Unlocking Efficiency: The Power of Predictive Maintenance for Industrial Equipment
As technology continues to advance, industries are constantly seeking ways to improve their operational efficiency and reduce downtime. That's where the power of predictive maintenance for industrial equipment comes in. By harnessing the capabilities of artificial intelligence and data analytics, businesses can now anticipate equipment failures and take preventive measures to minimize disruptions and costly repairs.
Predictive maintenance is revolutionizing the way industries approach equipment maintenance. Instead of relying on traditional reactive maintenance, which can lead to unexpected breakdowns and prolonged downtimes, predictive maintenance uses real-time data and machine learning algorithms to predict when maintenance is needed. This proactive approach allows businesses to optimize their maintenance schedules, reduce downtime, and increase overall operational efficiency.
By implementing predictive maintenance, industrial businesses can not only save time and money but also ensure that their equipment operates at peak performance. Additionally, it enables them to detect and rectify potential issues before they become major problems, resulting in improved productivity and customer satisfaction.
In this article, we will delve into the power of predictive maintenance for industrial equipment, exploring its benefits, implementation strategies, and success stories from various industries. Join us as we unlock the gateway to enhanced efficiency and profitability through the world of predictive maintenance.
The importance of predictive maintenance for industrial equipment
Predictive maintenance has emerged as a critical strategy for industries aiming to enhance their operational efficiency. This approach focuses on forecasting equipment failures before they occur, allowing organizations to implement maintenance activities at the most opportune times. By transitioning from traditional maintenance methods, companies can significantly reduce the risks associated with unexpected breakdowns, which often lead to unscheduled downtime and loss of productivity. The importance of predictive maintenance lies not only in its ability to prevent failures but also in optimizing resource allocation and operational workflows.
In an environment where every minute of downtime can translate into substantial financial losses, predictive maintenance serves as a proactive measure that addresses potential issues before they escalate. It leverages data collected from various sensors and monitoring devices installed on industrial equipment. By analyzing this data, businesses can gain insights into equipment health and performance trends, which ultimately informs decision-making regarding maintenance schedules. This foresight helps in maintaining continuous operations and enhances the overall reliability of machinery.
Moreover, predictive maintenance contributes to a culture of continuous improvement within organizations. As companies become more adept at utilizing data analytics and machine learning, they start to foster innovation and adapt to emerging technologies. This forward-thinking mindset not only benefits equipment management but also encourages employees to embrace technological advancements as integral components of their work processes. As such, the importance of predictive maintenance extends beyond immediate operational benefits, paving the way for a more resilient and adaptable industrial landscape.
Key benefits of implementing predictive maintenance
Implementing predictive maintenance offers numerous advantages that can significantly impact an organization's bottom line. One of the primary benefits is the reduction of maintenance costs. Traditional maintenance strategies often involve routine inspections and repairs, which can lead to unnecessary expenditures. Predictive maintenance, on the other hand, allows businesses to conduct maintenance activities only when needed, thereby minimizing labor costs and extending the lifespan of equipment. This targeted approach means that resources are utilized more efficiently, leading to a more sustainable maintenance budget.
Another key benefit is the enhancement of operational efficiency. With predictive maintenance, equipment can be serviced based on real-time data rather than fixed schedules. This flexibility means that maintenance can be performed during scheduled downtimes, thus avoiding interruptions to production. As a result, organizations can achieve higher levels of productivity and ensure that machinery operates at optimal performance levels. The ability to anticipate issues further enhances efficiency, as it reduces the likelihood of sudden failures that disrupt workflows.
In addition to cost savings and operational efficiency, predictive maintenance also improves safety within the workplace. By identifying potential equipment failures before they occur, companies can reduce the risk of accidents and injuries caused by malfunctioning machinery. A safer working environment not only protects employees but also fosters a culture of safety that can improve employee morale and retention. This holistic approach to maintenance — prioritizing safety, efficiency, and cost-effectiveness — exemplifies the comprehensive benefits that come from implementing predictive maintenance strategies.
Predictive maintenance tools and technologies
The effectiveness of predictive maintenance is largely dependent on the tools and technologies employed to gather and analyze data. One of the most significant advancements in this area is the integration of the Internet of Things (IoT) into industrial settings. IoT devices equipped with sensors can monitor equipment in real-time, providing continuous streams of data regarding performance metrics such as temperature, vibration, and pressure. This wealth of information forms the foundation for predictive analytics, enabling organizations to identify trends and detect anomalies that may indicate impending failures.
