Partnership between RoboDK and KEBA Industrial Automation
The integration of KEBA Robotik KeMotion in RoboDK simplifies the complete life cycle of a process solution with integrated robotics, from the preparation of the quotation to implementation and after-sales support.
The integration of KEBA Robotik KeMotion in RoboDK simplifies the complete life cycle of a process solution with integrated robotics, from the preparation of the quotation to implementation and after-sales support.
RoboDK and KEBA Industrial Automation officially announce their collaboration. RoboDK was founded in Canada in 2015 and specializes in offline programming and simulation. KEBA now has over 30 years of expertise in industrial robotics and, with its Kemro X automation platform, enables perfect interaction between the overall solution, the movement of the robot and the respective process functionalities. Michael Garstenauer, Product Manager Robotics at KEBA Industrial Automation, says: "We are delighted with the successful integration of our control technology into RoboDK. RoboDK has developed a KeMotion KEBA driver that is based on KEBA's new secure and powerful web APIs and thus enables corresponding workflows. Our existing customers will also benefit from this, as the RoboDK Robot Library already supports them."
Benefit from two open platforms
OEM developers can now combine the advantages of Kemro X and RoboDK. The two open platforms make it possible to create and test several robot cell scenarios from the desktop and only then set up the real production cell. This means that the optimum positioning of the robot can be determined before it is actually used. Cycle times are minimized, singularities are avoided and accessibility is ensured. This leads to shorter commissioning times, conserves employee resources and ultimately allows reliable quotations to be prepared quickly for customers. Garstenauer says: "If, for example, you program a robot to paint a complex 3D structure such as a designer chair, this can often take hours - with RoboDK you can do this in just a few minutes."
Simple transfer to KEBA control unit
The currently available functionality enables the creation of robot programs in the KEBA language KAIRO within the RoboDK environment based on 3D models of parts and systems. A simple option for transferring to KEBA controllers is also available. The execution of the robot movement can be monitored both in a digital environment and with the actual robot controller within RoboDK.
Advanced simulation and programming function
Samuel Bertrand, Software Development Lead at RoboDK, says: "The integration between Kemro X and RoboDK provides KEBA users with advanced simulation and programming capabilities, including CAD to path features, offline programming (OLP), digital twin capabilities, collision checking, CAM for robots, and more. By integrating KEBA systems into RoboDK, we aim to enhance efficiency, control, and flexibility in robotic automation. "
Easy maintenance thanks to digital twin
Even after the production cell is set up and running, it can be easily maintained or modified using the digital twin. The recorded data makes it easy to quickly identify problems and provide efficient customer support and service. The collaboration between KEBA and RoboDK is also of great benefit to end users: It minimizes downtime during product changes and by quickly identifying problems, it guarantees them effective service & support.
The main advantages and key points of the collaboration between KEBA and RoboDK include:
• Advanced simulation: Enables users to create and test robot cell scenarios virtually, in a simulated environment, ensuring optimal positioning and performance before real-world implementation.
• Reduced setup times: Minimizes commissioning times and conserves employee resources by simplifying programming tasks and setup procedures. Key feature is the automatic generation of robot paths along for new parts or products to be processed by the robotic system. Hour long manual teach-in at the robot is replaced by quick and easy software-driven processes.
• Enhanced monitoring and maintenance: Facilitates easy monitoring and maintenance using digital twins, ensuring quick identification and resolution of issues.
• Reliable and efficient support: Guarantees effective customer service with minimized downtime during product changes and swift problem-solving capabilities.
About RoboDK
Founded by Albert Nubiola in January 2015, RoboDK is a spin-off company from the highly prestigious CoRo laboratory at ETS University in Montreal, Canada. RoboDK software is designed to bring powerful robotics simulation and programming capabilities to companies large and small and to coders and non-coders alike. Today, it supports more than 1000 robots from over 80 different manufacturers, including ABB, Fanuc, KUKA, Yaskawa/Motoman, Stäubli, Omron, and Universal Robots.
https://robodk.com/
https://robodk.com/partners
About KEBA Industrial Automation
KEBA, founded in 1968, with headquarters in Linz (Austria) and subsidiaries worldwide, operates in three business areas: Industrial Automation, Handover Automation and Energy Automation. Controls and safety technology, drive technology for machines and robots, ATMs and parcel and transfer machines, as well as power charging stations for e-cars and heating controls, for example, are all part of the product portfolio of the automation expert, which employs around 1800 people.
In the area of industrial automation, in line with the guiding principle "Automation by innovation", KEBA develops and produces innovative and high-quality automation solutions for general machine and tool construction as well as for Intralogistics, robotics, plastics, wind energy, turbo systems and sheet metal processing. Whether hardware or software, individual components or complete solutions - the Austrian technology expert offers powerful, modular and safe solutions for all industrial requirements.
https://www.keba.com/industrial-automation
https://www.keba.com/en/industrial-automation/lp/robodk-und-kemotion
Featured Product
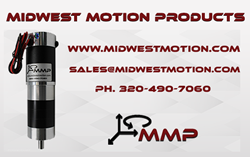
Midwest Motion Products is a leading provider of robust and reliable Motion Control Products.
MMP specializes in supplying high-quality Brushed & Brushless DC Motors & Gearmotors for Robotics and Automation Equipment with a wide range of motor windings and gear ratios. With an impressive track record of more than 8,000 released DC Gearmotors designs and over 2,000,000 individual part numbers, we are renowned for our ability to handle large-scale orders. Due to our huge on-hand inventory, we are also well known for lightning-fast delivery of our standard products. We take pride in our dedicated customer service and our team of knowledgeable sales and engineering experts who are ready to assist you with custom design solutions tailored to your specific application. Additionally, we also offer a wide range of complimentary products, such as DC Motor Controls, DC Linear Actuators, AC-DC power Supplies, and DC Servo Amplifiers and others.