What Are the Benefits of Automated Plating?
Automation is an increasingly popular option for high-volume tasks requiring precise results. It minimizes the variability associated with manual tasks. Here are some of the specific benefits of pursuing automated plating.
1. Improved Speed
Automated systems are often chosen for better plating productivity. They allow people to maintain high work output despite having small teams. Reaching higher speeds is especially advantageous when the material requiring plating is on a large item.
Wind turbine blades are a good example. Plating makes them more corrosion-resistant and protects against pitting caused by exposure to the elements. Silver is a common material used when coating the blades.
However, getting the job done becomes trickier as rotor blades get progressively longer. That’s why a Dutch tech company tested using an autonomous mobile robot for the task. The goal was to have it coat a 100-meter blade in only 90 minutes.
The robot moves to a predetermined position before applying the coating. It then progresses to the next programmed spot to repeat the process until the blade is fully covered.
People responsible for engineering this application believe the robot’s uses could go beyond automated plating and integrate into numerous turbine blade manufacturing duties. For example, it could inspect the blade’s laminate or help with surface cleaning.
2. Enhanced Quality Control
Company leaders increasingly feel pressure for their organizations to stay competitive in an ever-challenging marketplace. There’s no guaranteed path to making that happen, but automation often plays a significant role. That was the conclusion made by the leaders of a Michigan company specializing in electroless nickel plating for customers in the automotive, oil and gas industries.
The company has seven operating baths, and decision-makers at the facility decided to automate all of them. That was due in part to labor expenses and operator differences associated with titration testing. Representatives at the organization recognized an opportunity to increase production quantities, improve chemical usage and benefit from other perks.
Better quality control was also a primary benefit expected from this plan. Automating plating systems remove virtually all the variability present in tasks done by hand. They also allow people to supervise the processes and pinpoint the precise causes of production issues earlier and address them promptly. In this case, the organization selected a system that sent alerts to people’s smartphones if abnormalities were detected.
The automated equipment chosen by the company was three-and-a-half times better at maintaining a bath’s nickel concentration than manual processes, data showed. Also, it didn’t take long to see positive results.
Company leaders initially planned to compare the automated controller’s results with the manual methods for a month. However, the automation showed superior outcomes after only a week.
3. Reduced Costs
Companies specializing in plating use various processes to achieve uniformity that can cut costs while ramping up production when needed. It’s also necessary to apply plating in ways that fit customers’ precise needs.
For example, gold plating is commonly added to electronics components to protect them from heat. That’s because gold’s melting point is 1,943 F, which provides good protection from heat. Applying a thicker plating layer is a practical way to increase heat resistance within the electronics concerned.
Since people can set up tools to apply precisely the amount of plating needed, it cuts the costs associated with mistakes. Similarly, bringing robots into a plating process is an effective way to reduce waste. Minimizing resource usage is a proven way to support a company’s bottom line by curbing unnecessary spending.
Toyota uses a dip-free plating machine that allows precise limiting of the application area. The waste solution associated with this method is reportedly about one-30th of the previous one.
4. Minimized Environmental Impact
Some companies also use automation to source materials used for plating. Apple’s iPhone 13 was the first of the brand’s products to use certified 100% recycled gold on the main logic board and the front and rear camera wires.
The company has a disassembly robot called Daisy that helps recyclers get to the reusable materials inside old electronics. It currently operates one such machine in the Netherlands and another in the United States.
A source at Apple said, “Just 1 metric ton of iPhone main logic boards, flexes and camera modules disassembled by Daisy contains the same amount of gold and copper as an estimated 150 metric tons of mined earth. These materials make it back to the general market so that we and others can use recycled materials for the next generation of products."
This method of applying automation to source plating materials is not yet common. However, as people become increasingly concerned about protecting the environment for this and future generations, other companies will likely follow Apple’s lead.
5. Elevated Operator Safety and Comfort
Automating some or all parts of the plating process can reduce or minimize potential operator illness or discomfort. For example, electroplating can emit dangerous chemicals, while metal plating produces dust that’s harmful if inhaled. The side effects can range from short-term issues like eye and throat irritation to long-term illnesses, including cancer. The health risks vary depending on how much of a chemical or harmful particle is absorbed into the body.
Automated plating could keep people safer by letting them stay further away from electroplating operations while supervising and intervening when needed. Using automation instead of having operators manually pour substances into tanks removes the threat of an accident caused by a person spilling the product onto themselves or a co-worker.
Automated plating systems also relieve people from spending too much time in positions that eventually strain the body. Even if a process still requires some manual steps, machines could offer a more ergonomic option for workers.
Automation can also reduce the overall number of people required to do a task without causing fatigue in the workforce. For example, one manufacturer needed more than a dozen workers overseeing four to five machines before investing in automation. Now, one or two people do the same job.
Plating Automation Brings Impressive Payoffs
These examples show it makes good business sense to bring automation into a plating operation. However, that approach is not the best one in every case. Getting optimal results requires careful consideration of project specifications, client needs and other relevant factors. A clear understanding of requirements from the outset prevents challenges later.
Comments (1)
Featured Product
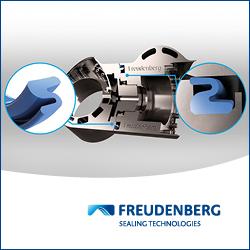