The recent developments at Amazon's new robotic warehouse in Shreveport, Louisiana, offer valuable insights into this complex interplay between human workers and advanced technologies.
The Future of Manufacturing: Harmonizing Human Talent and Automation
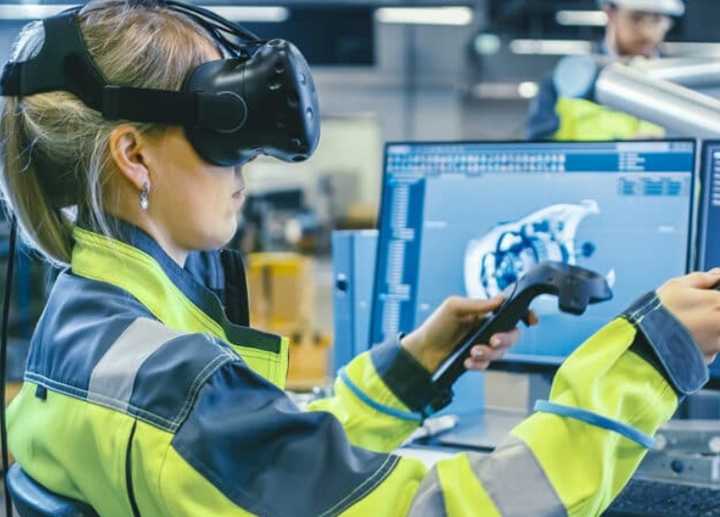
Dijam Panigrahi, Co-founder and COO | GridRaster Inc.
The manufacturing landscape has been redefined by the rapid advancement of automation and robotics technologies, but companies are now faced with the opportunity to evolve their strategies even further. As industry leaders navigate this new terrain, they face a critical challenge: how to effectively integrate human capital with cutting-edge AI-powered automation solutions.
The recent developments at Amazon's new robotic warehouse in Shreveport, Louisiana, offer valuable insights into this complex interplay between human workers and advanced technologies.
Amazon’s Need for Automation and Human Capital
While Amazon's three-million-square-foot distribution center showcases the company's most automated warehouse to date, it also highlights a stark reality that manufacturers across various sectors must recognize. Despite the extensive use of robotics and artificial intelligence throughout the fulfillment process, the facility still relies heavily on human workers, with plans to employ 2,500 individuals for tasks ranging from order picking to managing robotics systems.
This scenario is not unique to e-commerce giants like Amazon. Manufacturers in aerospace, automotive, industrial equipment, medical devices, and even construction are grappling with similar challenges as they seek to optimize their production and operational strategies.
The key lies in recognizing that the future of manufacturing is not about replacing humans with robots, but rather about creating a symbiotic relationship between the two.
One of the primary reasons for this continued reliance on human workers is the incredible versatility and adaptability of the human mind and body. As Tye Brady, chief technologist at Amazon Robotics, points out in a recent news interview, "The tactile grasp that the human hand has, and the situational awareness and the perception of the human brain, is unmatched".
This observation holds true across manufacturing sectors, where the ability to handle diverse products, make quick decisions, and adapt to changing circumstances remains a uniquely human trait.
Consider the aerospace industry, where precision and safety are paramount. While robots can perform repetitive tasks with high accuracy, human expertise remains important for quality control, complex assembly processes, and troubleshooting unexpected issues. Similarly, in the automotive sector, advanced robotics have revolutionized production lines, but skilled workers are still essential for fine-tuning, customization, and ensuring the overall quality of the finished product.
The medical device manufacturing industry presents another compelling case for human-robot collaboration. While automation can enhance precision and consistency in producing standardized components, the intricate nature of many medical devices and the need for stringent quality control often require human oversight and expertise. Moreover, as medical technology continues to advance, the ability to quickly adapt production processes to new innovations is a task better suited to human ingenuity than pre-programmed robots.
In the realm of industrial equipment and supply chain management, the unpredictability of demand and the need for customization further underscore the importance of maintaining a skilled human workforce. Robots excel at handling routine tasks and moving large volumes of standardized goods, but human workers are essential for managing exceptions, making real-time decisions, and ensuring customer satisfaction through personalized service.
