Industrial Dampers cushion vibrations in machines. In order to fulfill this task perfectly, there are a large number of different types. To find the right variant for your own application, the load cases should be examined in detail.
2021 Top Article - How to Find the Right Damper for Your Application
Article from | Zimmer Group
Nowadays, machines are performing increasingly complex tasks. As a result, the number of moving parts in machines is increasing, as are their speeds and thus their kinetic energies. But in order to avoid collisions, high impact forces and strong vibrations, which would lead to damage and thus to a reduction in service life, excess energy must be removed from the system. However, this also means that special components are needed to remove kinetic energy specifically at the points and in the situations where this would lead to damage. By integrating industrial dampers, safe operation can be achieved by reducing the load while simultaneously increasing the utilization of a machine. Industrial dampers can be used to control dynamics and speeds.
Configure the perfect damper
There are a few ways to find the right industrial damper for your application. The easiest and fastest way is to choose an online product finder, such as the one offered by Zimmer Group: https://www.zimmer-group.com/en/service/pre-sales/product-finder/industrial-damping-technology. Online sizing software greatly facilitates a calculation and selection of suitable industrial dampers, and an online product finder can be accessed by the user via PC, laptop, smartphone or tablet even without software installation. Such a convenient tool quickly leads to well-founded selection decisions and combines the functions of calculation, selection aid and configurator. With the software, the user can perform all the necessary calculations and, based on this data, make a selection from the product range and possibly supplement the selected product with additional accessories.
Translation or Rotation
In the first step of the product finder, the user can select between various load case which suit the application best. A basic distinction is made between translational and rotational movements in the load case. After that, it is necessary to select which translation the own damping application has, for example whether it has a freely falling mass (L1) or a downward moving mass with driving force (L2) or a falling mass on an inclined plane (L8). In total, there are eleven different load cases to choose from. If, however, the movement in the load case is rotational, it is necessary to select from corresponding load cases in the Product Finder. These include scenarios such as a freely oscillating mass with horizontal impact (R1a), a downward-moving mass with opposing drive torque with horizontal impact (R2a) or the case of a horizontally oscillating mass without drive torque (R5). A pictorial representation with the necessary parameters facilitates the use of the above-mentioned total of eleven (for translation) or seven (for rotation) damping scenarios.
Calculation for translational scenario
For the common application of a pneumatic cylinder with necessary damping of the end position, the calculation is made easier for the customer via the load case L6. Only the moving mass to be damped, the speed and the driving force of the cylinder have to be entered, and the appropriate dampers are displayed in a results table. The last step is to enter the operating mode of the shock absorber. Here it is important to know the following: There are two different operating modes for industrial dampers. Continuous operation represents a regular load on the industrial damper with a certain number of cycles per time unit. This results in heating of the industrial damper, whereby a certain operating temperature is established from the thermal equilibrium between heat absorption by the damping and heat dissipation to the environment. In emergency stop operation, the industrial damper is only used in exceptional situations or emergencies, for example in the event of a failure of the machine's control system. In this case, there is no number of cycles per unit of time, but the load does not occur at all in the best case or occurs at irregular or unpredictable intervals. Some industrial dampers are designed to absorb even more energy per stroke in emergency stop mode than in continuous mode. If several industrial dampers are used simultaneously, they can also be calculated for parallel or series connection. In this way, the energy absorption is distributed evenly among the dampers and the utilization per damper is calculated.
Calculation for rotatory scenario
Similar to a translational motion, a rotation has the following parameters. In our example "free swinging mass at horizontal impact", in addition to mass, velocity and height, further parameters such as the distance of the industrial damper to the center of rotation R and the distance of the center of mass to the center of rotation L are used in the calculation. After entering the values, the user then obtains a reliable result. From the values entered, the software calculates - automatically and individually for each industrial damper - values such as energy absorption per stroke and per hour, impact speed, and the respective load that the industrial damper is to absorb. The available elements that meet these specifications are displayed in a table that can be sorted by load per stroke or per hour as well as all technical data. Compared to existing solutions, this table shows both industrial dampers and structural industrial dampers, which can also be filtered. In the table, the energy absorption is calculated individually for each damper and its utilization is displayed. This makes it possible to assess whether an industrial damper is being operated near its performance limit and perhaps the next larger dimension should be selected, or whether a smaller variant would be the more suitable choice from an economic point of view.
Customized damper via filter
Due to the increasing number of variants, dampers can be precisely adapted to the ambient conditions, which is made possible by a filter in the product finder. In this way, a choice can be made between different series depending on performance. By choosing between normal or long-stroke versions, the appropriate support force can be selected depending on the space requirements. For optimum protection, a wiper can also be used to protect against liquids or oils. A felt ring, in turn, offers proven protection against dust and chips, for example in the woodworking industry. Complete protection is provided by a bellows with a complete seal, enabling use under the most adverse conditions, for example in the grinding machine under abrasive grinding dust, as well as when used in a clean room. Lastly, the optional impact head is selected in steel to reduce surface pressure or with a plastic insert for additional noise reduction.
Horizontally moving mass with form fit driving force
Freely oscillating mass at horizontal impact
The content & opinions in this article are the author’s and do not necessarily represent the views of RoboticsTomorrow
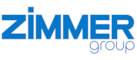
Zimmer Group US, Inc.
Are you interested in premium products in the fields of mechanical and plant engineering? Do you want to learn more about our solutions in the fields of automation, damping, linear, processing, tooling, and machine tooling technology?
Other Articles
Automate 2025 Q&A with Zimmer Group
Converting Passenger Aircraft to Freight Aircraft - the Zimmer Group Is on Board!
Automated Loading and Unloading of CNC Machines
More about Zimmer Group US, Inc.
Comments (0)
This post does not have any comments. Be the first to leave a comment below.
Featured Product
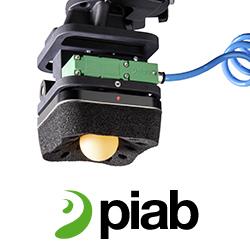