The high efficiency of induction brazing for copper tube assemblies demonstrated by UltraFlex
By replacing torch-based brazing with induction brazing, the customer would not only achieve a time- and energy-efficient brazing process and increased productivity; he would ensure a process that is safe both for the operator and the environment, due to the lack of open flame and noxious emissions.
A demonstration of the high energy and time efficiency of the process of induction brazing for copper tube assemblies has recently been shared by UltraFlex. UltraFlex is a major manufacturer of induction heaters and frequently publishes the results from induction heating test scenarios set up per request of potential customers.
In this demo scenario, a manufacturer of refrigerator compressors was looking at evaluating the replacement of their current torch-brazing process for compressor tubing with induction brazing. The goal was to achieve higher energy efficiency and up to 10 sec brazing time for brazing copper tube assemblies with tube size ranging between 1/8 inch (3.18 mm) to 3/8 inch (9.53 mm). The customer was also aiming at improving the brazing quality as well as the reliability of the process.
For brazing the copper tube assemblies UltraFlex engineers recommended the use of UBraze Handheld Brazing System along with an induction heater from the UltraFlex UltraHeat SM series.
UBraze is a mobile induction heating solution that can be used as a hand-held unit or can be integrated with a robotic arm for automated production lines. It is a durable assembly with an easy-hold grip, and a handle at the top of the unit to maximize stability. UltraHeat SM are compact and easy-to-use 5kW induction heaters that can be used with either a water-cooled or air-cooled remote heat station.
At target temperature of 815 C and using a standard induction coil suitable for ⅜" OD tubing, it took between 1 and 7 seconds to braze each copper tube assembly, which was far less than the customer's target. By replacing torch-based brazing with induction brazing, the customer would not only achieve a time- and energy-efficient brazing process and increased productivity; he would ensure a process that is safe both for the operator and the environment, due to the lack of open flame and noxious emissions. Finally, when used on the line, this induction brazing process would produce consistent, high-quality results with no dependency on the operator's skills.
Find out more at:
https://ultraflexpower.com/
Contact us at:
+1.631.467.6814
uptnews@ultraflexpower.com
About UltraFlex Power Technologies:
UltraFlex Power Technologies (ultraflexpower.com) offers the most advanced and innovative digitally controlled induction heating equipment in the industry. Its compact modular and flexible systems are used for a wide variety of induction heating, casting and melting applications.
Featured Product
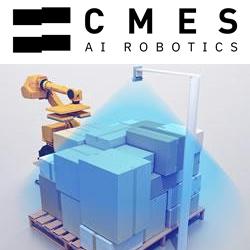