Robotics Changed Industry 4.0; Now, How Will Industry 4.0 Change Robotics?
Novel robotics technology was one of the most significant drivers behind the start of the fourth industrial revolution, or Industry 4.0. Now, new computer technology, like industrial IoT devices and AI algorithms, is likely having a bigger impact on industry. It seems likely that these technologies will also have a major effect on how commercial robots are used in heavy industry.
This is how Industry 4.0 technology is revolutionizing the robotics industry — and what changes robotics professionals should expect over the next few years.
Real-Time Operational Monitoring
With IIoT sensors, it’s possible for machine owners to track the operational performance of equipment in real-time over the internet. Modern industrial IoT sensors can track a wide range of parameters, including temperature, sound, vibration, pressure, and lubrication. This information can help machine operators to optimize machine performance or more effectively respond to potential failure.
If a machine’s parameters exit a pre-established safe operating range, the IoT monitoring system can also automatically alert site technicians, allowing them to move quickly to prevent damage or machine failure.
The IoT sensors that power smart operational monitoring technology are specially constructed for industrial environments and are typically designed to integrate with existing industrial systems, like computerized maintenance management systems.
Predictive Maintenance
With enough data from operational monitoring, it’s also possible to use AI to predict when machines will fail.
Predictive maintenance is a new maintenance strategy that builds on the more conventional preventive approach. With this technique, machine operators train an AI algorithm on historical performance data from a machine, establishing a performance baseline and safe operating ranges.
If the algorithm detects readings it interprets as unusual, the predictive maintenance system can automatically alert technicians, possibly providing a suggestion of what may be going wrong. More advanced systems may be able to take action on their own, shutting down a machine to prevent damage or prepare it for emergency maintenance. The approach can significantly reduce downtime and regular maintenance costs, helping to keep factory operational expenses to a minimum.
Collaborative Robots (Cobots)
Collaborative robots (cobots) employ safety features, like force limiters and padded joints, that enable them to work in close proximity to human workers. Often, modern cobots leverage AI algorithms that allow them to automate tedious tasks that previously required human labor — like machine tending.
These cobots help free up human workers for tasks that are less dull and repetitive, helping factories streamline workflows while reducing the risk of musculoskeletal injuries.
Machine Vision
Machine vision algorithms allow robots to interpret visual data. These algorithms, best known for powering self-driving vehicles, can enable a robot to break down visual information from a camera or similar device into distinct objects or areas.
For example, a quality assurance process may use a machine vision algorithm and cameras fixed to a conveyor belt to automatically flag finished components with visible defects. A robotic system can then remove these defective items from the production line.
Autonomous Robotics
Some novel factory robotics also use machine vision to navigate without human supervision. Autonomous mobile robots (AMRs), for example, can use machine vision to break down visual information from the factory floor into categories like obstacles, workers, and navigable space. With this information, the robot can pilot itself around a site and perform tasks like the picking of goods and components, often with minimal to no human intervention.
Like cobots, these robots can help streamline a wide variety of industrial tasks that have traditionally been difficult to automate. With the right combination of robots and AI algorithms, factory owners can free up workers dedicated to picking and packing for labor that requires more creativity and less rote work.
Industry 4.0 Technology May Transform the Robotics Industry
The rise of industrial IoT and artificial intelligence is likely to have a major impact on robotics. Industry 4.0 technology enables new maintenance strategies, more autonomous robots, and new collaborative robotics technologies.
Over the next few years, industrial robots and Industry 4.0 technology could help transform factories — streamlining machine supervision and automating tasks that previously had to be handled by human workers.
Comments (0)
This post does not have any comments. Be the first to leave a comment below.
Featured Product
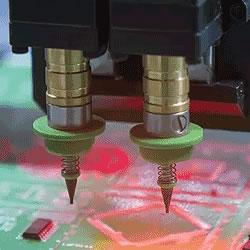