Enhancing Equipment Reliability: Implementing xPump – AI/ML based pump monitoring & predictive maintenance system on the EH Mechanical Booster Pump EH1200C
In today's industrial landscape, the reliability of equipment is paramount. Unexpected breakdowns can lead to significant financial losses, production disruptions, and safety hazards. This is particularly true for critical equipment like the EH Mechanical Booster Pump EH1200C, which plays a vital role in various industries such as water treatment, oil and gas, and manufacturing. To address these challenges, innovative solutions like xPump - an AI/ML based pump monitoring and predictive maintenance system - are emerging as game-changers.
In today's industrial landscape, the reliability of equipment is paramount. Unexpected breakdowns can lead to significant financial losses, production disruptions, and safety hazards. This is particularly true for critical equipment like the EH Mechanical Booster Pump EH1200C, which plays a vital role in various industries such as water treatment, oil and gas, and manufacturing. To address these challenges, innovative solutions like xPump - an AI/ML based pump monitoring and predictive maintenance system - are emerging as game-changers.
This blog delves into the importance of pump reliability, the challenges faced by industries, and how xPump can revolutionize equipment maintenance for the EH1200C pump.
The Critical Role of Pumps in Industrial Operations
Pumps are the workhorses of many industrial processes. They are responsible for transporting fluids, ensuring consistent flow rates, and maintaining pressure levels. The EH Mechanical Booster Pump EH1200C, in particular, is designed for heavy-duty applications, delivering high-pressure water for various industrial needs. However, these pumps are complex machines susceptible to wear and tear, making them prone to breakdowns and inefficiencies.
Challenges in Pump Maintenance
Traditional pump maintenance practices often rely on reactive measures, such as scheduled maintenance or breakdown repairs. This approach can lead to several challenges:
Unplanned Downtime: Unexpected pump failures can disrupt operations, leading to significant financial losses and production delays.
Increased Maintenance Costs: Reactive maintenance is often more expensive than preventive measures, as it involves emergency repairs and overtime labor.
Reduced Equipment Lifespan: Operating pumps beyond their optimal limits can accelerate wear and tear, leading to premature equipment failure.
Safety Risks: Malfunctioning pumps can pose safety hazards to personnel and the environment.
The Power of AI/ML in Pump Monitoring
To overcome these challenges, industries are turning to advanced technologies like AI and ML. xPump is an AI/ML-based pump monitoring and predictive maintenance system designed to optimize pump performance and reliability.
How xPump Works: A Deep Dive
xPump leverages a combination of sensors, data analytics, and machine learning algorithms to provide comprehensive insights into pump health and performance. Here's how it works:
Sensor Integration: xPump integrates with various sensors installed on the EH1200C pump to collect real-time data on parameters such as vibration, temperature, pressure, flow rate, and power consumption.
Data Acquisition and Processing: The system continuously collects and processes sensor data, creating a detailed historical record of pump behavior.
Anomaly Detection: Advanced AI algorithms analyze the data to identify abnormal patterns or deviations from normal operating conditions, indicating potential issues.
Predictive Maintenance: By leveraging machine learning, xPump can predict the likelihood of equipment failure, allowing for proactive maintenance actions to be taken.
Real-Time Monitoring: The system provides real-time alerts and notifications for critical issues, enabling prompt responses and minimizing downtime.
Performance Optimization: xPump analyzes pump performance data to identify opportunities for improvement, such as optimizing pump settings or reducing energy consumption.
Benefits of Implementing xPump
Implementing xPump on the EH1200C pump offers several significant benefits:
Enhanced Equipment Reliability: By predicting potential failures, xPump helps prevent unplanned downtime, ensuring continuous operations.
Increased Operational Efficiency: Optimized pump performance and reduced energy consumption lead to improved operational efficiency and cost savings.
Extended Pump Lifespan: Early detection of issues allows for timely maintenance, prolonging the pump's lifespan.
Improved Safety: Proactive identification of potential hazards reduces safety risks for personnel.
Data-Driven Decision Making: xPump provides actionable insights to support informed decision-making regarding pump maintenance and operations.
The Future of Pump Monitoring with xPump
As technology continues to evolve, we can expect further advancements in AI/ML-based pump monitoring systems. Future developments may include:
Integration with digital twins for virtual simulation of pump performance.
Advanced anomaly detection using deep learning algorithms.
Predictive maintenance models that incorporate external factors like weather conditions and load variations.
Integration with augmented reality for remote equipment diagnostics.
By embracing these innovations, industries can achieve even greater levels of efficiency, reliability, and sustainability in their pump operations.
Featured Product
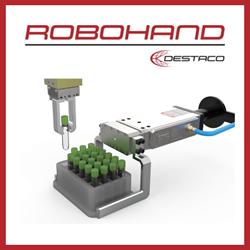