As President Trump's second term unfolds, the manufacturing landscape in the United States is poised for a significant transformation. The administration's renewed focus on reshoring manufacturing operations presents both opportunities and challenges for industry leaders.
The Reshoring Revolution: Navigating New Policies For A Manufacturing Renaissance

Dijam Panigrahi, Co-founder and COO | GridRaster Inc.
The Tariff Strategy: A Double-Edged Sword
President Trump's aggressive tariff policies, particularly on steel and aluminum imports, are reshaping the calculus for global manufacturers. By imposing a 25% tariff on steel imports and elevating aluminum tariffs to 25%, the administration aims to level the playing field for domestic producers1. This move has been met with mixed reactions from industry stakeholders.
On one hand, U.S. steel and aluminum producers have seen immediate benefits. The tariffs have allowed them to raise prices, invest in new production capabilities, and safeguard jobs in these critical sectors. The Steel Manufacturers Association and United Steelworkers have voiced strong support for these measures, citing the need to combat unfair trade practices and global overcapacity.
However, the ripple effects of these tariffs extend far beyond primary metal producers. Downstream manufacturers, particularly those in industries like automotive and construction, face increased input costs. This cost pressure can squeeze profit margins and potentially lead to job losses in sectors that employ far more workers than primary metal production.
The Reshoring Incentive Package
To counterbalance the potential negative impacts of tariffs and further incentivize domestic manufacturing, the Trump administration is proposing a comprehensive package of economic incentives.
These measures, combined with the tariff pressure, create a compelling case for both domestic and foreign manufacturers to establish or expand their U.S. operations. The lower corporate tax rate, in particular, could significantly enhance the competitiveness of U.S.-based manufacturing operations on the global stage.
Foreign Investment and Technological Adaptation
As foreign companies reassess their global manufacturing strategies, many are finding that producing in the U.S. can be more cost-effective than previously thought. Factors contributing to this shift include:
- Lower transportation costs for goods destined for the U.S. market.
- Cheaper energy prices in the United States.
- Various local and state-level incentives for new manufacturing facilities.
- Avoidance of tariffs on imported goods.
However, these foreign manufacturers face a significant challenge when entering the U.S. market: higher labor costs. To remain competitive, they are likely to invest heavily in advanced manufacturing technologies, including robotics, automation, and virtualized technologies such as augmented and virtual reality (AR/VR).
This trend is already evident in the U.S. robotics industry, which has experienced significant growth in recent years. Sectors such as automotive, aerospace, electrical and electronics, and metal and machinery are at the forefront of this technological adoption. The integration of these advanced technologies is expected to enhance productivity, improve product quality, and help address persistent labor shortages in the manufacturing sector.
Challenges and Considerations
While the reshoring trend presents significant opportunities, it also comes with challenges that industry leaders must navigate:
- Supply Chain Reconfiguration: Many manufacturers will need to identify new suppliers or develop domestic sourcing strategies to avoid tariffs on imported components. This process can be complex and time-consuming, potentially leading to short-term disruptions in production.
- Workforce Development: As manufacturing returns to the U.S., there is an increasing demand for skilled labor. Companies will need to invest in training programs and partnerships with educational institutions to develop a workforce capable of operating advanced manufacturing technologies.
- Initial Investment Costs: While automation and robotics can enhance long-term competitiveness, the initial investment required can be substantial. Manufacturers must carefully assess the return on investment and potential financing options.
- Balancing Automation and Employment: As companies invest in automation to offset higher labor costs, they must also consider the potential impact on employment. Finding the right balance between technological efficiency and job creation will be crucial for maintaining public and political support for reshoring initiatives.
- Global Market Access: While reshoring may improve competitiveness in the U.S. market, manufacturers must consider how it affects their ability to serve global markets. Retaliatory tariffs from other countries could impact export competitiveness.
Manufacturing industry leaders play a pivotal role in shaping America's industrial future. Their responsibilities encompass developing comprehensive strategies that account for policy changes, technological advancements, and global market dynamics, while continuing to invest in R&D and advanced manufacturing technologies. Fostering partnerships between industry, academia, and government is crucial for addressing workforce development challenges and driving innovation. Additionally, industry leaders must engage with policymakers to ensure that reshoring initiatives and related policies support long-term growth and competitiveness, ultimately steering the sector towards a more robust and resilient future.
Companies manufacturing in the U.S. should also continue to explore opportunities to leverage the highly skilled labor available in friendly partner nations like India. By tapping into India's vast pool of technical expertise, particularly in areas such as AI, quantum computing, and semiconductor technology, U.S. manufacturers can enhance their innovation capabilities and global competitiveness. Collaborative initiatives, such as the proposed U.S.-India AI and Deep Tech Public-Private Council, offer pathways for knowledge exchange and joint research and development.
Furthermore, streamlined visa processes and expanded work permits for critical skills could facilitate workforce mobility, allowing U.S. companies to benefit from India's talent in security-critical fields while fostering mutual growth and technological advancement.
A New Era of American Manufacturing
The reshoring trend, driven by new policies and global economic shifts, presents a unique opportunity to revitalize American manufacturing. By embracing advanced technologies and adapting to the new policy landscape, manufacturers can enhance their competitiveness and contribute to a robust domestic manufacturing base.
However, success in this new era will require careful navigation of the challenges ahead. Industry leaders must balance the benefits of automation with workforce considerations, manage complex supply chain transitions, and continue to innovate in the face of global competition.
Dijam Panigrahi is Co-founder and COO of GridRaster Inc., a leading provider of cloud-based platforms that power compelling high-quality digital twin experiences on mobile devices for enterprises. For more information, please visit www.gridraster.com.
The content & opinions in this article are the author’s and do not necessarily represent the views of RoboticsTomorrow
Comments (0)
This post does not have any comments. Be the first to leave a comment below.
Featured Product
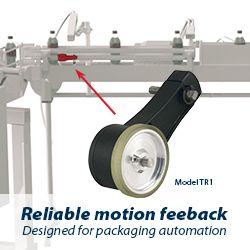