Q&A with Tom Quartararo, Mechatronics Engineer at Ultra Motion
Electromechanical Linear Actuators in Robotics & Autonomous Vehicles
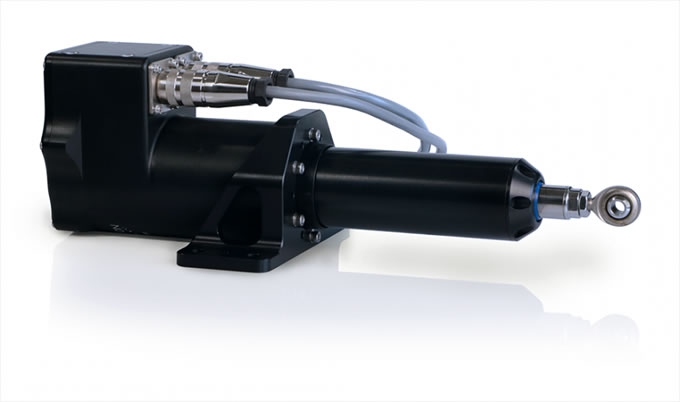
Tom Quartararo | Ultra Motion
Tell us about Ultra Motion.
Ultra Motion designs and manufactures high performance electromechanical linear actuators and has been supplying aerospace, medical, industrial, and subsea industry leaders for twenty five years. Ultra Motion specializes in applications requiring high power density actuators with output forces up to 500 lbf, and high reliability operation in extreme environments. Our actuators have flown to the International Space Station, manipulated control surfaces on ROVs submerged 20,000 feet below sea, and are a first-choice for hundreds of industrial automation customers requiring the most dependable solutions.
Figure 1: The R-Series has been designed for the highest power density and reliability actuation for aerospace and military applications. The R-series integrates a dual redundant version of our flight-proven Phase Index absolute position sensor and is hardened against extreme shock and vibration environments.
What are some emerging trends in your industry now?
We’ve seen the majority of new applications moving towards absolute position feedback and integrated drive electronics to simplify and improve the operation of their mechanisms.
Absolute position feedback is critical in applications that cannot perform a homing operation after power-up due to safety concerns or application constraints. As an example, an unmanned aerial vehicle cannot tolerate a homing sequence of a control surface actuator if there is a power-glitch in flight, and a manufacturing robot may not be able to tolerate a move to a home position to ensure operator safety. Our patented Phase Index absolute position sensor provides contactless, digital, batteryless absolute position allowing the system designer to know the exact position of our actuator’s shaft without the typical wear/life concerns of traditional absolute sensors.
The integration of brushless DC motor control electronics directly into the actuator eliminates a great deal of complexity for the system designer. As an example, our Servo Cylinder integrates brushless DC control electronics and Phase Index absolute position feedback into a single, robust package, making setup and use extremely simple and reliable.
Figure 2: The Servo Cylinder’s Phase Index absolute position feedback and brushless DC control electronics are both integrated into the rear of the actuator.
What industries are seeing a transition from hydraulic/pneumatic actuators to electromechanical?
Many industrial automation customers are transitioning from pneumatic/hydraulic actuators to electromechanical alternatives due to their lower system complexities and higher efficiencies, controllability, and repeatability. Switching to an integrated actuator like the Servo Cylinder, which is extremely simple to configure and operate, reduces the amount of resources required to implement an electromechanical replacement while also allowing the designer to bring a higher level of sophistication to their machine. The Servo Cylinder can interface with many common PLC protocols including “bang-bang” pneumatic imitation with simple digital signals, 4-20 mA input/output for drop-in analog replacements, network protocols like CANopen, and more. The Servo Cylinder is designed with oversized components so that they will provide reliable operation for years, with speeds up to 14 in/s, and position repeatability better than 0.001”.
Robotics & Autonomous vehicles are experiencing tremendous growth, can you share some examples of Ultra Motion products being used in these applications.
Ultra Motion is currently involved with many autonomous vehicle applications including unmanned aerial, ground, marine surface, and subsea vehicles. The built-in BLDC control electronics and absolute position feedback of our Servo Cylinder actuators are the perfect match for real-time vehicle control. The Servo Cylinder never needs to home at startup, making it extremely reliable and resistant to power-glitches, and the advanced BLDC control electronics allow for very high bandwidth control, up to 15 Hz for small amplitudes, which is important for stability in highly dynamic environments.
The Servo Cylinder is used for swashplate and rudder control on several UAV helicopter platforms in the 200+ kgf payload range. The Servo Cylinder is also popular in unmanned surface vehicles (USVs) for rudder control, unmanned ground vehicles for brake/throttle control, and large fixed-wing UAVs for landing gear and control surface actuation.
Figure 3: Ultra Motion’s A2 Servo Cylinders can be seen in the above photo controlling the swashplate on a UAV helicopter platform.
What are some of the special requirements you are seeing for these applications?
Dynamic performance, reliable absolute position feedback, environmental protection, and resistance to shock/vibration are the most critical special requirements for these unmanned vehicle applications. The actuators must operate perfectly while exposed to continuous vibration from engines, shocks from wave-slaps in USV applications and rough terrain with UGVs, along with rain, waves, partial submersion, mud, etc. The Servo Cylinder is designed to handle the most aggressive environments presented in these applications, and has operated flawlessly in all of its field testing.
How is Ultra Motion addressing these requirements in order to grow its market share in the Robotics & Autonomous vehicles sector?
Ultra Motion has designed our Phase Index absolute position feedback and the Servo Cylinder to meet the shock/vibration, environmental, and high dynamic performance requirements typical with our past robotics and autonomous vehicle applications. The Servo Cylinder can be controlled with typical autopilot protocols such as RC PWM and 4-20 mA, and can also be communicated with protocols such as RS-422 and CANopen. We’ve expanded the mechanical capabilities of our Servo Cylinder platform to include options for additional vibration hardening and D38999 connectors, as well as a pressure-compensated oil-filled version for subsea operation.
Figure 4: The subsea AU Servo Cylinder (top) and the vibration hardened AM Servo Cylinder (bottom) are designed to offer best-in-class reliability and performance.
The content & opinions in this article are the author’s and do not necessarily represent the views of RoboticsTomorrow
Comments (0)
This post does not have any comments. Be the first to leave a comment below.
Featured Product
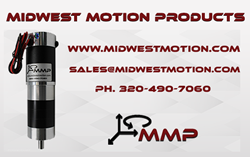