Machine learning algorithms play a crucial role in predictive maintenance by processing vast amounts of data to identify patterns and correlations that human analysts might miss. These algorithms can learn from historical data to improve their predictions over time, leading to increasingly accurate forecasts of equipment failure. Advanced analytics platforms can further enhance this process by offering visualization tools that allow maintenance teams to interpret data intuitively, making it easier to prioritize maintenance tasks based on urgency and potential impact.
Cloud computing has also revolutionized the predictive maintenance landscape by enabling companies to store and analyze data at scale. By leveraging cloud-based solutions, organizations can access advanced analytics and machine learning capabilities without the need for significant investments in on-premises infrastructure. This democratization of technology allows even small to medium-sized enterprises to implement predictive maintenance strategies, leveling the playing field and fostering competition across industries. As these tools and technologies continue to evolve, they will further empower businesses to unlock the full potential of predictive maintenance.
Steps to implement a predictive maintenance program
Implementing a predictive maintenance program requires a structured approach to ensure its effectiveness and sustainability. The first step is to define clear objectives that align with the organization's overall maintenance strategy. This involves identifying key performance indicators (KPIs) that will help measure the success of the predictive maintenance initiative. Establishing these goals upfront provides a roadmap that guides the implementation process and helps garner support from stakeholders across the organization.
Next, organizations must invest in the necessary technologies and tools to support predictive maintenance efforts. This includes selecting appropriate sensors, IoT devices, and analytics platforms that can capture and process data effectively. It's also essential to ensure that employees are trained to use these technologies, as successful implementation hinges on the ability of the workforce to interpret data and act on insights. Investing in employee training and development not only enhances the effectiveness of the predictive maintenance program but also fosters a culture of continuous improvement.
Once the technology and training components are in place, organizations should initiate a pilot program to test their predictive maintenance strategies. This phase allows companies to refine their processes, gather feedback, and identify any challenges that may arise during implementation. By starting with a smaller-scale project, organizations can address issues proactively and make necessary adjustments before rolling out the program on a larger scale. Continuous monitoring and evaluation of the pilot program will provide valuable insights that can inform future maintenance strategies and ensure that the predictive maintenance program delivers on its promises.
Case studies showcasing successful predictive maintenance implementations
Case studies of successful predictive maintenance implementations provide valuable insights into the practical applications and benefits of this approach across various industries. One notable example is a leading manufacturer in the automotive sector that adopted predictive maintenance to enhance its assembly line operations. By installing IoT sensors on critical machinery, the company was able to collect data on equipment vibration and temperature. This data was analyzed using machine learning algorithms to predict potential failures, enabling the manufacturer to schedule maintenance during planned downtimes. As a result, the company reported a 30% reduction in unscheduled downtime and significant cost savings in maintenance expenses.
Another compelling case study comes from a major utility company that implemented predictive maintenance for its power generation equipment. By utilizing advanced analytics and machine learning, the utility was able to monitor the health of turbines and generators in real time. This proactive approach allowed the company to identify potential issues before they resulted in costly outages. The utility reported a 25% increase in overall equipment effectiveness, leading to improved service reliability for customers and enhanced operational efficiency. This case demonstrates how predictive maintenance can drive tangible improvements in performance and customer satisfaction.
In the aviation industry, a prominent airline adopted predictive maintenance to enhance the reliability of its fleet. By leveraging data from aircraft sensors, the airline developed predictive models that could forecast maintenance needs based on actual flight data. This initiative allowed the airline to optimize maintenance schedules and reduce aircraft downtime. The airline reported a 40% reduction in maintenance-related delays, leading to increased customer satisfaction and improved operational performance. These case studies illustrate that predictive maintenance is not limited to specific sectors but can be adapted to various industries, delivering significant benefits regardless of the operational context.
Common challenges in implementing predictive maintenance and how to overcome them
Despite the numerous benefits of predictive maintenance, organizations often face challenges when implementing this approach. One common hurdle is the integration of new technologies with existing systems. Many companies have legacy equipment and outdated maintenance practices that can complicate the adoption of predictive maintenance strategies. To overcome this challenge, organizations should assess their current systems and develop a phased approach to implementation. This may involve upgrading legacy systems incrementally or integrating predictive maintenance tools that can work alongside existing infrastructure.
Another significant challenge is the cultural shift required within the organization. Employees may be resistant to change, particularly when it comes to adopting new technologies and data-driven decision-making processes. To foster a culture that embraces predictive maintenance, leadership must actively engage employees in the process. This can be achieved through training programs that emphasize the value of predictive maintenance and its positive impact on job performance. Involving employees in pilot projects can also help build buy-in and demonstrate the effectiveness of the new approach.
