Realtime Robotics Unveils Realtime Controller
Simplifies and reduces the programming burden, accelerating the integration of robots
Realtime Robotics, the inventor of responsive motion planning for industrial robots and autonomous vehicles, today announced the launch of its Realtime Controller. The solution dramatically reduces and simplifies the programming required to safely integrate robotic workcells, speeding up the time to deployment.
As the pressure intensifies to improve margins, it will accelerate the adoption of robotic automation. However, integrating robotic operating systems currently is complex, time-consuming, and cost-prohibitive, which has limited where and how the technology is deployed. With the Realtime Controller, multi-robot cells are much more flexible, as it automates many core processes and can dynamically adjust to variable production conditions.
Using Realtime's Controller, manufacturers can now quickly and easily plan, simulate, and validate automation through the entire deployment. The Realtime Controller connects with the customer's PLC and robot controller so that they can autonomously calculate, communicate, and execute collision-free motions. Both development time and cycle time are significantly reduced with automated interlocks and interference zone-free multi-robot workcells enabling robots to be deployed more quickly and expand into new areas that were previously cost-prohibitive.
The Realtime Controller is an industrial hardware computing platform with proprietary hardware and software that supports both off-line programming and run-time operation of single and multi-robot work cells. The software toolkit and API enable easy integration with PLCs, picking systems, robot controllers, simulation software, and other task planning solutions. Its web-based interface allows companies to configure and monitor robot workcells, including visualizing robot motions and managing fault conditions. In addition, Realtime's motion planning enables immediate and autonomous fault recovery solutions for multi-robot workcells.
The Realtime Controller will be commercially available in North America, Europe, Japan and China beginning in May 2020.
Quotes and Commentary
"Our vision is to reduce the friction associated with deploying robots in industrial settings. The Realtime Controller is a catalyst for accelerating and simplifying robotic automation across the globe, enabling manufacturers to finally benefit from the power of industrial robots working together."
— Peter Howard, CEO, Realtime Robotics
Customer Quote
"Realtime's RapidPlan technology and the new Realtime Controller provides the power to transform how we deploy and operate industrial robots. The solution dramatically reduces time for motion planning and eliminates interlocking, so our engineers can focus their efforts on designing fully capable work-cells and efficient multi-robot deployments."
— Gurpreet Ghataore, Advanced Research Engineer, The Manufacturing Technology Centre
Other Resources
Realtime Controller specification sheet
About Realtime Robotics
Realtime Robotics has developed a specialized processor to generate safe motion plans in milliseconds for industrial robots and autonomous vehicles. Its solution enables robots to function together in unstructured and collaborative workspaces, as well as react to dynamic obstructions the instant changes are perceived. Its solutions expand the potential of automation. Learn more about Realtime Robotics here and connect on Twitter and LinkedIn.
Featured Product
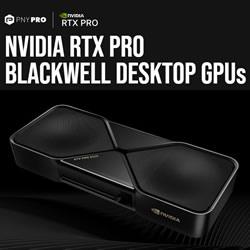
NVIDIA RTX PRO™ BLACKWELL DESKTOP GPUs
NVIDIA RTX PRO™ - Built for Professionals - NVIDIA RTX PRO Blackwell Desktop GPUs feature the latest breakthroughs in AI, ray tracing, and neural rendering technology to power the most innovative workflows in design, engineering, and beyond.