Press brake robots eliminate the challenges of manual sheet metal bending, such as inconsistencies, high labor costs, and workplace hazards. By leveraging robotic arms, sensors, and advanced software, these systems significantly improve accuracy and repeatability.
Press Brake Robots: Transforming Sheet Metal Bending with Precision and Efficiency
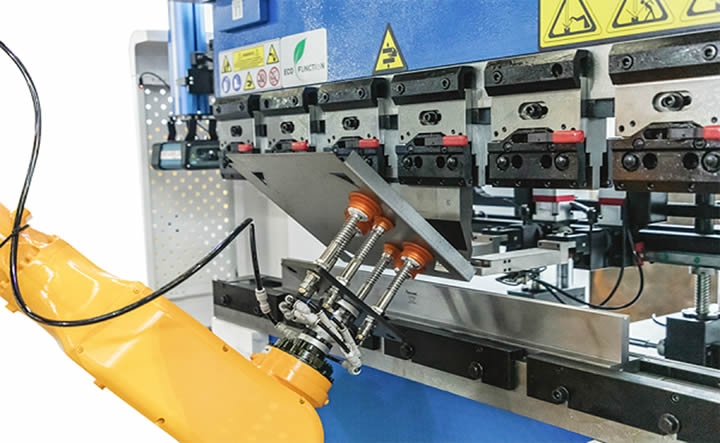
Article from | ACCURL
Automation has revolutionized the manufacturing industry, and one of the most significant advancements in sheet metal fabrication is the use of press brake robots. These robotic systems enhance efficiency, reduce human error, and ensure consistency in bending operations. As the demand for precision and speed increases, businesses are integrating automation to streamline production and meet stringent quality standards.
Press brake robots eliminate the challenges of manual sheet metal bending, such as inconsistencies, high labor costs, and workplace hazards. By leveraging robotic arms, sensors, and advanced software, these systems significantly improve accuracy and repeatability. Leading the way in this transformation, ACCURL integrates cutting-edge robotic automation into its press brake solutions, enabling manufacturers to achieve higher efficiency and precision. This article explores the mechanics, benefits, and applications of press brake robots, as well as their future in the manufacturing sector
What is a Press Brake Robot?
A press brake robot is an automated system that assists or fully executes the sheet metal bending process using a robotic arm, vision systems, and software-driven controls. Unlike traditional press brake operations, which require skilled operators to manually position and manipulate metal sheets, press brake robots ensure precision by following pre-programmed instructions.
How It Differs from Traditional Press Brake Operations
- Automation: Robots handle repetitive tasks with minimal human intervention.
- Precision: Advanced sensors and AI-based control systems enhance accuracy.
- Efficiency: Faster cycle times compared to manual operations.
- Safety: Reduces risks associated with handling large and heavy metal sheets.
The Role of Robotics in Modern Metal Fabrication
Robotics play a crucial role in streamlining metal bending processes by increasing throughput and maintaining consistency across large production runs. With advancements in artificial intelligence and machine learning, these systems can adapt to variations in material properties and environmental conditions, ensuring optimal bending performance.
How Do Press Brake Robots Work?
Press brake robots operate through a series of automated steps that ensure precise and consistent metal bending.
Key Steps in the Operation Process:
- Material Loading: The robotic arm picks up and positions the metal sheet.
- Alignment and Positioning: Vision systems and sensors ensure accurate placement.
- Bending Process: The press brake machine executes the programmed bending sequence.
- Quality Inspection: Sensors check the accuracy of bends and detect any deviations.
- Unloading: The robotic system moves the finished part to the designated area.
Robotic arms work in sync with press brake machines, following programmed instructions that dictate force, speed, and angle of bending. Advanced control systems and AI-based algorithms further enhance accuracy by adjusting for material variations in real time.
What are the Key Components of a Press Brake Robot?
A press brake robotic system consists of several essential components that work together to perform precise sheet metal bending.
Main Components of a Press Brake Robotic System:
- Robotic Arm – Handles material manipulation and positioning.
- Press Brake Machine – Applies force to bend the sheet metal.
- Vision Systems and Sensors – Ensure accurate placement and quality control.
- Control System and Software – Manages programming and automation.
