The M55 rocket stockpile was successfully destroyed without any major incidents. With so many complex systems, processes, and disposal procedures, the Robosuits played a key role in ensuring that all of the careful planning and timing would not be disrupted.
Special Agents: Chemical Weapons Disposal Done Right

Case Study from | Roboworld
OVERVIEW
Project Goal: Dispose of 50,000+ M55 rocket projectiles that contained more than 523 tons of chemical agent
Protection Parameters: Caustic chemical washdown agents, lethal nerve agents
Facility Type: Indoors
Companies Involved: CRG Automation, Amentum, Bechtel, Blue Grass Army Depot, Department of Defense, Roboworld
Location: Blue Grass Army Depot, Richmond, Kentucky, USA
Timing: Started in June 2019, completed in July 2023
BACKGROUND
After the Chemical Weapons Convention in 1993, a treaty was signed that required all participating countries, including the US, to destroy their chemical weapons stockpiles in a safe, effective way. These rockets contained lethal and volatile mustard agents, VX nerve agents, or GB nerve agents.
In addition, due to the projectiles being stored for a prolonged period of time at separate storage facilities in different climates, some of the rocket casings had warped and some of the chemical agents had congealed. Due to the complex nature of this project, the disposal process was far behind schedule before CRG was brought in, but the treaty deadline of September 2023 had not moved.
CHALLENGE
Destroying chemical weapons leaves no room for error. It requires specific processes, technology and expertise to achieve the goal of safely destroying a chemical stockpile of munitions that were never meant to be disassembled. Given the parameters and the timing, a full-proof yet nimble disposal protocol had to be developed that allowed for immediate emergency washdowns if a leak occurred.
A punch-and-drain system was developed, where the nerve agent was removed by a controlled puncture of the munition cavity to allow for the nerve agent to drain into a specialized mixture of water and caustic solutions resulting in hydrolysate. The munition was then moved on a conveyor to a controlled static detonation chamber (SDC).
While this process was safe and effective, any leakage would trigger the disbursement of a proprietary caustic chemical washdown to decontaminate the nerve agent. These cleaning agents could severely damage the robots, resulting in a complete facility shutdown which would cost thousands of dollars for every minute/hour/day it was not operational as well as make the approaching deadline untenable. To insure against this, CRG outfitted their specialized robots with Roboworld’s Robosuits®.
SOLUTION
To stay one step ahead of an emergency event or routine cleaning, Robosuits that could withstand the 20% Sodium Hyroxide, high-pressure hot water, or low-pressure steam were selected to keep the robots fully operational.
RESULTS
The M55 rocket stockpile was successfully destroyed without any major incidents. With so many complex systems, processes, and disposal procedures, the Robosuits played a key role in ensuring that all of the careful planning and timing would not be disrupted.
“The Robosuits added an extra layer of protection to help ensure that we could meet our deadline,” said James DeSmet, CRG Automation’s CEO, “They protected our customer’s investment in the technology so that we could complete the mission and exceed expectations.” In fact, the Robosuits enabled the disposal process to commence without any robotic malfunctions resulting from chemical exposure or precautionary washdowns.
It was a disposal done right, ahead of schedule, safe, and sound.
The content & opinions in this article are the author’s and do not necessarily represent the views of RoboticsTomorrow
Comments (0)
This post does not have any comments. Be the first to leave a comment below.
Featured Product
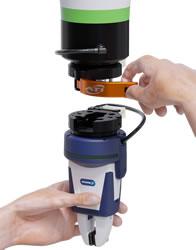