Can Robotics Truly Drive Down Energy Costs?
Manufacturers face rising pressure to reduce their power consumption. Factory automation is a common solution in energy-efficient manufacturing, but organizations must consider where these savings come from. Taking a more skeptical approach to robotics will help businesses ensure their Industry 4.0 initiatives actually produce the desired results.
The use of robotics in manufacturing has benefits far beyond efficiency. As such, this technology can be a sound investment even if it does not deliver significant electrical consumption reductions. Still, if efficiency is a primary driver behind robot adoption, brands must confirm automation’s ability to drive down costs before implementing it.
How Does Factory Automation Save Energy?
Some businesses may be skeptical of robots’ ability to reduce power expenditures because these machines consume power themselves. However, they can reduce overall electricity consumption in several ways.
Higher Efficiency
Much of factory automation’s energy savings stem from their productivity. Robots can accomplish more work in less time than humans, resulting in lower total tool time for the same level of output. These improvements are often substantial, too — some manufacturers have increased their throughput by 300% after implementing collaborative robots.
While those cobots undoubtedly introduced new electrical needs, the jump in utility expenses wouldn’t equal such a considerable hike in productivity. Consequently, the overall electrical price per product would fall in such a facility.
These savings are easier to understand in light of the fact that manual processes are not passive. Without automation, human workers use similar tools to those in a robotic system, but they would have to run them longer to achieve the same results. Comparing the two approaches this way highlights the potential for robots in energy-efficient manufacturing.
Fewer Errors
Automation also makes fewer mistakes than human workers. Even the most experienced employees can get tired or distracted. When they do, they’re likely to create errors leading to scrap, rework and related downtime. While each of these instances may seem small, they add up to significant power expenditures over time.
Manufacturers disposed of 1.33 billion pounds of waste in 2022 and directed another 14.33 billion pounds to recycling. While recycling does reduce upstream electricity consumption, it’s still preferable to prevent scrap in the first place, as recycling requires some power itself. These figures suggest manufacturers waste a considerable amount of their resources, but automation can reduce that figure.
Even a marginal reduction in errors means manufacturers need less energy to collect, transport and recycle wasted materials. It also ensures greater overall efficiency because workflows do not need to stop or produce more to compensate for a defect.
Building Automation
Enterprises must also consider that factory automation covers more than just production floor robots. It also includes building process automation like smart HVAC solutions and other Internet of Things (IoT) functionality. These use cases enable energy-efficient manufacturing by minimizing less direct sources of wasted power.
HVAC automation adjusts heating and cooling levels in response to real-time temperature and humidity readings. Such precision lets them turn off if conditions have not changed and avoid unnecessary operations a schedule-based alternative may incur. As a result, they ensure facility environments remain optimal while using as little electricity as possible.
Manufacturers can reduce HVAC power consumption by 3.2% through IoT-based systems. While these gains may be marginal, they provide more room for the extra electricity robots consume. These reductions, in turn, maximize robotics’ efficiency benefits.
How Factory Automation May Increase Energy Costs
These benefits are impressive, but manufacturers must view them in relation to robots’ power consumption. While the use of robotics in manufacturing can produce significant savings, these machine’s own electrical usage is an unavoidable caveat.
In some cases, robots may increase a factory’s electricity expenses — especially if the organization does not plan its automation carefully. Automation’s efficiency can hit a point of diminishing returns if manufacturers use more bots than necessary. Industrial robots account for 8% of all energy consumption in some sectors, so they can only reduce electrical costs with proper implementation.
Robotic inefficiencies are more likely to arise if facilities use them where they’re least impactful or deploy the wrong kind of robot. Using a heavier or faster robot where a process does not require as much strength or speed will create excessive power withdrawals. Similarly, an autonomous mobile robot may be unnecessary if it’s marginally faster than manual material handling.
Steps to Maximize Robotic Energy Efficiency
Manufacturers must approach factory automation carefully to ensure it saves power instead of using more of it. A good first step is to turn to an energy consultant. These professionals can lower total electricity costs by helping organizations understand their current usage trends and find areas to improve before implementing automation.
After these initial optimizations, manufacturers should compare robotics solutions to their existing needs. It’s important to look at options from multiple vendors and use site-specific data to ensure they right-size the bot to the task. These comparisons include noting a robot’s average power consumption and its projected impact on productivity.
Businesses can adjust their workflows to minimize wait times between robot operating cycles. Streamlining the production line this way will ensure the automated system reaches its full cost-saving potential. Similarly, technicians must calibrate the equipment according to OEM recommendations and regularly monitor its performance.
Proactive maintenance is another key part of energy-efficient manufacturing. A reactive approach can increase power costs by up to 60% and decrease equipment life span. By contrast, preventive repairs will ensure robots sustain peak performance for longer, producing more significant electricity savings.
Finally, manufacturers must inspect workflows to determine if manual processes may be more efficient. Complex, less repetitive or predictable tasks are typically better to assign to humans. Similarly, if robots will be more efficient but not by a wide margin, automation may not be the best option.
Robots Play a Key Role in Energy-Efficient Manufacturing
The use of robotics in manufacturing can do more than boost throughput. It can also minimize energy spending, but only with thoughtful planning and implementation.
Attention to these details will help organizations get more out of their automation investments. They can then pave the way for a more sustainable and cost-effective future.
Comments (0)
This post does not have any comments. Be the first to leave a comment below.
Featured Product
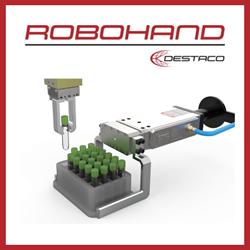