Data quality and availability also pose challenges in predictive maintenance implementations. Accurate predictions depend on high-quality data, but organizations often struggle with incomplete or inconsistent data sets. To address this issue, companies should prioritize data management practices, ensuring that data is collected consistently and stored in a centralized system. Establishing clear data governance policies can help maintain data integrity and facilitate better analytics. By proactively addressing these common challenges, organizations can pave the way for successful predictive maintenance implementations that drive operational excellence.
Predictive maintenance vs. preventive maintenance: understanding the difference
Understanding the distinction between predictive maintenance and preventive maintenance is crucial for organizations seeking to optimize their maintenance strategies. Preventive maintenance involves scheduled maintenance activities performed at regular intervals, regardless of the actual condition of the equipment. This approach is based on the belief that routine servicing can prevent breakdowns. While preventive maintenance can be effective in certain scenarios, it often leads to unnecessary maintenance activities and associated costs, as many scheduled tasks may not be needed if the equipment is operating optimally.
Conversely, predictive maintenance focuses on data-driven insights to determine when maintenance should be performed. By analyzing real-time data from sensors and monitoring systems, organizations can predict when a piece of equipment is likely to fail. This allows for maintenance to be scheduled only when necessary, reducing costs and minimizing disruptions. The predictive approach enables businesses to extend the lifespan of their equipment and enhance overall operational efficiency, as maintenance is based on actual equipment health rather than arbitrary timelines.
The choice between predictive and preventive maintenance ultimately depends on the organization's specific needs and operational context. While preventive maintenance may still play a role in certain industries or for specific types of equipment, the growing trend is towards predictive maintenance as organizations seek to leverage technology and data analytics for improved performance. By understanding the differences between these two maintenance strategies, companies can make informed decisions that align with their goals and drive greater efficiency in their operations.
Predictive maintenance best practices for maximizing efficiency and cost savings
To maximize the benefits of predictive maintenance, organizations should adhere to several best practices that enhance efficiency and cost savings. First and foremost, it is essential to establish a solid data foundation. This includes investing in high-quality sensors and monitoring devices that can capture relevant data accurately. Companies must also ensure that data is collected consistently and stored in a centralized location for easy access and analysis. By prioritizing data quality, organizations can improve the accuracy of their predictive models and make more informed maintenance decisions.
Another best practice is to continuously refine predictive maintenance algorithms based on the data collected over time. Machine learning models should be regularly updated to ensure they reflect the most current equipment performance trends. This iterative approach enables organizations to enhance the accuracy of their predictions, allowing for timely maintenance that avoids costly failures. Additionally, companies should regularly review their maintenance strategies and KPIs to ensure they align with overall business objectives and adapt to changing operational conditions.
Collaboration across departments is also critical for the success of predictive maintenance initiatives. Maintenance teams, engineering departments, and data analysts should work together to ensure that insights gained from predictive analytics are effectively communicated and acted upon. Establishing cross-functional teams can facilitate knowledge sharing and foster a culture of continuous improvement. By involving all relevant stakeholders in the predictive maintenance process, organizations can maximize efficiency, minimize costs, and drive better outcomes across their operations.
Conclusion: Embracing the future of industrial equipment maintenance
As industries continue to evolve in response to technological advancements, embracing predictive maintenance represents a significant opportunity for organizations to enhance their operational efficiency and reduce costs. By leveraging data analytics and machine learning, companies can transition from traditional maintenance strategies to a more proactive and intelligent approach. The benefits of predictive maintenance, ranging from reduced downtime to improved safety, make it an essential component of modern industrial practices.
The successful implementation of predictive maintenance requires not only the right tools and technologies but also a commitment to continuous improvement and cross-departmental collaboration. Organizations that prioritize data quality, invest in employee training, and foster a culture of innovation will be best positioned to reap the rewards of predictive maintenance. As case studies have demonstrated, the potential for cost savings and improved productivity is substantial, making predictive maintenance a strategic imperative for businesses in various sectors.
Ultimately, the future of industrial equipment maintenance lies in the ability to harness the power of predictive maintenance. By understanding its importance, benefits, and best practices, companies can unlock new levels of efficiency and profitability. As we move forward, embracing predictive maintenance will not only enhance operational performance but also secure a competitive advantage in an increasingly data-driven industrial landscape.
Featured Product
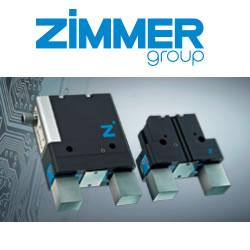