UltraFlex performing induction annealing in less than 1 second at 1900°F (1037°C)
By using induction, the customer would not only achieve much improved time- an energy-efficiency for this process; he would also ensure high-quality and repeatable results, that are independent of the operator skills.
A demo application revealing the super fast induction annealing process performed at temperature of 1900°F (1037°C) has recently been completed by UltraFlex Power Technologies. UltraFlex is a major manufacturer of advanced, digitally controlled induction heaters. The company is frequently being reached by potential customers interested in test applications proving the optimization capabilities of induction heating for their specific setup.
In this demo application, a customer from the Automotive and Transportation industry was looking to improve the quality and reliability of their current annealing process by using induction. The process involved heating stainless steel corrugated tubes with 0.25" (0.635cm) OD and 12" (30.48cm) of length. The required heated length was 0.40" (1.02cm), and the entire cycle time had to fit within 3.7 seconds.
The annealing is a very specific process which changes the properties of the metals and alloys without melting them. It is performed by heating the parts at temperatures that are high enough for changing the properties, but below the point of melting. For the materials used in this test setup, the target annealing temperature was 1800-1900°F (982 - 1037°C) for each part.
When induction is being used to perform the process, reaching the annealing temperature is achieved using alternating currents of high frequency and magnetic fields. The goal is to focus the heat into a small area, and thus obtain a time-efficient and high-quality annealing.
To perform the annealing, UltraFlex engineers recommended the use of an induction heater from the UltraFlex UltraHeat S series, along with a water-cooled heat station HS-4W. UltraHeat S are small and efficient 2kW induction heaters that operate with a water-cooled or air-cooled remote heat station. All systems utilize the latest switching power supply technology and adaptive digital phase control, which efficiently operate in wide frequency ranges.
By using a 4-turn coil with a tight OD to apply focused heat into a small area, each part was heated to 1900F (1037C) within less than a second and the annealing process was successfully completed. With induction heating, the customer would not only achieve much improved time- an energy-efficiency for this process; he would also ensure high-quality and repeatable results, that are independent of the operator skills. In addition, the lack of open flame, fumes and noxious emissions would make this annealing process completely safe - safe for the operator, safe for the environment.
Find out more at:
https://ultraflexpower.com/
Contact us at:
+1.631.467.6814
uptnews@ultraflexpower.com
About UltraFlex Power Technologies:
UltraFlex Power Technologies (ultraflexpower.com) offers the most advanced and innovative digitally controlled induction heating equipment in the industry. Its compact modular and flexible systems are used for a wide variety of induction heating, casting and melting applications.
Featured Product
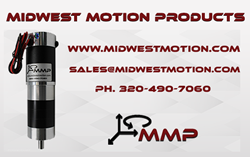