Transforming Laser Marking Operations with Collaborative Robotic Automation
FOBA Laser Marking + Engraving works with Flexxbotics and Universal Robots to enable companies to achieve highest throughput and optimum marking quality. In August, the three companies will host an event where they will provide insights into practical implementation of robotic assisted laser marking.
Selmsdorf/Wood Dale, July 2024 - Laser marking and engraving is critical for unique part identification (UID), compliance, and branding. However, capacity constraints and labor shortage issues can create serious throughput challenges. To increase output and improve profit per part, forward thinking manufacturers are transforming their laser marking operations with advanced robotic machine tending. FOBA Laser Marking + Engraving works with Flexxbotics and Universal Robots to enable companies to achieve highest throughput and optimum marking quality. In August, the three companies will host an event where they will provide insights into practical implementation of robotic assisted laser marking.
Laser marking is a critical stage of the value stream for a product in many manufacturing processes. Bottlenecks can cause serious delivery problems and any mistakes can render the product unsellable. By introducing collaborative robotic automation with lean manufacturing principles, laser marking processes can be improved to maximize throughput, assure quality, and reduce waste.
"Connecting robotic machine tending with our FOBA laser marking solution using Flexxbotics provides an even greater Return on Investment," states Jeffrey A. Kniptash, FOBA's Sales Manager for Americas. "Enabling Flexxbotics robot-driven manufacturing with our FOBA laser marking and engraving equipment to enable autonomous process control can remove bottlenecks and deliver continuous operation."
Utilizing collaborative robots from Universal Robots with Flexxbotics digitalization technology, companies running FOBA's laser marking and engraving machines can increase the machine-to-man ratio to 10:1 or more and run ‘lights out' safely. Thus, they will benefit from additional capacity, highest precision, optimum marking quality and improved profit margins. Flexxbotics includes communication with FOBA's integrated camera system for vision-based inspection providing closed-loop feedback to the robot for autonomous process control. FOBA's three-stage laser marking process HELP (Holistic Enhanced Laser Process) which includes part inspection prior to marking, automatic mark alignment, and subsequent validation of the marking is coordinated with the robot actions. Flexxbotics utilizes either the Intelligent Mark Positioning (IMP) or Point & Shoot (P&S) capabilities in the FOBA equipment for precise alignment of the laser marker on the customer's product along with vision-assisted workflows for unmatched accuracy.
"Combining FOBA with Flexxbotics is particularly valuable in industries with strict regulatory compliance requirements that dictate the highest levels of repeatable precision such as medical devices and surgical products along with aerospace, defense and space," explained Tyler Bouchard, Co-founder & CEO of Flexxbotics. "Environments that require rapid and accurate processing like semiconductor and electronics operations also benefit substantially. With Flexxbotics and FOBA together customers can optimize cycle-time, expand capacity and increase profit per part."
Universal Robots, Flexxbotics and FOBA give an insight in automated laser marking in a half-day event on Thursday, August 1, 2024 in Boston with a live demonstration of a cobot-enabled FOBA laser marking workstation, best practices and proven approaches to real-world applications. Sign up at event details and registration page. https://tinyurl.com/Foba-UR-Flexx1
Featured Product
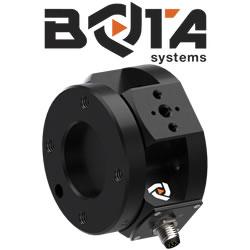