UltraFlex induction soldering a brass and copper assembly within 11 seconds
Following the test setup, UltraFlex engineers concluded that the induction-based soldering would allow for increased productivity, far exceeding the customer targets, and high-quality, consistent results, regardless of the operator skills.
The time- and cost-efficient induction soldering process for a brass and copper agriculture tool has recently been demonstrated by UltraFlex Power Technologies. UltraFlex is a leading provider of innovative, digitally-controlled induction heaters and as such is frequently being asked to perform test setups, allowing potential customers to evaluate the results they can achieve via replacing traditional heating methods with induction heating.
This time the test setup has been requested by a manufacturer of agricultural tools looking to replace gas soldering with induction-based soldering, to improve the soldering quality and repeatability, as well as ensure a safe work environment. The customer was also looking to boost productivity, with a target production rate of 50 soldered assemblies per day.
The parts that had to be soldered were a copper tubing and a brass valve. The requirement was to heat the middle of the parts to no more than 280°C, allowing the solder to flow between the parts and make a strong joint.
UltraFlex engineers are always approaching each customer heating scenario with the goal to achieve the best quality-cost ratio. Hence, in this case they evaluated the use of 2 induction heaters from the UltraHeat SM series - a 2 kW and a 5 kW induction heater. UltraHeat SM are compact and easy-to-use induction heaters. They can be used with either water-cooled or air-cooled remote heat stations.
The test with the 2 kW induction heater, however, showed less flexibility since it required a high-inductance coil, which would obstruct the working premise and could come in contact with the part. The 2 kW heater was also requiring heating cycles of 16 to 38 seconds. A 5KW induction heater, on the other hand, although being more expensive, demonstrated superior heating results. It required a 2-turn heating coil, ensuring better heat concentration and heating time as short as 11 seconds, for the target heating temperature of 280°C. It also allowed for solder flowing upwards or downwards, thus enabling the customer to change the part orientation per their needs.
The test setup concluded that a 5 KW induction heating unit would ensure a fast, energy- and cost-efficient induction soldering process. It would allow for increased productivity, far exceeding the customer targets, and high-quality, consistent results, regardless of the operator skills. Finally, by replacing gas soldering with induction-based soldering the customer would achieve a completely safe process - safe for the operator and for the environment - due to the lack of open flame, fumes and noxious emissions.
Find out more at:
https://ultraflexpower.com/
Contact us at:
+1.631.467.6814
uptnews@ultraflexpower.com
About UltraFlex Power Technologies:
UltraFlex Power Technologies (ultraflexpower.com) offers the most advanced and innovative digitally controlled induction heating equipment in the industry. Its compact modular and flexible systems are used for a wide variety of induction heating, casting and melting applications.
Featured Product
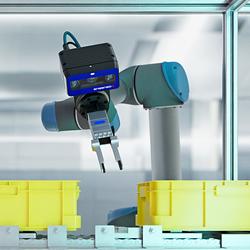