UltraFlex accomplishes 10-second induction annealing of small stainless steel tubes
In addition to being efficient and independent of the operator's skills, this induction-based annealing process was completely safe - for the operator and for the environment - due to the lack of open flame and noxious emissions.
An UltraFlex recent demonstration for a potential customer proved the efficiency of using induction heating for the annealing of stainless steel tubes. UltraFlex is a leading provider of digitally-controlled induction heaters and has set up the demonstration so the customer would be able to evaluate the possibility of replacing their current torch-based annealing process with induction-based annealing.
A stainless steel tube with 1.25″ (3.175 cm) OD and 0.065″ (0.165 cm) wall had been provided for this induction heating scenario. The heating had to be applied to 1″ (2.54 cm) on the tube end, so the end can be formed over and closed.
UltraFlex engineers considered the use of an induction heater from the UltraFlex UltraHeat SM series as most appropriate for this induction heating scenario. UltraHeat SM are compact and easy-to-use 5kW induction heating systems. They can be used with either a water-cooled or air-cooled remote heat station and are easy to tune to a wide range of loads and coils. A 4-turn induction coil was selected for this heating case.
After only 2 tests, UltraFlex engineers confirmed that the induction heater power output should be set to 5 kW, to achieve a heating cycle of 10 seconds at the target temperature of 1900°F (~1038°C). The customer was provided the full set of heating parameters that would ensure an efficient, high-quality and repeatable annealing process, meeting all customer requirements. In addition to being efficient and independent of the operator's skills, this induction-based annealing process would be completely safe - for the operator and for the environment - due to the lack of open flame and noxious emissions.
Find out more at:
https://ultraflexpower.com/
Contact us at:
+1.631.467.6814
uptnews@ultraflexpower.com
About UltraFlex Power Technologies:
UltraFlex Power Technologies (ultraflexpower.com) offers the most advanced and innovative digitally controlled induction heating equipment in the industry. Its compact modular and flexible systems are used for a wide variety of induction heating, casting and melting applications.
Featured Product
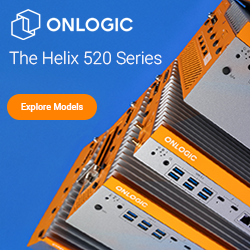