Navigating the World of Cartesian Robots: Essential Tips for Selecting the Ideal Automation Tool
Unlocking the potential of automation in manufacturing begins with selecting the right tools. Among the many options of automation technology are cartesian robots, known for their precision and flexibility. However, with so many options available, choosing the ideal cartesian system for a specific application can feel daunting.
In this article, explore 5 key considerations for simplifying the decision process when selecting the correct cartesian robot.
What are cartesian robots?
Cartesian robots (or gantry robots) are a type of robotic system commonly used in manufacturing and automation. These systems operate on a cartesian coordinate axis system, which is a three-dimensional grid system with X, Y and Z axes. These devices are used for a wide variety of automation applications.
Common applications for cartesian robots
One common application of this technology is pick and place operations. A cartesian multi-axis systems can precisely pick up objects and place them in the desired location, making them useful for assembly lines, material handling tasks, and even packaging.
These versatile robots can also be programmed to move heavy materials or components along multiple axes with impressive precision and speed. The technology has also been known to assist with inspection and quality control, being equipped with sensors and cameras to inspect products for defects, ensuring quality control throughout the manufacturing process.
The robots have also been used in numerical control (CNC) machines for milling, cutting, and engraving operations, allowing for precise fabrication for parts and components. Gantries are also extremely beneficial in the raw and processed material handling stages of a CNC production cell.
Cartesian systems are also known for their exceptional precision, capable of positioning tools or components with accuracy down to micrometer or even nanometer scales. This precision is crucial in automation projects because it ensures consistent and reliable performance by minimizing errors and variability in manufacturing processes. In industries such as semiconductor manufacturing or precision machining, even slight deviations from the desired specifications can result in product defects or performance issues. By achieving precise control over movement and positioning, cartesian systems enable manufacturers to maintain tight tolerances, enhance product quality, and ultimately drive efficiency and competitiveness in the market.
Ultimately, cartesian robots have a lot of applications in a variety of industries, so understanding your specific application is a necessary step in selecting the best possible cartesian robot system for smooth operations.
Selecting the right cartesian systems
When selecting a Cartesian system for a specific task, several factors should be considered to ensure optimal performance and suitability. These factors include:
- Required precision and accuracy
- Size and weight of objects being handled
- Speed and throughput requirements of the task
- Ease of programming
- Integration with existing automation processes and available workspace
- Versatility and the flexibility to adapt to future expansions
At its core, an in-depth understanding what the system will be handling is key to selecting the correct cartesian robot. It’s this key factor that explains why the first three listed factors encompasses task details such as required precision and accuracy, size and weight of objects, and the speed and throughput requirements.
With the latest cutting edge cartesian technology, end users no longer need expertise in ladder logic or other complex programming techniques to create and modify programming code. Selecting a cartesian multi-axis system with simplified programming means coding expertise is not one of the factors that needs to be considered for selection and can increase implementation timelines.
Cartesian systems are highly versatile and should be capable of handling a wide range of tasks across various industries. When evaluating systems, look for a modular design that allows for easy customization and scalability to meet evolving production needs. This will provide long-term flexibility and investment protection. End-of-arm tooling modifications or additions to sensors and feedback devices are all changes that can easily be made to the system, which help them adapt to changing needs. Program changes should be simple to make and can be stored in the system’s memory, allowing recall of past programs to be accomplished within seconds. These adaptations mean that while a system may be selected for a specific task, should that task change, the cartesian robot can change with it.
Consider the implementation timeline
Another consideration is the implementation timeline. In other words, how fast can these systems be fully operational. Designing, configuring, commissioning and programing these multi-axis systems can be regarded as a time-consuming process, but with the use of turnkey solutions such as Smart Function Kits, the process can be drastically simplified. These kits provide easy to use interfaces and automated drive-to-motor commissioning, all while still offering the ability to connect to third party controls and higher-level systems. Utilizing these kits can save engineers and technicians up to 80% of the typical time they would spend commissioning and programming the cartesian system.
Cartesian robots revolutionize the Factory of the Future
With advancements in technology, such as improved motor controls and sensor integration, cartesian multi-axis systems are becoming more intuitive and responsive, leading to enhanced productivity and reduced downtime. Additionally, these systems generate a wealth of data, including positional, velocity, acceleration data, and sensor data that can provide feedback on the environment and task status.
These advancements and data generation make cartesian systems imperative to the Factory of the Future. By selecting the correct system, you can elevate your organization with enhanced data collection and precision. The integration of artificial intelligence and machine learning algorithms further optimizes these systems, enabling predictive maintenance and adaptive control, ensuring continuous operations and minimizing disruptions. As a result, cartesian multi-axis systems are poised to revolutionize the Factory of the Future, driving innovation and empowering manufacturers to achieve new levels of efficiency and competitiveness in the global market.
When selecting a cartesian system for a particular task, it’s important to keep in mind the adaptability of these robots. As your automation demands change, so can the system. This makes cartesian robots extremely valuable as more manufacturers enter the Factory of the Future, constantly adapting to new technologies. While it’s important to select the correct system by considering the various factors outlined above, the ease of adaptation protects your investment.
Comments (0)
This post does not have any comments. Be the first to leave a comment below.
Featured Product
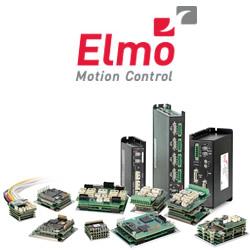