Enhancing Equipment Reliability: Implementing xPump – AI/ML-Based Pump Monitoring & Predictive Maintenance System on Turbomolecular Pumps with Integrated EPX On-Tool High Vacuum Pump EPX180L
Implementing xPump - AI/ML-Based Pump Monitoring & Predictive Maintenance System on Turbomolecular Pumps with Integrated EPX On-Tool High Vacuum Pump EPX180L
In today's fast-paced industrial environment, equipment reliability is paramount. Downtime due to equipment failure can lead to significant financial losses, reduced productivity, and compromised safety. This is especially true for critical components like turbomolecular pumps, which are essential in high-vacuum applications such as semiconductor manufacturing, analytical instrumentation, and research laboratories. To address these challenges, the integration of advanced technologies like Artificial Intelligence (AI) and Machine Learning (ML) into equipment monitoring and maintenance systems has become a game-changer. One such innovative solution is xPump, an AI/ML-based pump monitoring and predictive maintenance system designed specifically for turbomolecular pumps, including the integrated EPX on-tool high vacuum pump EPX180L.
In this blog, we will explore how xPump enhances equipment reliability, reduces downtime, and optimizes maintenance processes. We'll also discuss the benefits of implementing this system and provide a call to action for industries looking to revolutionize their maintenance strategies.
The Importance of Equipment Reliability in High-Vacuum Applications
Turbomolecular pumps are critical components in high-vacuum systems, ensuring the efficient removal of gases and maintaining the required vacuum levels. However, these pumps operate under extreme conditions, including high rotational speeds and exposure to corrosive or abrasive gases. Over time, wear and tear can lead to performance degradation or unexpected failures, resulting in costly downtime and production delays.
Traditional maintenance approaches, such as reactive or scheduled maintenance, are no longer sufficient in today's demanding industrial landscape. Reactive maintenance addresses issues only after they occur, often leading to extended downtime and higher repair costs. Scheduled maintenance, while proactive, can be inefficient, as it may involve unnecessary servicing of equipment that is still functioning optimally.
This is where predictive maintenance comes into play. By leveraging AI and ML, predictive maintenance systems like xPump can monitor equipment in real-time, detect early signs of potential failures, and provide actionable insights to prevent unplanned downtime.
What is xPump?
xPump is an advanced AI/ML-based monitoring and predictive maintenance system designed specifically for turbomolecular pumps, including the EPX180L integrated high vacuum pump. It combines state-of-the-art sensor technology, data analytics, and machine learning algorithms to provide real-time insights into pump performance and health.
Key Features of xPump:
Real-Time Monitoring: xPump continuously monitors critical parameters such as vibration, temperature, pressure, and power consumption, providing a comprehensive view of pump health.
Predictive Analytics: Using machine learning algorithms, xPump analyzes historical and real-time data to predict potential failures before they occur.
Early Warning System: The system generates alerts and notifications when anomalies are detected, allowing maintenance teams to take corrective action proactively.
Performance Optimization: xPump provides recommendations for optimizing pump performance, reducing energy consumption, and extending equipment lifespan.
Integration with EPX180L: xPump is fully compatible with the EPX180L integrated high vacuum pump, ensuring seamless operation and enhanced reliability.
Benefits of Implementing xPump
Implementing xPump on turbomolecular pumps, including the EPX180L, offers numerous benefits for industries relying on high-vacuum systems. Here are some of the key advantages:
1. Reduced Downtime
By predicting potential failures before they occur, xPump minimizes unplanned downtime, ensuring continuous operation and maximizing productivity. This is particularly critical in industries like semiconductor manufacturing, where even a few minutes of downtime can result in significant financial losses.
2. Lower Maintenance Costs
xPump's predictive maintenance capabilities enable maintenance teams to address issues before they escalate, reducing the need for costly repairs and replacements. Additionally, the system eliminates unnecessary scheduled maintenance, further lowering operational costs.
3. Extended Equipment Lifespan
By optimizing pump performance and preventing premature failures, xPump helps extend the lifespan of turbomolecular pumps, providing a higher return on investment.
4. Improved Safety
Early detection of potential failures reduces the risk of catastrophic equipment breakdowns, enhancing workplace safety and minimizing the risk of accidents.
5. Enhanced Operational Efficiency
xPump's real-time monitoring and performance optimization features ensure that pumps operate at peak efficiency, reducing energy consumption and improving overall system performance.
6. Data-Driven Decision Making
xPump provides actionable insights based on real-time and historical data, enabling informed decision-making and strategic planning.
How xPump Works with the EPX180L Integrated High Vacuum Pump
The EPX180L is a compact, high-performance turbomolecular pump designed for on-tool applications in semiconductor manufacturing and other high-vacuum processes. When integrated with xPump, the EPX180L becomes even more reliable and efficient.
Integration Process:
Sensor Installation: xPump sensors are installed on the EPX180L to monitor key parameters such as vibration, temperature, and pressure.
Data Collection: The sensors continuously collect data and transmit it to the xPump analytics platform.
Data Analysis: xPump's AI/ML algorithms analyze the data to identify patterns, detect anomalies, and predict potential failures.
Actionable Insights: The system generates real-time alerts and provides recommendations for maintenance and performance optimization.
Continuous Improvement: Over time, xPump's machine learning models become more accurate, further enhancing its predictive capabilities.
Real-World Applications of xPump
xPump is already making a significant impact in various industries that rely on turbomolecular pumps. Here are a few examples:
1. Semiconductor Manufacturing
In semiconductor manufacturing, maintaining a high vacuum is critical for processes like etching, deposition, and lithography. xPump ensures that turbomolecular pumps operate reliably, minimizing downtime and improving yield.
2. Analytical Instrumentation
In analytical instruments such as mass spectrometers and electron microscopes, turbomolecular pumps are essential for creating and maintaining a vacuum. xPump helps ensure consistent performance and reduces the risk of instrument failure.
3. Research Laboratories
Research laboratories often rely on turbomolecular pumps for experiments requiring high vacuum conditions. xPump provides peace of mind by ensuring that pumps operate reliably and efficiently.
Call to Action: Revolutionize Your Maintenance Strategy with xPump
In an era where equipment reliability is more important than ever, xPump offers a cutting-edge solution for enhancing the performance and longevity of turbomolecular pumps. By implementing xPump on your EPX180L integrated high vacuum pump or other turbomolecular pumps, you can:
Reduce downtime and maintenance costs
Extend equipment lifespan
Improve safety and operational efficiency
Make data-driven decisions for better outcomes
Don't wait for the next equipment failure to disrupt your operations. Take a proactive approach to maintenance with xPump and experience the benefits of AI/ML-driven predictive maintenance.
Contact us today to learn more about xPump and how it can transform your maintenance strategy. Our team of experts is ready to assist you in implementing this innovative solution and ensuring the reliability of your high-vacuum systems.
Featured Product
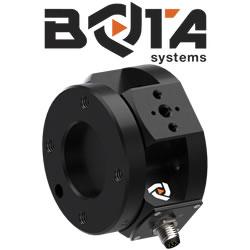