What Technologies Is Amazon Developing to Keep Workers Safe?
People commonly think of Amazon as an innovative company, and for valid reasons. After all, it got online shoppers accustomed to the option of two-day deliveries on most of its goods and introduced the world to the Alexa assistant and the associated line of smart speakers.
The company also gains attention for how it uses robotics in its massive facilities. Getting that help from robots is crucial given the number of orders coming and the fulfillment speed necessary to keep consumers happy.
Although these machines boost profitability by raising output, they also keep workers safer by relieving them of repetitive movements and some hazardous duties. The company has dedicated robotics and advanced technologies labs and hires specialists to develop and test possibilities. Here are some of the latest robotic creations made to improve worker safety at Amazon.
Supporting Ergonomic Positioning
Repetitive bending, twisting and reaching could put workers at a higher risk of injury, especially if they don’t keep their bodies properly aligned. Warehouse jobs are strenuous, and improper movements increase a person’s risk of strains, sprains and fatigue. The U.S. Bureau of Labor Statistics (BLS) recorded more than 27,000 injuries requiring stockers and order fillers to take time off from work in 2019.
Poor ergonomics did not cause all those issues, but it’s safe to say they were a contributing factor in many of them. Amazon hopes to reduce ergonomic injuries with a workstation accessory called Ernie.
Ernie is a robot that collects totes from robotic shelves and gives them to employees. That functionality improves worker comfort and stability. Plus, it’s an ergonomically friendly innovation that should reduce how much Amazon’s team members have to bend and reach.
Kevin Keck, Amazon’s worldwide director of advanced technology, noted, “The innovation with a robot like Ernie is interesting because while it doesn’t make the process go any faster, we’re optimistic, based on our testing, it can make our facilities safer for employees.”
Reducing Excessive Movement
Amazon warehouses are huge facilities that require employees to do miles of walking per shift. It’s impossible to eliminate all that foot travel, but Amazon’s robotics experts hope to minimize it.
The company is testing an autonomous mobile robot (AMR) called Bert to carry heavy items for employees and potentially handle several at once. Bert is one of the first AMRs developed and used at Amazon. The robot has specialized sensors that let it avoid obstacles and safely navigate its environment — which is essential, considering how busy the company’s warehouses are.
Developers hope Bert can eventually hold the carts that people use to move goods while working at Amazon. There may be a time when workers could summon Bert to retrieve something for them, allowing the humans to stay focused on other tasks. If such situations become realities, employees could cut down their travel time and reduce the strain that causes injuries.
Implementing Risk Management in Materials Handling
Keeping workers safe in a warehouse involves engaging in various risk management practices. Here’s a closer examination of two used at Amazon, including one related to how and why the company builds robots.
Building Special Storage Facilities for Dangerous Goods
Some risk management procedures relate to protecting people from potentially dangerous items. Amazon sells millions of products, and the total increases even more with the number of third-party Amazon Marketplace sellers that use the company’s Fulfilled by Amazon service. A report indicated that more than 450,000 parties relied on it from May 2019-2020.
Since the company offers such a vast product range, some items are naturally classified as hazardous goods. The U.S. Department of Transportation (DOT) requires shipping those products in DOT-approved containers. There are nine main categories of dangerous products. They include flammable items, poisons and radioactive materials.
Several years ago, Amazon began building dedicated warehouses for those items as a safety measure. The people working in them can get specialized training or attire to help them avoid possible complications from working in those centers.
Reducing Risks With Product-Handling Robots
Limiting risks in materials handling also comes into play when the company’s workers interact with robots. For example, Robin, one of Amazon’s newer robots, complements depalletizers. Advanced technologies let the machine recognize and sort packages. Robin is a robotic arm that can grab parcels, then rotate and scan them to learn the ZIP code of their destinations.
Tye Brady, a chief technologist at Amazon Robotics, discussed how safety is a defining principle with its robot designs. “We don't just build a robot and then say, 'Hey, safety people, I want you to get involved now. Instead, safety engineers are there every step of the way, from design and deployment to maintenance and operation. They're at the table talking with us about how we can make it a better experience for our employees,” Brady clarified.
Clay Flannigan, the technical lead for Robin’s development, added, “We work hard to identify any potential hazards. That could be anything from limiting any risk for contact between people and the robot, tripping on a floor cable or a sharp edge on a barrier. Ideally, we can eliminate them with multiple engineering mitigations.”
Some of Amazon’s robots work directly alongside humans without barriers. However, that’s not true with Robin. That bot has fencing and an operator gate to cut the risks accompanying any gigantic piece of machinery. It, like all of Amazon’s robots under development, also gets thoroughly tested before real-world deployment. In Robin’s case, that means going through a 1,000-package test run.
Minimizing Collisions
Amazon also has a pair of autonomously guided carts (ACG) in development, named Kermit and Scooter. Workers already frequently use carts to move items from place to play. However, company representatives envision that bringing robots into the picture will keep employees safe while letting them focus on higher-value tasks.
Amazon intends to use them to move empty packages and totes. Since these robots have advanced sensing technology, company representatives believe the robotic carts will cut down on the collisions sometimes associated with manual maneuvering while also reducing employee strain.
Scooter is in an earlier development phase than Kermit. However, the company still plans to roll out that robot at one or more of its fulfillment centers later in the year. Kermit follows strategically positioned magnetic tape on the ground when moving. It also responds to tags spread out along the path that tell the robot to speed up, slow down or alter its course.
Amazon has already brought Kermit to several of its sites in the United States. It plans to use it in at least a dozen more North American locations throughout 2021.
Studying Machine-Human Interactions
Many other major brands look to Amazon for inspiration when considering how to use robots in their operations. That’s likely because the e-commerce giant uses more than 200,000 in its facilities and processes, giving other companies plenty of ideas. Amazon also brings in experts to spur progress and solve problems. One such initiative is the Amazon Scholars program, which targets academics and lets them continue teaching in addition to working at Amazon.
Bill Smart is a current program participant interested in how robots and humans perform in shared surroundings and improving future machine movement capabilities. His work could develop safer, more advanced robots.
Smart discussed how Amazon opens new opportunities. He described how a typical academic study involving robots might have 30 people taking part, but each interacts with the robot individually. Such isolated engagement doesn’t accurately represent the hundreds of people the machine would encounter during a single warehouse shift.
“As an academic, I can run a few robots for a few days and do what essentially amounts to proof-of-concept studies,” Smart said. “Working with robots at Amazon, it’s possible to think on a larger scale for months and years at a time. This lets you ask questions that you just can’t as an academic.” One of Smart’s priorities is to improve robot signaling.
He explained, “Currently, the robots we're working with have a set of indicator lights, similar to a car, that show the intent of the robot. The underlying safety systems on the robot will cause it to slow or stop. But the ultimate goal is to have the robots be ‘invisible in use’ so that the employees don’t have to think about them any more than they think about the actions of their human colleagues.”
A Bright Future for Amazon Robots
Amazon continually unveils robots that make its facilities safer places to work. These are some of the newest advancements, but more are certainly on the way. As the company continues announcing its latest innovations, it’ll cement its status as one of the most forward-thinking e-commerce companies in terms of technological advancements.
Comments (0)
This post does not have any comments. Be the first to leave a comment below.
Featured Product
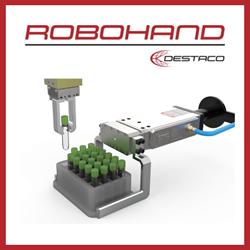