Cornerstone Specialty Wood Products’ New Manufacturing Facility Nears Completion
Located in a suburb of Louisville, Kentucky, the plant will enable Cornerstone to increase its manufacturing output to more than double its current capacity.
Having experienced significant growth in demand for its ResinDek® engineered flooring panel and shelving products over the past two years, Cornerstone Specialty Wood Products, LLC® (www.resindek.com) and its parent company, Universal Woods (www.universalwoods.com), have invested in the construction of a new, $15 million greenfield manufacturing facility. Located in a suburb of Louisville, Kentucky, the plant will enable Cornerstone to increase its manufacturing output to more than double its current capacity.
"Our business has grown dramatically over the past two years, for which we are extremely grateful," says Greg Doppler, inventor of the ResinDek flooring panel and President of Cornerstone. "As a result of this tremendous growth, we are approaching the upper limits of our current production capacity. This investment will ensure we are in position to deliver ResinDek products quickly to our valued customers well into the future."
"The new facility's footprint is more than double the current footprint, enabling us to carry more inventory and manufacture products faster. That combined with a design that incorporates significantly more dock doors for shipping and receiving, will allow us to reduce lead times," adds Scott McGill, Director of Sales at Cornerstone.
"The new operation will also be equipped with the latest state-of-the-art electron beam coating and curing equipment that we have always used to produce our ResinDek's protective coatings and finishes, only at much higher throughput rates and volumes than before," Doppler explains. "It will also allow us to attain even greater quality than the high standards our current coating and curing line currently achieves."
"The new equipment will not only increase quality and manufacturing output, but also provide a wider array of opportunities within our new product development program. This will allow us to continue to offer a fantastic value proposition to our customers," states McGill.
The new facility, located at 264 Eiler Avenue in Louisville, near the UPS Worldport and Louisville International Airport, will be staffed by the same production team working at the existing operation. In advance of its construction, Cornerstone added additional employees in 2021 in anticipation of the expanded production capacity. "Starting them ahead of the new plant's construction allows them to become familiar with the ResinDek production process before the new facility goes live," adds Doppler.
Equipment is slated to be installed and commissioned throughout January 2022, with partial production beginning shortly thereafter. The new coating and curing machinery are scheduled for installation in the second quarter of 2022.
"We expect to be fully operational in the third quarter of 2022 and look forward to celebrating Cornerstone's new capabilities with a Grand Opening ceremony at that time," Doppler concludes.
For more information, visit Cornerstone Specialty Wood Products at www.resindek.com.
# # #
ABOUT CORNERSTONE SPECIALTY WOOD PRODUCTS, LLC
For more than 20 years, Cornerstone Specialty Wood Products, LLC (www.resindek.com) has been at the forefront of research and development in the field of engineered wood floor panels for the material handling industry. In 1994, Greg Doppler, company founder and president, invented the ResinDek panel, which has become the premier mezzanine flooring panel product sold worldwide today. ResinDek industrial engineered flooring panels have the proven structural integrity to support live and dead pallet jack limits from 2,000 - 8,000 lbs. and the rigorous demands of Automated Guided Vehicles and Autonomous Mobile Robots.
Featured Product
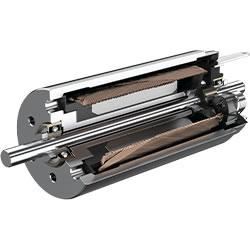