How Construction Companies Are Automating Workflows
Visit any news site, and you’ll find recent headlines and op-eds describing big tech’s recent stumbles—overzealous hiring sprees in hyper-growth phases have been disrupted by worrying economic signals, which perpetuate a vicious cycle of mass job cuts.
The story unraveling in the construction industry, meanwhile, is quite a different one—job openings far outpace workers in the talent pool. Data released by Associated Builders and Contractors (ABC) in February revealed that the construction industry’s workforce shortages have topped half a million.
NPR reported a similar story, citing the recent Bureau of Labor Statistics’ (BLS) report that showed the number of construction job openings rose by 129,000 in February, while hiring decreased by 18,000.
CNBC reports that tech workers worry over being replaced by generative AI, but as these workers find their jobs threatened by recent job cuts, the construction industry stands to gain from adopting technology and, particularly, automation to address workforce challenges. In fact, Construction Drive cites a new report from Dodge Construction Network that revealed positive results among general contractors automating subcontractor management processes. 91% of GCs who used sub management technology, the report found, experienced improvements in productivity. In addition, 81% responded they experienced lower costs, and 79% responded higher profits.
In this article, we look at how construction companies are currently automating workflows and can continue to leverage technology to address workforce challenges.
Robotics
Reuters reported in February that orders placed to North American robotics companies in 2022 reached 44,100 units—an 11% increase over the previous year and a new record.
And that’s for good reason – robots drive positive outcomes in the construction sector:
- They help improve speed and automate procedural tasks (by 25-90%) as well as reducing hazardous tasks (by 72%), empowering already strapped project execution teams onsite to deliver executables faster, but also more safely and more predicably.
- They empower project managers to better forecast, predict, and scope project budgets and timelines while also improving communication, collaboration, and morale between cross-functional teams.
- They can reskill construction laborers into higher-skilled roles. At the same time, they can empower skilled trades to cut the monotony from their day to focus on the parts of their job that call for the highest degree of human intelligence and reasoning.
Types of robotics and use cases:
- Procedural robots – bricklaying robots, like Construction Robotics’ SAM, have helped companies complete jobs faster by working alongside skilled bricklayers in remote areas like Virginia where access to skilled workers is limited.
- Drones and reality capture – Drones can be used both in preconstruction and on active sites—to map out sites, to perform overhead progress reports, even to keep track of assets. Such is the case for an Australian customer of major drone-making company DroneDeploy, who has used the company’s software across 20 projects to communicate daily activities as well as change design plans and report site progress in real-time. Meanwhile, Boston Dynamics’ “Spot,” a more traditional, if canine-reminiscent, robot, has been used to drive reality capture workflows, such as monitoring an HDVC converter station in central Massachusetts for public safety.
- Exoskeletons – both partial and full-body exoskeletons (think: Tony Stark becoming Iron Man) can help empower their wearer to more safely perform dangerous tasks, faster. Such is the case with Comau’s MATE that offers postural and upper limb support that helps wearers move more comfortably, reduces muscle fatigue, and enhances overhead mobility.
Experts have agreed that automation is critical to address many of the challenges the construction industry faces, while they also agree that focusing on the human side of automation is equally important. “It’s not that they’re replacing people but that they’re refocusing people,” said Alan Gasvoda, an End User Productivity Leader for Continuous Improvement at Milwaukee Tool, in a recent expert roundup on automation. “[T]he robotics are typically done to those tasks that people don’t typically like to do anyway, and it provides the industry the chance to upskill their current workforce,” he explains.
Industrialization
Industrialization within the construction industry refers to the productization of construction projects, and it represents a mindset shift from one-off projects to more wholistic, systemic processes. General tenets and key advantages to industrializing construction processes include reducing waste, creating a value chain for the customer, and improving the overall quality and consistency of the build.
Common levers pulled in an industrialized construction workflow include:
- Adopting lean management principles
- Streamlining preassembly through offsite construction (e.g., partnering with a third-party prefab or modular construction vendor, or building your own infrastructure) to better control quality assurance. That is to say, offsite construction allows companies to skirt unpredictable weather conditions, and leverage temperature-controlled factory settings and assembly lines with standardized processes and even robotics (as in above workflow!) that drive better consistency.
- Adopting additive manufacturing technologies (such as 3D printing) to increase design freedom and timeliness as well as reduce waste.
- BIM and digital twin models to mirror systems and processes across project lifecycles, leverage real-time data, and use simulation and machine learning and reasoning to help empower smarter decision making.
Examples of companies currently using industrialization techniques include Modular Building Institute award-winning company, NRB Modular Solutions, which has done everything from providing affordable housing in Oshawa, Ontario, to delivering office space in a manufacturing facility.
A similar project included one from modular builder 720 Solutions, which delivered housing for mental health clients, a 36-module, 28-unit structure that, once planned, greenlit, and completed offsite, took merely a day to assemble onsite.