The construction industry, traditionally reliant on manual labor, is also exploring ways to integrate automation and robotics. However, the complex and often unpredictable nature of construction sites means that human workers will remain indispensable for the foreseeable future. The challenge here lies in finding ways to use technology to enhance worker safety and productivity rather than replace human labor entirely.
As manufacturers across these diverse sectors plan their strategies for integrating human labor with automation, several key considerations emerge:
Redefining roles and responsibilities: Rather than viewing automation as a replacement for human workers, companies should focus on redefining roles to leverage the strengths of both humans and machines. This might involve creating new positions that focus on managing and maintaining robotic systems, as Amazon has done in its Shreveport facility.
Investing in training and skill development: As the nature of manufacturing work evolves, companies must invest in comprehensive training programs to equip their workforce with the skills needed to work alongside advanced technologies. This includes not only technical skills but also soft skills such as problem-solving, critical thinking, and adaptability.
Prioritizing safety and ergonomics: The integration of robotics and automation presents an opportunity to improve workplace safety by assigning physically demanding or repetitive tasks to machines. However, it's crucial to ensure that the human-robot interface is designed with worker safety in mind.
Fostering a culture of innovation: Encouraging employees at all levels to contribute ideas for improving processes and integrating new technologies can lead to more effective and widely accepted automation strategies.
Balancing efficiency with flexibility: While automation can significantly boost efficiency, it's important to maintain enough flexibility to adapt to changing market demands and unforeseen circumstances. Human workers play a crucial role in providing this adaptability.
Automation and Humans Powering Virtual Tasks
One particularly promising area for human-robot collaboration in manufacturing is the use of AI-powered Augmented Reality (AR) and Virtual Reality (VR) technologies. These immersive technologies are modernizing various aspects of the manufacturing process, from design and production to employee training and customer interactions. Importantly, they exemplify how advanced technology can enhance rather than replace human capabilities.
In the design phase, AR and VR allow engineers and designers to visualize and manipulate 3D AI models in a virtual space, facilitating more efficient and innovative product development. During production, AR can provide workers with real-time information and guidance, overlaying digital instructions onto the physical work environment. This not only improves accuracy and efficiency but also reduces the learning curve for complex tasks.
For employee training, VR simulations offer a safe and cost-effective way to familiarize workers with new equipment or processes without disrupting actual production. These immersive training experiences can significantly reduce errors and improve retention of information compared to traditional training methods.
3D AI-powered AR and VR are also transforming customer interactions in the manufacturing sector. Virtual site visits and product demonstrations allow customers to explore and interact with products or facilities remotely, opening up new possibilities for sales and customer support.
It’s also important to note that the effective implementation of AR and VR solutions still relies heavily on human expertise. Skilled workers are needed to develop and maintain these systems, interpret the data they generate, and make informed decisions based on the insights provided. This underscores the ongoing importance of human capital in even the most technologically advanced manufacturing environments.
It's clear that the most successful strategies will be those that effectively balance human skills with technological capabilities. The example of Amazon's Shreveport warehouse, while instructive, is just one piece of a much larger puzzle. Manufacturers across all sectors must recognize that the path forward is not about choosing between humans and robots, but about finding innovative ways to combine the strengths of both.
The challenges are significant, but so are the opportunities. By embracing a collaborative approach to automation, investing in their workforce, and leveraging emerging technologies like AR and VR, manufacturers can create more efficient, safer, and more adaptable production environments. In this new paradigm, human workers are not replaced by machines but are empowered by them, leading to a more resilient and innovative manufacturing sector capable of meeting the complex demands of the 21st century.
Dijam Panigrahi is Co-founder and COO of GridRaster Inc., a leading provider of cloud-based AR/VR platforms that power compelling high-quality AR/VR digital twin experiences on mobile devices for enterprises. For more information, please visit www.gridraster.com.
The content & opinions in this article are the author’s and do not necessarily represent the views of RoboticsTomorrow
Comments (0)
This post does not have any comments. Be the first to leave a comment below.
Featured Product
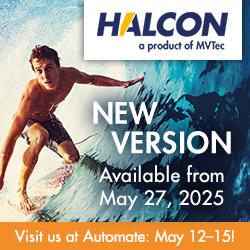