Over the past few years, all aspects of the warehousing sector have been automated and this naturally includes the materials handling processes. This automation has increased efficiency across the board as well as improving employee safety and productivity.
Optimizing Material Handling Processes for Increased Efficiency
Harry Thompson | Parvalux by maxon
Over the past few years, all aspects of the warehousing sector have been automated and this naturally includes the materials handling processes. This automation has increased efficiency across the board as well as improving employee safety and productivity.
As online shopping takes over from the high street, more and more large-scale distribution hub facilities and complex warehousing will be required nationwide. Businesses will be looking for ways to streamline their processes and make savings without compromising on delivery of services. Therefore, the more that warehousing processes can be fully automated, the more efficient the business will be, and the more savings can be made.
For many years Parvalux has been at the forefront of motor and gearbox design for the warehousing industry and you will find our geared motors in numerous applications in the materials handling processes including:
- Conveyor Systems – Geared motors are essential for conveyor systems to run. It’s necessary to have adjustable components as the speed is dependent on whether the conveyor is sorting, on incline, or straight transport and the torque required varies according to the weight and the friction of the materials being handled.
- Pallet and Tray Shuttles – Motors such as Parvalux’s PBL86 combined with the GB28 and GB9 gearboxes are essential to the safe running of pallet and tray shuttles. These geared motors offer high torque density as well as being both reliable and durable.
- Lifting Mechanisms – Lifts, hoists or cranes require geared motors to handle vertical movement whilst offering precise control when combined with a controller. Lifting heavy loads requires a significant amount of torque. Geared motors, which combine an electric motor with a gearbox, are able to provide the required high torque at low speeds.
- Warehouse Tugs – The combination of a motor such as the PBL86 and PBL70 with a gearbox like the GB12 enables the tug to move smoothly on a variety of surfaces within the warehouse, including smooth floors, ramps, or even slightly uneven terrain.
- Packaging Equipment – Machines used for packaging and palletizing require precise control of both speed and torque. Speed requirements might vary from high-speed packaging lines to slower, more controlled operations. Torque requirements depend on the machinery’s handling capacity.
- Automated Shrink Wrapping – Geared motors are essential for many aspects of automated shrink-wrapping systems including controlling the unwinding and dispensing of the shrink wrap film. They provide the necessary torque and precision to unwind the film rolls at a consistent speed, ensuring smooth and even application around the products being wrapped.
- Sorting and Distribution Systems – Systems used for sorting and distributing materials need a motor like the Parvalux BRx52 combined with the GB28 gearbox, which have varying speed and torque capabilities. The specific requirements vary dependent on the sorting complexity and the weight of items being handled.
- Automated Guided Vehicles (AGVs) – Motors and gearboxes like the GB12 power AGVs which are used for material transportation in warehouses or factories. Speed requirements can differ based on the required movement pace, while torque specification depends on the vehicle’s load capacity.
Each application has very specific speed and torque requirements dependant on the particular task and environment such as load capacity, speed of operation, precision needed and the nature of the materials being handled.
Tailoring the gear ratio, motor size, and specifications to match these requirements is crucial for successful integration and performance within each application. Choosing the right combination of motor and gearbox can ensure optimal performance, efficiency and safety. All of our motors can be configured to match such requirements.
At Parvalux, we pride ourselves on having the expertise in engineering and designing the perfect combination of motors and gearboxes for optimal performance. One of the most common combinations is the PBL86 motor and the GB12 gearbox.
The PBL86 is known for its high torque output, compact size, reliability and durability. This motor offers a wide speed range – allowing precise control when connected to a controller. Combined with the GB12 gearbox, itself boasting a small footprint whilst enhancing torque transmission, creates an extremely powerful motor which can handle heavier loads. This gearbox enables precise control over the speed and movement of the system which is vital in many materials handling applications that require accurate positioning, as well as controlled acceleration and deceleration.
Benefits of Parvalux Motors
By introducing Parvalux motors and gearboxes to your materials handling applications, you can benefit from optimized output in several ways including:
- Enhanced Performance – By using Parvalux motors and gearboxes in materials handling equipment, such as conveyors or lifting mechanisms, companies can achieve smoother and more consistent operations, whilst reducing downtime and increasing overall efficiency.
- Increased Durability – Our motors and gearboxes are built to withstand heavy-duty usage. Their robust construction and high-quality materials ensure longevity, reducing maintenance requirements and minimizing equipment downtime, thereby improving overall productivity.
- Customization and Adaptability – Our motors come in a wide variety of sizes and configurations, offering flexibility in design and integration. This means it is possible to select components that precisely match specific materials handling requirements, allowing for tailored solutions that optimize performance and efficiency.
- Energy Efficient – Using the Parvalux range of motors can reduce power consumption in the materials handling systems, leading to cost savings and environmental benefits.
- Precise Control and Speed Regulation – Adding a controller to a motor/gearbox combination can help to increase the control and set a particular speed. This level of control can improve safety, accuracy, and productivity in materials handling processes.
- Reliability and Consistency – Parvalux products’ consistent performance ensures that the materials handling processes remain stable, minimizing errors and disruptions in production or logistics.
- Integration with Automation – As automation becomes more prevalent in materials handling, Parvalux motors and gearboxes can seamlessly integrate with automated systems already in place. This integration leads to smoother workflows, reduced manual labour, and increased throughput.
Parvalux designs and manufactures an exciting range of AC, DC, brushless and brushed motors and our drives are valued for their performance and reliability. Geared motors come in a variety of configurations, allowing for customization ensuring all your materials handling requirements can be met.
If you would like to learn more about how our products are able to help in your materials handling projects, you can access our product page here or speak to the team if you would like to discuss a more bespoke option.
The content & opinions in this article are the author’s and do not necessarily represent the views of RoboticsTomorrow
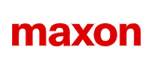
maxon group
maxon is a leading supplier of high-precision DC brush and brushless servo motors and drives. These motors range in size from 4 - 90 mm and are available up to 500 watts. We combine electric motors, gears and DC motor controls into high-precision, intelligent drive systems that can be custom-made to fit the specific needs of customer applications.
Other Articles
Understanding Torque and Speed in Electric Motors
How Parvalux Is Helping to Develop the Next Generation of Conveyor Systems
Robots speeding up material handling
More about maxon group
Comments (0)
This post does not have any comments. Be the first to leave a comment below.
Featured Product
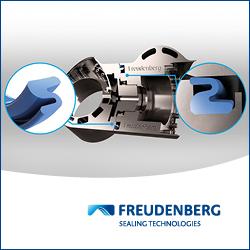