Our approach is to drive modularity and mobility into the core system architecture so that the automation is less static and monolithic, and can adapt to the changing nature of scientific research.
Using Modular and Mobile Robotic Solutions in The Biotech Industry
Peter Harris | HighRes Biosolutions
Give us some background on HighRes Biosolutions (overview of co., specific use cases/offerings, when it was founded, etc.)
HighRes Biosolutions was founded in 2004 by Lou Guarracina, who had spent much of his life working in the laboratory automation space, and had a vision for an improved architecture around which to configure complex systems. We pioneered the use of modularity to address robotic system integrations in life science research.
Today, our systems are used by both the largest therapeutic research organizations in the world and many early-stage, innovative companies looking for novel methods to address disease states.
Tell us a little bit more about your laboratory automation systems and what they can do.
HighRes’ expertise lies at the intersection of robotics and scientific research. As such, our systems are comprised of a combination of robotic elements and associated software, and a wide range of application-driven research instruments that can mix, heat, seal, shake, and read the results of experiments. At its simplest, our systems are designed to replicate the work a scientist used to do through a sequence of steps at a benchtop through using a robot integrated with a range of sophisticated instruments to produce results. Applications span from high-throughput screening, to compound management, to next generation sequencing, to synthetic biology.
Any time precise, repetitive and complex research tasks need to be performed, there is an opportunity to design a robotic system using our technology.
You work with many impressive clients including AstraZeneca, Ginkgo, Unum, Recursion, among others. What kinds of results do your clients typically see, utilizing your technology?
In almost all cases, our customers find that the use of our systems increases the number and accuracy of experiments/processes they are able to run, while also letting their scientists focus on the actual science. For example, a large HighRes screening system may be able to test upwards of 300,000 compounds per day, while at the same time having high enough precision to reduce the amount of material required per test. In this way, our systems are helping to reduce the overall cost of discovery for new therapies. In other cases, the science would not even be possible without the robotic system. For example, companies working to use artificial intelligence in closed loop systems to generate real time feedback from experimental results rely on the system being automated to do so.
What unique elements of HighRes Biosolutions' robotics solutions and systems allow you to meet the needs of scientists in the pharmaceutical and biotechnology industries? (Vs. competitors)
Our approach is to drive modularity and mobility into the core system architecture so that the automation is less static and monolithic, and can adapt to the changing nature of scientific research. We use docking elements and collaborative robots to create systems that work on an integrated holistic basis, but can also have elements decoupled to perform different tasks, thus increasing asset utilization.
At the same time, modularity allows multiple workflows to happen on the same system. For example, by making the reader element of a system dockable, researchers can switch out readers in a matter of minutes if the type of screen they are interested in performing changes. This makes our systems highly flexible, and helps to future-proof the robotic investment if the application distribution evolves.
Give us an idea on the setup procedure and time needed to implement an HRB laboratory automation system.
Because we design and configure each system for each customer’s needs, there is a decent amount of upfront work we do with customers to really understand their science and associated goals. At some level, a guy and a dog in a garage can build a basic robotic system. However, a system that is married to scientific research workflows in a way that works seamlessly for scientists (not computer scientists or roboticists) requires work and expertise. We typically have a very large amount of applications development time invested in every project before the customer is even in a position to know exactly what system configuration is best for them. Thereafter, the build and deployment timelines depend largely on the size and complexity of the system itself.
Once up and running what kind of maintenance and training are required to operate the systems?
Software is arguably more important in robotic systems than hardware, and our approach is to make the entire system interface seamless and easy for the scientist. Researchers want to do research, not robot design or maintenance; our software has incredible complexity and sophistication in how it operates, but presents the user with simple, graphically-driven interfaces that make it easy for them to interact with the automation themselves.
We believe it should be very rare that a user needs to call us to make changes to their system or protocols. With that said, we do perform periodic maintenance and tuning on our systems in the field to ensure that they are running in an optimized manner and delivering what the customer needs. The training requirements can also vary depending both on the nature of the system and the interest from the user.
The topic of robots and automation eliminating jobs has been everywhere this year. How do you respond to these fears that many jobs will be taken over by robots and automation.
The hype around robots taking jobs has to be near its long-term peak level, and is almost certainly a perceptual bubble. There is no doubt that robots (and frankly software in particular) will replace a lot of routine tasks currently being performed by people. However, there has never been a time in history when technology eliminated routine work and humanity hit the pause button. Rather, in the never-ending quest to improve our quality of life, we find new things to do and new ways to apply human effort.
When the Luddites protested modernization of weaving because it threatened to eliminate jobs, they never envisioned that eventually cost reductions in textile manufacturing would allow people to have 10 suits instead of one. As technology progresses, standards of living increase and work gets created. Similarly, in our case we strongly believe in the benefits of reducing overall discovery costs for novel therapies. You would not believe how much routine work is being done by highly-educated scientists. Imagine if they all just did science and let the robots do the labor. Therapeutic discovery output would increase, and not at the expense of jobs. In other industries, it may be messy along the way, but in research there is a lot of room for humans and robots to work together for the greater good.
Robotics and automation is evolving rapidly. Where do you see laboratory automation systems 5 years from now and how will HRB technology adapt to meet these changes?
You are absolutely right about the rate of change. It is staggering and varied in the technologies that are adapting. Sensing, collaboration, machine learning, vision, and cloud computing are all big factors to be considered as we look into the crystal ball for laboratory automation. We believe the lab of the future will have humans and robots working alongside each other, safely and productively. The reach of automation will also increase – many tasks and workflows not currently addressed by large, monolithic automation installations will become possible as collaborative robots enable smaller, mobile/modular architectures and centralized cloud computing and management let robots become distributed assets capable of performing a wide range of tasks.
As HighRes’ strategy is to lead in life science discovery robotics, we have a variety of R&D programs underway with these trends in mind. Will they be fully deployed within five years? Hard to say. Within ten years? Almost certainly.
The content & opinions in this article are the author’s and do not necessarily represent the views of RoboticsTomorrow
Comments (0)
This post does not have any comments. Be the first to leave a comment below.
Featured Product
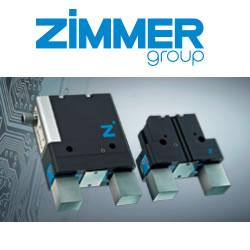