To validate and demonstrate our Through-the-Earth capability, we developed a full-duplex MI Modem (MIM-1000) and installed it on a Pioneer 3-AT R&D robot. Initial field trials were carried out at an abandoned coal mine in Nova Scotia, Canada, where we successfully demonstrated the robot – we call her “Maggie” – being driven and maneuvered remotely by an operator located on the mines surface with Maggie located in an underground mine shaft separated by over 100 feet of geological overburden.
Steve Parsons, Business Development Manager | Ultra Electronics
Tell us a bit about Ultra Electronics:
Ultra Electronics is a defence and aerospace company specializing in the design, manufacture and support of electronic and electromechanical systems, sub-systems, products and services for aircraft, ships, submarines, armoured vehicles, surveillance and communication systems, airport and transport systems. Headquartered in London, UK, Ultra Electronics is a publicly traded company listed on the LSE with multiple business units operating in the UK, US, Canada, Europe, Australia, China and the Middle East.
Ultra Electronics, Maritime Systems is a leading supplier of innovative and cost-effective solutions to defence, aerospace and industrial markets internationally. Founded in 1947, Maritime Systems has earned its reputation as a world leader in the development and manufacture of solutions for Undersea Surveillance, Infrastructure Optimization and Protection, and Magneto Inductive Technology. Maritime Systems is located in Dartmouth, Nova Scotia and is an ISO 9001 certified company.
How does this technology work:
We refer to the communication technology as Magneto-Inductive (MI). The MI signal is actually a low-frequency ac magnetic dipole field that is created by applying current to an antenna coil. We modulate the current using a variety of different techniques, depending on the application, so it is digital data we are transmitting and receiving, much like software defined radio, but it’s not RF. The advantage of the MI signal lies in its ability to penetrate through all natural media (air, water, earth, rock, ice) as well as most man-made structures. You don’t get reflections and refractions off surfaces and there is no multipath. Radio can’t penetrate into a tunnel or mountainside, acoustics can’t get out of the water. The MI signal can pass through physical barriers, intervening media and across media boundaries, enabling wireless connectivity to and from some very remote and isolated places.
You have recently demonstrated wireless Through-the-Earth (TTE) command and control of a remotely operated vehicle. What role with this play for military and civilian applications?
We have been working on the remote command and control of robotic platforms for a number of years now. Our early work involved networking a group Underwater Bottom Vehicles designed to carry out mine countermeasure missions in the littorals. Recently, we’ve extended this work to the control of remotely operated ground vehicles. Our end goal here is to provide vehicle operators with the capability to remotely control their robotic and unmanned platforms in places where RF won’t work and where the use of a fiber-optic tether is susceptible to entanglement and damage, like in underground tunnels, culverts, buildings and basements.
To validate and demonstrate our Through-the-Earth capability, we developed a full-duplex MI Modem (MIM-1000) and installed it on a Pioneer 3-AT R&D robot. Initial field trials were carried out at an abandoned coal mine in Nova Scotia, Canada, where we successfully demonstrated the robot – we call her “Maggie” – being driven and maneuvered remotely by an operator located on the mine’s surface with Maggie located in an underground mine shaft separated by over 100 feet of geological overburden. Video captured by Maggie’s onboard camera was compressed and transmitted back to the operator in real time at 2400 bps by the MIM-1000, allowing the operator to control and manipulate Maggie and her functions and to view objects of interest remotely. We’ve since trialed the system in a number of tactical operating environments in underground and in confined spaces.
The importance of this development is what it can mean to the safety of soldiers, emergency responders and law enforcement personnel, especially those who need to send a robot deep inside a building, culvert or other confined space to investigate a potential IED/EOD threat. Additionally, if you lose your RF link or break the fiber optic cable, you lose control of a very expensive piece of equipment that has to be physically recovered by personnel, who are then exposed to whatever threat may be in there. We want to keep those folks out of that danger area.
With the existing UAVs and other unmanned vehicles currently available is it difficult to change the technology on them like upgrading the video with a newer camera? Are most UAVs built to allow for modular upgrades?
To answer the first part of the question, not necessarily. Today’s unmanned vehicles are continually evolving. Users and developers alike are always looking at ways of improving what their unmanned vehicles can deliver, whether it’s a UAV or a UGV. This goes to better cameras, new sensors, lighter components, more efficient power supplies. The list goes on. Modular upgrades are preferred simply because you don’t want to have to modify or reengineer your platform every time there is a new payload to integrate. That involves time and money and of course risk. Industry specific interface standards are well defined for the same reason. So if you can provide a modular solution that can be “plugged-in” with as little NRE as possible that is obviously the best way to go.
Looking into your crystal ball, what do you see with the future of this technology?
Ultra has been supplying MI solutions to the defence community since the early 90’s and the technology has found some very interesting and unique homes. We believe this is one of them. We are constantly looking at ways of improving and optimizing the MI channel’s capacity through the implementation of newer, advanced modulation schemes, error correction techniques, and so on. For this application, our current focus is looking at ways to extend the range and improve the quality of the video backlink, while maintaining logistical supportability. We are working with robot developers, vendors and the end-user community to refine and deliver this capability to CIED and EOD field operators at home and abroad.
About Ultra Electronics
Ultra Electronics is an internationally successful defence, security, transport and energy company with a long, consistent track record of development and growth.
Ultra businesses constantly innovate to create solutions to customer requirements that are different from and better than those of the Group’s competitors. By applying these differentiated solutions to a wide range of international platforms and programmes, Ultra has built an exceptionally broad range of niche market positions.
Ultra offers support to its customers through the design, delivery and support phases of a programme. Ultra businesses have a high degree of operational autonomy so that they may provide exceptionally agile and responsive support to customers and partners.
Operationally, the Group is organised into three divisions:
Aircraft & Vehicle Systems, Information & Power Systems and Tactical & Sonar Systems.
The content & opinions in this article are the author’s and do not necessarily represent the views of RoboticsTomorrow
Comments (0)
This post does not have any comments. Be the first to leave a comment below.
Featured Product
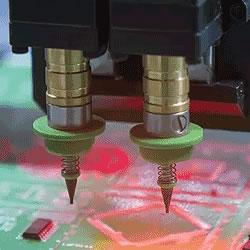