An enormous warehouse necessitates mapping of thousands of positions, and for the system to track order numbers and individual products on the pallets while transmitting information wirelessly back to the central control room for collection and monitoring.
Cincoze DI-1000 Drives AGVs in Factories and Warehouses

Case Study from | Cincoze
Our customer, a European automated guided vehicle (AGV) manufacturer, is a leading global supplier of AGVs for logistics and material handling tasks in warehouses, distribution centers, and manufacturing operations worldwide. It helps its customers to develop AGV and logistics robot solutions by offering hardware, navigation technologies, and software services. AGV system performance continues improving, with evolving technologies like sensors, wireless networks, and automatic control, enabling AGVs to complete many different tasks.
Our client had a project to design new AGVs in which the control system has progressed from simple relay logic to a highly sophisticated PC-based controller. High-performance computing and robust system design are required to ensure the AGV’s capability to complete autonomous operation in complex and dynamic warehouse environments.
Customer's Requirements
High Performance
For complex orders in the warehouse, like pick and dispatch, the processing requirements are formidable. There are two laser cameras fixed to the AGV, one on the front for object detection, and another at the center for accurate positioning. An enormous warehouse necessitates mapping of thousands of positions, and for the system to track order numbers and individual products on the pallets while transmitting information wirelessly back to the central control room for collection and monitoring. For these intensive processing tasks, a powerful embedded computer with rich interfaces to connect to cameras, motors, and wireless networks is necessary.
Low Energy Consumption
AGVs require rest periods to recharge batteries, so the longer they spend in the charging station, the less time they are working. The control embedded computer must have low power consumption to maximize battery life and, in turn, the time between charges, keeping the AGV productive.
Compact Size
The warehouse environment has massive amounts of storage racks and narrow aisles that require many tight turns for an AGV. A small AGV can navigate easier, so to keep the size down, the embedded computer control system in the AGV must also be compact enough for integration.
Why Cincoze?

High Performance, Small Size
With minimal dimensions of 203 x 142 x 66.8 mm, the DI-1000 can easily be installed in a machine or other space-constrained application. The DI-1000 uses Intel® Core™ i3/i5/i7 mobile CPUs, with 15-watt power consumption, providing unbeatable performance to handle AGV navigation, movement, and control functions. It packs a rich I/O, including DVI-I, DP, 2 x LAN, 6 x COM, 6 x USB, and 8 x DIO. Additional I/O and functions include more LAN ports, PoE, M12 connections, and power ignition sensing through CMI and CFM modules.
Wireless Connectivity
The DI-1000 comes with two full-size Mini PCIe slots for WiFi connectivity to easily connect to a central control room, cloud systems, or wirelessly communicate with nearby devices. It also supports 4G LTE for long-distance data transmission in larger warehouses or outdoors.
Robust Design
AGVs are always on the move. The DI-1000 inherits the rugged design DNA from Cincoze, featuring fanless and cableless design, outstanding thermal performance, and high shock and vibration tolerance (50/5G). It can operate from -40°C to 70°C, suitable for both cold storage for food and medical industries.
The content & opinions in this article are the author’s and do not necessarily represent the views of RoboticsTomorrow
Comments (0)
This post does not have any comments. Be the first to leave a comment below.
Featured Product
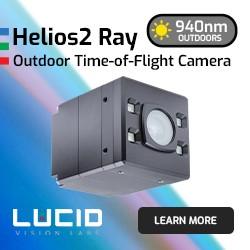