- Grippers and End Effectors – Securely hold the material during bending.
Robotic Arm
The robotic arm is responsible for handling and positioning the metal sheet. It is equipped with end effectors and grippers to ensure a firm hold on the workpiece. The movement of the robotic arm is programmed to follow precise trajectories, ensuring consistency in bending operations.
Press Brake Machine
The press brake machine exerts force on the metal sheet to achieve the desired bend angles. Modern press brakes integrate CNC (computer numerical control) systems for precise operation and seamless coordination with robotic arms.
Vision Systems and Sensors
Vision systems and sensors enhance accuracy by verifying sheet placement and measuring bend angles. They detect discrepancies and adjust the robotic arm’s movements in real time, preventing errors and minimizing material waste.
Control System and Software
This component acts as the brain of the robotic system, managing the communication between the robotic arm and press brake machine. Advanced software allows for offline programming, real-time monitoring, and data analysis to optimize performance.
Grippers and End Effectors
Grippers are specialized tools attached to the robotic arm that hold, manipulate, and rotate metal sheets during the bending process. Different gripper designs accommodate various sheet sizes, weights, and materials.
What are the Benefits of Using Press Brake Robots?
Integrating press brake robots into sheet metal fabrication brings numerous advantages to manufacturers.
Key Advantages:
- Increased Precision and Consistency – Ensures uniform bend angles with minimal deviation.
- Higher Productivity and Efficiency – Reduces cycle times and increases output.
- Reduced Labor Costs and Workforce Challenges – Minimizes reliance on manual labor.
- Improved Safety in Metal Bending Operations – Reduces workplace injuries.
- Lower Scrap Rates and Material Waste – Enhances resource efficiency.
- Ability to Handle Complex and Repetitive Tasks – Ensures reliability in large-scale production.
What Industries Use Press Brake Robots?
Press brake robots are widely adopted across various industries to streamline metal bending operations and improve efficiency.
Industries and Applications:
- Automotive Industry – Used for manufacturing body panels, chassis components, and structural reinforcements.
- Aerospace and Defense – Essential for precision bending of aircraft parts and military equipment.
- Construction and Structural Fabrication – Applied in producing metal framework and heavy-duty structures.
- Electronics and Enclosures Manufacturing – Ensures accurate bending for metal casings and enclosures.
- Agricultural Equipment and Machinery – Used for manufacturing durable components in farming machinery.
- Medical Equipment and Devices – Provides precision bending for medical instruments and equipment housings.
What Factors Should You Consider When Choosing a Press Brake Robot?
Selecting the right press brake robot depends on multiple factors that impact performance and cost-effectiveness.
Key Decision-Making Factors:
- Machine Compatibility – Ensuring the robot integrates seamlessly with existing press brake machines.
- Load Capacity and Sheet Size Handling – Matching the robot’s capabilities with production requirements.
- Programming and Software Capabilities – Evaluating ease of use and customization options.
- Flexibility and Customization Options – Determining adaptability for various bending applications.
- Cost and Return on Investment (ROI) – Weighing initial investment against long-term efficiency gains.
How Much Does a Press Brake Robot Cost?
The cost of a press brake robot depends on various factors, including automation level, brand, and software integration. Generally, pricing varies across different categories, from entry-level collaborative robots to mid-range articulated models and high-end fully automated systems. The more advanced the system, the higher the investment required.
Factors Affecting Pricing:
- Brand and Manufacturer – Premium brands command higher prices.
- Automation Level – Fully automated systems cost more than semi-automated setups.
- Software and Programming Features – Advanced AI-driven programming increases costs.
- Installation and Maintenance Costs – Additional expenses for integration and upkeep.
Conclusion
Press brake robots are transforming sheet metal bending by delivering unmatched precision, efficiency, and safety. As industries continue to adopt automation, these robotic systems will play an even more critical role in modern manufacturing. By reducing labor costs, minimizing material waste, and improving productivity, press brake robots offer a strategic advantage in an increasingly competitive market.
The content & opinions in this article are the author’s and do not necessarily represent the views of RoboticsTomorrow
Comments (0)
This post does not have any comments. Be the first to leave a comment below.
Featured Product
