Flexxbotics Provides Robot Compatibility with DMG MORI CNC Machines and Equipment
Flexxbotics’ patent-pending FlexxCORE technology enables robots to securely connect and communicate with DMG MORI machinery in the smart factory to provide more powerful, flexible and open robot connectivity than previously possible.
Boston, MA - March 5, 2024 - Flexxbotics, delivering workcell digitalization for robot-driven manufacturing, today announced advanced robot machine tending connectivity compatible with the entire range of DMG MORI machine tools including turning, milling, ultrasonic, lasertec, additive manufacturing, and grinding. With Flexxbotics next generation machining environments using robotics with DMG MORI equipment achieve higher yields, greater throughput and increased profit per part.
Flexxbotics' patent-pending FlexxCORE technology enables robots to securely connect and communicate with DMG MORI machinery in the smart factory to provide more powerful, flexible and open robot connectivity than previously possible.
Flexxbotics compatibility includes DMG MORI's CELOS®, as well as, Siemens, Heidenhain, Mapps, Mitsubishi and Fanuc controls utilized across DMG MORI systems. Flexxbotics is also compatible with a wide range of open standard protocols including OPC/UA, MTConnect, Modbus-TCP, TCP/IP, Ethernet/IP, and DeviceNet along with MELSEC, Profibus/Profinet and other proprietary controllers and interfacing protocols.
"Most of the time when automation projects fail it's because the robot is disconnected and can't properly communicate with the machines which minimizes any efficiency gains and can cause quality issues," said Tyler Modelksi, Co-founder & CTO of Flexxbotics. "We understand the complexities of robot-machine communication which is why we developed our breakthrough FlexxCORE technology which delivers broad interoperability to enables the robots to optimize each machine's operation."
Flexxbotics robotic workcell digitalization is the backbone of the Smart Factory, delivering robot-driven manufacturing at scale with autonomous process control for precision machining operations. Flexxbotics' SaaS/hybrid architecture also runs both online and offline so production continues with or without internet access, and Flexxbotics works with existing business systems such as DNC, CAD/CAM, SCADA/HMI, IIoT, MES, ERP, PLM and others for complete synchronization.
A full set of bidirectional communication, transform and routing capabilities are available in Flexxbotics for the robots and DMG MORI machinery that are connected including loading PLC programs, sending instructions, updating parameters and status awareness depending on the equipment's capabilities so the robots drive the machines in the smart factory.
"Global manufacturers are at different phases in transforming to production robotics in the smart factory," said Tyler Bouchard, Co-founder and CEO of Flexxbotics. "That's why Flexxbotics solutions for advanced robotic machine tending can be deployed quickly at scale factory-wide or incrementally one workcell at a time."
About Flexxbotics
Flexxbotics robotic workcell digitalization is the backbone of the Smart Factory delivering autonomous process control for next generation machining environments. Flexxbotics SaaS/hybrid solutions enable robot-driven manufacturing at scale. Flexxbotics breakthrough, the FlexxCORE™ technology, seamlessly connects and coordinates robots with existing automation equipment, IT systems and people. More powerful, flexible and open, Flexxbotics revolutionizes the use of robotics in complex production. Visit www.flexxbotics.com to learn more and follow us on LinkedIn.
Featured Product
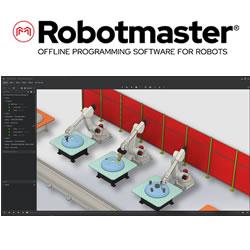