Industrial inspection robots
Inspection tasks, as they involve checking and monitoring, lead to the detection of malfunctions or various errors. In this way, increasing automation in hard-to-reach or hazardous environments is one of the main uses of robotics for inspection.
⊛ Inspection tasks are frequent in many environments: refineries, old or dilapidated buildings, industrial plants, infrastructures, roads, tunnels or power stations, among others. Due to the nature of these environments, inspection tasks often present dangers for humans, and therefore the use of robotics for inspection has grown considerably. In addition, these mechanical and repetitive activities are precisely what robots do best and most efficiently.
Can you imagine an inspection robot performing quality control in a factory, or an inspection robot operating in an electrical tunnel?
Inspection robotics is growing by approximately 25% every year because the ROI (return on investment) is demonstrable for end users. To this figure must be added another very significant one: industrial inspection work carried out by humans costs companies approximately more than 37 billion euros a year.
⊛ What is an industrial inspection robot?
Industrial inspection robots incorporate software, sensors, vision systems, lasers and other advanced technology needed to recognise and interact with the environment to perform inspection tasks autonomously or collaboratively.
These robots are usually marketed for the surveillance of different hazards such as the control of environmental factors (gas, smoke, radiation, fire…), to check the state of infrastructures and buildings that may be difficult for humans to access, or to perform routine inspections in industrial spaces.
Specifically, Robotnik's inspection robots are able to perform tasks safely and autonomously, reporting data to a control centre, or also remotely, being teleoperated by an operator.
3D localisation brings a disruptive approach to mapping, navigating and locating the robot in the space it is in, including remote locations.
One of the main advantages is that a mobile inspection robot is able to cover a large infrastructure with one or a few units, thus avoiding the installation of hundreds of sensors or static devices, as the robot can operate in different locations.
Depending on the size of the space to be inspected, the number of robot units can be scaled, considering the possibility of incorporating a fleet of robots that the user can easily manage from the advanced user interface developed by Robotnik. Among the advances of collaborative inspection robotics is the flexibility: you can start working with one unit and scale its use with new tasks or new work areas.
⊛ Check the link to know which robots are already performinf inspection tasks.
Featured Product
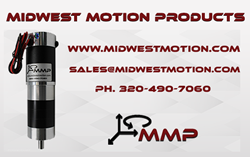