, including pick to light systems, manual and automated assembly stations, test systems. It has all the tools to make sure the fleet of robots is operating at peak efficiency with minimal human intervention.
The system interfaces to customer factory systems to receive build information and manages the assignment of missions by logistic priority.
By continuously monitoring and coordinating a fleet of up to 100 AMRs, Fleetware helps robots work together as a team to solve complex tasks. It controls the movements of robots for an optimised workflow while allowing for charging and monitoring the state of the system.
This automated workflow minimises errors on the production line and frees up a significant amount of time for the employees to focus on more meaningful tasks.
Testing the system before implementation
For companies investing in AMRs, analysing the overall workflow, processes and distance travelled is key to understanding how many robots are required before committing to a major investment. Running a simulation allows production managers to visualise the system, looking at all system interactions and their impact on overall efficiency.
Using the Fleetware Simulation Tool, the environment can be tested and validated prior to the installation of physical equipment and robots, saving time and resources. Furthermore, the impact of changes to layout and capacity can be tested without disturbing the actual system.
AMR monitoring drives operational efficiency and improved OEE
Fleetware is constantly collecting data from the robot fleet. The software monitors real-time fleet status by robot, product ID or station/stopping point. This allows for tracking of waiting and charge times and classification of stoppage time, giving a total overview of fleet utilisation and performance with failure and cause statistics.
Fleetware is under continuous development. Through close collaboration with robot manufacturers and their customers, Sorion are constantly improving the solution to meet the evolving needs of the industry.
Featured Product
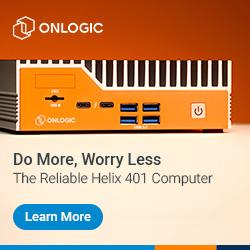
OnLogic Helix 401 Fanless Hybrid-Core Computer
OnLogic's Helix 401 Compact Fanless Computer offers scalable, high-performance processing and can simultaneously drive multiple 4K displays, making it the ideal computing platform for many automation and IIoT applications. The Helix 401 has the horsepower to drive mission-critical applications while requiring less than 28W of power, and is small enough to fit in space-constrained locations or enclosures. It can be configured with a range of Intel® 12th generation processors, up to a Core i7 and has Intel Iris® Xe graphics onboard.