Industrial robots – the perfect worker?
According to the World Robotics 2021 Industrial Robots report by the International Federation of Robotics (IFR), America ranked third globally for the installation of industrial robots in 2020, with 39,000 units installed. The Asia and Pacific region led the way with 266,000 installations and Europe sat in second place with 68,000. The same report showed the US ranked sixth in the world for robot density, with 255 robots per 1,000 employees. Here, Claudia Jarrett, US country manager for industrial automation supplier, EU Automation, explains why US industry should continue to bolster automation to alleviate its labour shortage.
Solving the labour shortage
America’s labour shortage is well documented, and the agricultural industry provides a clear example of the challenges of poor staffing. The number of American farms has been steadily decreasing since 2007 from 2.2 million to 2 million in 2020. Conversely, the number of temporary agricultural visas granted by the federal government has quadrupled since 2007, highlighting the increasing struggle of labour shortage for farms.
Britain, a nation which happens to only install 2,200 industrial robots a year, faced a similar problem in 2021, where labour shortages in agriculture left produce rotting in the field. Collaborative robots (cobots) are already providing solutions, with one example being automated fruit pickers. These machines use computer vision, a form of AI, to identify ripe fruit and then pick it using gippers, suction cups, or sometimes miniature sawblades. Commercial options are slowly being realised too, with Robotic Plus’s kiwi fruit picker; pepper picking Sweeper robot; and the strawberry picking Agrobot. Only a handful of experienced farmers would need to monitor the operations of these cobots, simultaneously solving labour shortages and increasing yield.
Automation apprehension
The advantages of automation are clear, so why is the US behind other developed countries for robot deployment? A controversial proponent of adopting automation is the idea that it will take away jobs from humans, leading to exponential unemployment. However, this isn’t necessarily true.
The electronics industry provides a stark example where robotics has not led to catastrophic redundancies. The electronics industry is the biggest employer globally with 17.4 million people currently employed in 2022. Interestingly, electronics is also the biggest industry for installations of industrial robots, with 109,000 in 2020.
The use of industrial robots in electronics manufacturing is vital for repeated precision for coating and populating circuit boards, assembling connectors, and handling components. That said, the human element for the industry is equally important. Engineers are crucial for data analysis design, software development and maintenance.
While robots may take some menial jobs — like ever-vacant agricultural picking roles mentioned earlier — this frees up workers to engage in more fulfilling and creative roles.
It is found that human jobs are most likely threatened in the companies that are late to automate, as they struggle to compete with production of adopters, resulting in the need to reduce their workforce. On the other hand, those that adopt robotics early record a spike in productivity and output, leading to bolstered growth and an increased potential to hire new staff. While a change in worker composition is noted, there is an overall net gain for job opportunities.
Costs and obsolescence
The expensive cost of units and integrating them into the production line can be a deterrent for manufacturers to adopt industrial robots. Although the face value cost is high, the return on investment (ROI) can be significant.
Unsurprisingly, there are also often concerns about obsolescence in robotics. The industry is constantly advancing and producing new models, which can be daunting for those hoping to invest in their first robot. For manufacturers in this position, it is recommended to invest in a traditional industrial robot model, such as a six-axis, SCARA or Cartesian — rather than experimenting with a newer robot variety, like the aforementioned cobots. Equally, obsolete robots and their parts are also available from credible suppliers such as EU Automation.
US manufacturers needn’t be daunted by the upfront cost of industrial robots when the ROI can be high. Increasing the number of installed industrial robots across the US will help manufacturers remain competitive globally with increased production potential. Bolstering automation in a variety of industries such as agriculture and manufacturing can alleviate labour shortages pressuring businesses. Investing in traditional and more simple models can reduce the face value cost for business whilst increasing efficiency. Credible suppliers such as EU Automation able to supply obsolete warrantied parts for older models diminish the stress of faults and the losses from unplanned downtime.
For further information visit https://www.euautomation.com/ .
Comments (0)
This post does not have any comments. Be the first to leave a comment below.
Featured Product
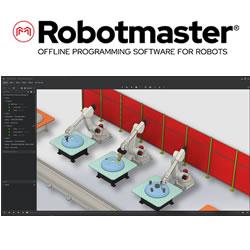