Safer, Smarter Power Tools
There has been a barrage of headlines related to artificial intelligence in recent months that highly emphasize applications like generative design. A far less discussed topic, though equally compelling, is how machine learning algorithms applied to power tools can make those tools, in the hands of onsite installers, safer against dangerous events like kickback, or how utilization events performed on these tools can be pulled to assist with anything from troubleshooting maintenance to providing quality assurance to customers that work has been performed to specification.
Examples of smart power tools in use:
- Major electrical grid providers rely on smart power tools, like digital torque wrenches, to automate the installation of heavy-duty mechanical lug nuts for high-voltage electrical wires. Proof-of-work reporting also demonstrates to customers and stakeholders that these critical fasteners were installed to specification and that the public’s safety can be ensured.
- Heavy duty mechanics, meanwhile, rely on IoT solutions – smart impact guns empower these trades to deliver precision fastening in the fleet vehicles they service. What’s more, integrated cloud-based inventory management features help them warranty and service the tools they use in the shop, as well as to keep track of these tools’ locations around the shop and in the field.
Software Integrations
Software integration and interoperability remain the digital answer to the real, quantifiable problems experienced in the physical world of construction—both in terms of addressing workforce problems as well as the industry’s digitization dilemma.
Experts have pointed to recent acquisitions by major construction SaaS companies as evidence to where the industry is moving.
The advantages to construction companies integrating their software as well as the apps they use include removing information silos, increasing cross-functional collaboration, removing manual entry that can lead to human error, and overall, improving how companies can operate more seamlessly by leveraging real-time data.
Examples of software integrations in the wild include:
- How a data center utilizing Procore seamlessly connected their flow of information so that communication is facilitated “from anywhere, at anytime.”
- How an engineering services firm utilizing Autodesk Construction Cloud™ “foster collaboration” by building data connectivity that allows their in-office engineering and in-field construction management teams to synchronize digitally in real time.
- Integrations like the one between consumer BLE tracking tag company Chipolo® and heavy-duty cordless power tool manufacturer Milwaukee® via their One-Key connectivity platform. This integration allows both companies to expand their BLE networks and it facilitates the reciprocal improvement of both consumer and professional trade end users. As an example, when a consumer whose cat tracker passes within range of professional tradesperson’s Bluetooth®-enabled Drill/Driver or asset affixed with a heavy-duty Bluetooth tracker, this interaction contributes to the scatternet that sends location updates to each app anonymously.
Advice to the Construction Sector: Absorb Big Tech’s Displaced Technologists
I started this article comparing and contrasting the technology sector’s job cuts to the construction sector’s workforce challenges, which on the surface serve as an interesting narrative foil.
Both industries confront seemingly insurmountable obstacles. Both are existential in nature. The displaced tech engineers worry where they may go as thousands of their peers face similar fates. The construction companies wonder how they’ll execute on a growing backlog of projects as the talent pool they and their competitors both rely on continuingly narrows.
But with these industries facing problems on the opposite side of the workforce spectrum, one wonders if, together, both industries can help solve the other’s problems in a mutually beneficial manner.
Microsoft’s CEO Satya Nadella, in a 2022 interview with CNBC International, had some thoughts that mirror this sentiment:
“There are more software engineering jobs outside of the tech industry than there are in the tech industry,” said Nadella. “So, to some degree, I’d say the labor markets are much more resilient. There’s not an auto company that doesn’t need software engineers. There’s not an energy company that doesn’t need software engineers. There’s not a retailor or a bank that doesn’t need software engineers.” He arrived at a similar conclusion to the above-one I made: “To the degree to which there is oversupply in one [industry], there will be more even distribution.”
As roles like construction technologist emerge, as experts in the construction industry agree on the importance of data and integrations, and as VC funding in contech startups surge, there begin to emerge pathways for this even distribution Nadella describes to accommodate big tech’s displayed displaced software engineers entering the construction tech industry:
- Displaced software engineers entering contech startups
- Displaced software engineers and technologists hired directly by construction firms to help build these companies’ tech stacks to better execute on projects
Furthermore, as a parting thought, at Milwaukee Tool, there’s a lot more than immediately meets the eye from an engineering standpoint. While software engineers may see a traditional, nearly hundred-year-old power tool company, in fact there’s so much more inside these walls: The company’s double-digit, decade-long growth includes more than 1,500 patents since 2007, a workforce that has grown 7x, and 7 new technology centers.
Innovation is part of our DNA. One such project that brought innovation to a tired product category can demonstrate, having earned accolades from both industry and tech-focused recognizing bodies.
While the clouds may seem stormy, just beyond them is a sunny outlook: partnership.
About the Author
Lucas Marshall is a master’s degree-trained professional writer with nearly a decade’s worth of experience. At Milwaukee Tool, he’s served as Content Marketing and SEO Manager for the past four+ years, where he and his team raise awareness about the company’s digital and IoT products, particularly their connectivity platform ONE-KEY™. In addition to regularly contributing thought leadership to industry publications, he manages, contributes to, and edits the company’s connectivity blog.
Comments (0)
This post does not have any comments. Be the first to leave a comment below.
Featured Product
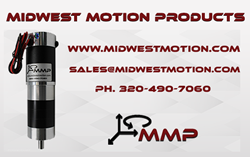