A force sensor measures mechanical forces, like a secret handshake between machines and the real world. These ingenious devices convert mechanical force into electrical signals, enabling us to measure, analyze, and interact with the physical world around us.
Understanding Force Sensors: How They Work and Measure Force
Ilias Patsiaouras | Bota Systems
Ever wondered how your phone knows when you tap the screen, or how robots know how much to squeeze an object? It's all thanks to tiny sensors called force sensors!
A force sensor measures mechanical forces, like a secret handshake between machines and the real world. These ingenious devices convert mechanical force into electrical signals, enabling us to measure, analyze, and interact with the physical world around us.
From the delicate touch of a finger on a smartphone screen to the immense weight of a skyscraper, force sensors provide the essential data that drives countless applications across diverse industries.
What is a Force Sensor and How it works?
Force sensor working principle
Force Sensor Types
Strain Gauge Force Sensor Technology:
When force is applied, the sensor deforms, causing the strain gauges to stretch or compress. This change in physical dimension alters the electrical resistance of the strain gauges and by measuring this resistance change, we can calculate the applied force.
Piezoresistive Technology:
When force is applied, the silicon's resistance changes, generating a measurable electrical signal.
Piezoresistive sensors offer high sensitivity and are often used in miniature force sensors for delicate applications.
Capacitive Technology:
This method relies on the principle of capacitance, which relates to the ability of a capacitor to store electrical charge. A force sensor with capacitive technology typically consists of two parallel conductive plates.
When force is applied, the distance between the plates changes, causing a variation in capacitance and by measuring this change in capacitance, the applied force can be determined.
Capacitive sensors are often used in touchscreens and proximity sensors due to their ability to detect small forces.
Piezoelectric Technology:
When force is applied, it creates a deformation in the crystal, leading to the generation of a piezoelectric effect. This voltage output is directly proportional to the applied force, offering a simple and direct measurement.
Piezoelectric force sensors are commonly used in impact detection, vibration monitoring, and high-force applications.
Magnetic Force Sensors:
These force sensors utilize the principle of magnetostriction, where a material's magnetic properties change under mechanical stress.
A ferromagnetic material within the force sensor experiences a change in its magnetic permeability when force is applied. This change is detected by coils or other magnetic sensors, generating an electrical signal proportional to the applied force.
Magnetic force sensors offer high sensitivity and are well-suited for low-force measurements in applications like biomechanics and microfluidics.
Optical Force Sensors:
These force sensors rely on changes in light properties caused by the applied force. Various techniques are employed in these sensors, such as fiber Bragg gratings and interferometry. In fiber Bragg grating force sensors, a tiny grating inscribed within an optical fiber reflects light at a specific wavelength.
When force is applied, the grating's structure changes, altering the reflected wavelength, which can be measured to determine the force. Interferometric sensors utilize the principle of interference of light waves to detect minute changes in distance caused by force.
Optical force sensors offer high precision and are often used in scientific research and microscopic measurements.
Acoustic Emission Sensors:
These force sensors detect acoustic waves (sound) emitted by a material when it undergoes stress or deformation due to applied force.
The frequency and intensity of these acoustic emissions carry information about the type and magnitude of force and by analyzing these acoustic signals, the applied force can be determined.
Acoustic emission sensors are valuable for damage detection in materials, monitoring machinery health, and identifying structural weaknesses.
Biomimetic Force Sensors:
Inspired by nature, these sensors mimic the biological mechanisms used by living organisms to sense force. Examples include artificial whiskers inspired by animal whiskers and electronic skin mimicking human skin's pressure sensitivity.
These force sensors offer highly sensitive and adaptable force measurement capabilities, potentially revolutionizing fields like prosthetics and robotic manipulation.
Choosing the right Force Sensor
1. How Much Force Can It Handle?
2. How Sensitive is it?
For example, weighing a tiny diamond needs a very sensitive sensor, while measuring the weight of a truck requires a less sensitive one.
3. What Environment Will it Be In?
Choose a force sensor that can handle those conditions without getting damaged or giving inaccurate readings.
4. Does it Fit the Space?
Make sure the force sensor you choose is the right size for the space you have available.
5. How Much Can You Afford?
Just like any other tool, force sensors come in different price ranges. Consider your budget and choose a force sensor that offers the features you need at a price you can afford.
How Force Sensors are Revolutionizing Robotics with Bota Systems
This isn't science fiction. Bota Systems is making it possible with their innovative force-torque sensors, giving robots the power of touch.
Force sensors act like translators for robots. They empower robots to:
-
Feel how much force they're using: No more crushing delicate objects or accidentally hurting people!
-
Know exactly where they're touching: This is crucial for precise tasks like assembling tiny parts or performing surgery.
-
Respond to their environment: Robots can adjust their movements based on what they feel, making them safer and more versatile.
Bota Systems: Pioneering the Future of Force Sensors:
They can sense force in different directions, like up, down, and sideways. Moreover, they are customizable and tough enough to handle even the most demanding jobs. Their product line includes:
-
MiniONE Pro: The smallest and most sensitive force-torque sensor, ideal for tasks requiring exceptional precision in tight spaces.
-
MegaONE: An industrial-grade sensor for advanced applications in automation and research, offering robust performance for demanding environments.
-
LaxONE: A lightweight and versatile sensor well-suited for collaborative robots, enabling safe and effective interaction with humans.
Explore Bota Systems' website to learn more about their specific products and how they can empower your next robotic project. Together, we can shape the future of robotics with the power of touch!
The content & opinions in this article are the author’s and do not necessarily represent the views of RoboticsTomorrow
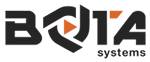
Bota Systems AG
We give robots the sense of touch - Bota Systems' vision is for robots to work and move safely and as naturally and freely as human beings. As a developer and manufacturer of multi-axis force-torque sensors, torque sensors, and custom sensors, we strive to provide the best force-torque sensing solutions and user care experience. Our team of robotics, software and mechanical engineers continually develops highly-integrated and advanced sensors to support a wide range of applications.
Other Articles
Mecademic robots achieve sense of touch with Bota sensors
Painting Robots: Benefits, Applications, and Sourcing Tips
More about Bota Systems AG
Comments (0)
This post does not have any comments. Be the first to leave a comment below.
Featured Product
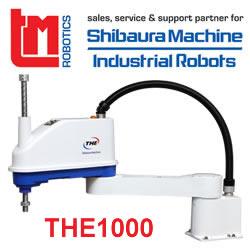