Non-Contact Vibration Measurement System Uses High-Speed Mikrotron Camera
Monitoring industrial machinery for vibration will pinpoint when amplitudes cross a permissible threshold. "Amplitude" is how vibrations are measured and refers to the amount of energy transferred by a wave.
Gilching, Germany, January 27, 2025 -- Excessive vibration in industrial machinery can cause significant damage to bearings, shafts and fasteners, ultimately leading to unscheduled downtime. Other consequences range from increased energy consumption and disruptive noise levels, to decreased machine lifespan and potential safety hazards.
Monitoring industrial machinery for vibration will pinpoint when amplitudes cross a permissible threshold. "Amplitude" is how vibrations are measured and refers to the amount of energy transferred by a wave. Traditionally, vibration amplitudes are measured with contact-based discrete sensors such as accelerometers. However, these sensors provide only localized vibration readings on machinery. Moreover, installation of the sensor can be complex and expensive, coupled with an increased need for maintenance to ensure accuracy in harsh industrial environments.
NON-CONTACT VIBRATION MEASUREMENT
Advances in image processing techniques has made it possible to monitor vibration levels with on-line, non-contact vision-based systems. For instance, researchers at the College of Engineering Pune (COEP) in Pune, India have developed a new vision system that's comparable in speed and accuracy with physical sensors.
COEP's solution consists of a Mikrotron EoSens CL camera set to continuously capture 300 x 300 pixel resolution monochrome video at 20 frames per second, along with a PC workstation equipped with an Intel xeon CPU, a vibrating platform, a stepper motor, a scale, and a checkerboard template for visual reference. VisualiMarc software is used to acquire video at the desired frame rate and resolution. The system then employs computer vision algorithms to analyze the pixel movement in the video.
TESTING PROCEDURE
To begin the experiment, a target machine is placed on the vibrating platform that's driven by the stepper motor. As the machine vibrates, the Mikrotron camera tracks its movement by focusing on several distinctive visible features. By comparing feature movements against the static checkerboard template on the wall, analysis of pixel displacement can be performed, allowing for precise measurement of the entire target in real-time and without physical contact.
In the presence of vibration, pixel locations will change frame-by-frame and these translational shifts are calculated by phase-correlation. Horizontal and vertical pixel shifts can be used to extract the amplitude and frequency of vibration. Sub-pixel motion estimation has also been included in the algorithm to achieve better accuracy of smaller amplitude vibrations.
COEP created its motion extraction algorithm with Visual Studio C++ and OpenCV, providing a simple and intuitive way to determine movement between the vibrating target and the checkerboard. The algorithm can extract vibration signals with impressive efficiency which helps the system realize faster processing.
Learn more about Mikrotron cameras at www.mikrotron.de.
Featured Product
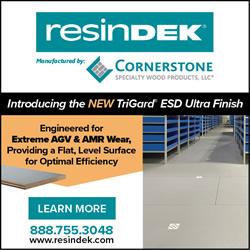
ResinDek® TRIGARD® ESD ULTRA FOR HIGH-TRAFFIC ROBOTIC APPLICATIONS
To maximize the productivity of an autonomous mobile robot (AMR) or automatic guided vehicle (AGV) deployment, it's critical to create the optimal environment that allows the vehicles to perform at their peak. For that reason, Cornerstone Specialty Wood Products, LLC® (www.resindek.com) created the TriGard® ESD Ultra finish for its ResinDek® engineered flooring panels. The TriGard ESD Ultra finish is ideal for high-traffic robotic applications characterized by highly repetitive movement patterns and defined travel paths.