In the past few years, we have found that ultra-short pulse (USP) lasers are being used more and more for medical device manufacturing – from stents and catheters, to wire stripping and balloon texturing.
Ultra-Short Pulse Lasers Are Great Tools for Processing Plastics for Medical Devices
Geoff Shannon | Amada Miyachi America, Inc.
In the past few years, we have found that ultra-short pulse (USP) lasers are being used more and more for medical device manufacturing – from stents and catheters, to wire stripping and balloon texturing. The level of quality and dimensional accuracy needed fits well with the USP lasers, which do a great job of drilling, cutting, skiving, texturing and machining both plastic and metal-plastic combinations.
As an independent laser integrator with our own application labs in which we test and select the best laser for the job, we have conducted testing on USP lasers for polymer processing and want to share some of our findings and recommendations for success.
Key laser parameters for polymer processing
For polymer processing for medical devices, the most important considerations are pulse width, pulse energy and frequency, and wavelength.
Pulse width
We tested pulse widths ranging from 300 femtoseconds (fs) to 10 picoseconds (ps), using the same laser with adjustable pulse width so all other beam parameters were as equivalent as possible. The figure below shows cross sections of machined channels using different pulse durations and showing channel depth. The top row is fluorinated ethylene propylene (FEP) material and the bottom row is polytetrafluoroethylene (PTFE).
The tests show that the fs pulse duration is the best choice based on material removal rates. Also, the shorter fs pulse width always provides superior feature quality because it is a pure sublimation removal process. Since there is no melting involved, there is no top or bottom side burr, and much more precise control over feature dimensions. The longer ps pulse widths, while still providing good quality, show burring effects, indicating some material melting.
Pulse energy and frequency
We asked ourselves, “Is it better to use higher pulse energy at lower frequency or lower pulse energy at higher frequency?” To get a definitive answer, we tested three pulse energy levels at a constant average power of 20W and a pulse width of 290fs.
The figure below shows data from multiple pass scribe lines in FEP plastic for the three pulse energy/frequency combinations. The left graphic shows the depth of the scribe with number of passes and the right shows the volumetric removal rate of the scribe line with number of passes. We found that both the depth and volume removal for the multi pass scribe line is better using the low energy/high repetition rate of 40mJ/500 kHz to around 0.5mm (0.02-inch) depth.
Beyond this thickness the narrow width of the scribe likely blocks the energy from reaching deeper. The higher pulse energy of 200mJ starts to create a much wider scribe. The wider width allows the laser energy to reach deeper into the bottom of the scribe line and continue to increase scribe depth at a linear rate with more passes.
We also found that using higher pulse energy increases the process depth of focus. This increase in the part position tolerance along the focus axis is important, because the most common problem of a process falling out of specification is maintaining the position of focus relative to the part.
Wavelength
Our wavelength testing took into consideration two key points: Longer wavelengths offer higher average power and pulse energy, and shorter wavelengths offer smaller spot sizes for the same optical setup. That meant it was nearly impossible to set up an absolute wavelength-vs-wavelength test.
So we focused on which wavelength – IR, GR or UV – provides the best solution for removal rate, quality and processing window. We set out to make a flat out best processing performance test between the three wavelengths to produce “good” quality feature in Pebax®.
The figure below shows our results, which clearly indicate that removal rate versus quality favors the GR and UV wavelengths. The cross section shows the feature in a lumen is for the UV wavelength. When we used the higher pulse energy/average power of the IR wavelength, it tended to just overheat the material rather than increasing removal rate. We did not find a big difference in removal rate between GR and UV – but the UV wavelength did show a better feature surface finish and less debris.
We originally thought that fs pulses effectively normalize absorption across all materials irrespective of wavelength by effectively beating the material into submission with a literal avalanche of photons. Not so for polymers!
Using GR or UV wavelengths also maximized the processing depth of focus, which we already mentioned as a key factor to maintaining a production process.
Go with a femtosecond laser for polymer processing
Our testing showed that a femtosecond laser is clearly the correct tool for polymer processing. The removal rate tends to favor mid-range pulse energy from 40-100 mJ and higher frequencies between 200-500 kHz. Also, there is a clear advantage to using the shorter wavelength of green and UV for processing removal rate, surface finish, and maximizing the process window.
Of course every application is different and there are always budgetary constraints that factor into the laser selection. Be sure to conduct sufficient testing to make sure you come up with the best choice for the specific process and production requirements.
The content & opinions in this article are the author’s and do not necessarily represent the views of RoboticsTomorrow
Comments (0)
This post does not have any comments. Be the first to leave a comment below.
Featured Product
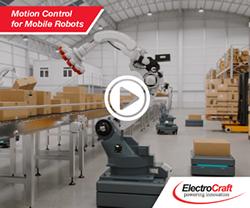