Obstacles in Robotic Welding in the Brazilian Industry
From a welding machine maintenance company, a company that significantly participated in the modification of the welding industry in Latin America and will certainly change the welding industry in other regions where there are needs to be met.
When the company Powermig Automação e Soldagem started its activities, the company's services were limited to maintenance of welding machines. In the design of this equipment, one of the main concerns was how achieve energy savings combined with higher power. Also, noise interference on voltage measurements, fluctuations in the electrical power network, impedance variations or even magnetic metallic masses are factors that could affect the result achieved by welding machines. As well, these machines are part of the set of main causes of voltage fluctuations in industrial electrical networks. As a result, yield loss and variation of power and torque in electrical machines. Or else, interference in electrical protection devices. Finally, when a equipment like this was send for maintenance repair, sometimes the decision was to discard. The maintenance costs were unfeasible when compared with the acquisition of new equipment.
Understanding the reality of the welding sector in the industry and working to meet the interests of this industry was the scope of the Powermig company since the beginning of its activities, 15 years ago. In this sense, the direction of their activities went from the maintenance of welding machines to the industrialization of robotic welding cells. The expertise obtained in the initial years as a maintenance company was the basis for the design of the activity model that happened.
At that time, industrial welding in Brazil, headquarters of the Powermig company, had robotic cells in mostly in the automotive industry. Robotic welding, compared to manual welding, overcomes this by being more accurate, fast and for mitigating the risks for humans. Problems related to energy inefficiency in the process manual, low productivity, low quality of the welded product and negative effects on the welding professional, from fatigue to greater consequences for your health are factors that underlie automation in welding. The automobile industry has easily absorbed welding automation into its production lines. On the other hand, the challenge was to bring access to this solution to other industrial segments.
Costs and limitations in application have produced obstacles that the auto industry has more easily overcome than other industrial sectors. However, the world of welding was changing. New technologies, new discoveries and developments resulted from research and investment in industrial welding innovation. In addition to robotic welding, on-board computers and on-board programs, the use of gas combinations and new wires with highly sophisticated metal alloys. Hybrid laser-arc welding, overcoming the limitations of high cost laser welding and limited applications. Also GMAW - gas metal arc welding - to weld steel alloys for automobiles. Or the use of laser technology in aluminum or low carbon steel.
Realizing that automated welding is necessary beyond the automotive sector and acting accordingly, based the decision-making about the company's role. The industry needs automation in welding, it needs differentiated, special models, because it is unfeasible to fit into models such as those that serve the automotive sector. This industry needs special cells and needs to automate its processes to avoid losing customers. Production more sustainable, more accessible products due to the reduction of industrialization costs and, in addition to the lower costs, higher quality is the promise being fulfilled by automation in welding. Providing this to the welding industry with the production of special cells, it changed the welding market in the region where the company Powermig operates.
Powermig followed the industry and its demands, understood the problems and started to provide opportunities to a large extent custom designs for the general industry achieve the use of robotic cells for welding. From a company maintenance on welding machines, became a company that participated significantly in the modification of the welding industry in Latin America and will certainly change the welding industry in other regions where there are needs that need to be met.
The future of welding will still require agile manufacturing and access to smart materials that will reduce energy costs. In fact, energy efficiency is a reality today, it is unnecessary to wait for the future to arrive to think in that.
By Carmen Thomazi carmen@davinciprojetos.com.br
Chemical engineer, technical director at Da Vinci Projetos, member of the management board of several companies and professor in Executive Education at Faculdade FIPECAFI.
Featured Product
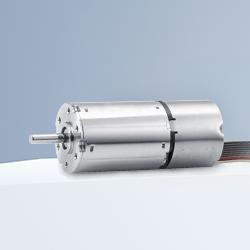