KUKA to Showcase Production Lifecyle Digitalization and Feature Robot Versatility at Automate 2025
The company will also highlight the versatility of its robot automation portfolio with bin-picking, palletizing, welding, and Autonomous Mobile Robot (AMR) demonstrations. Visitors to booth #4032 looking to automate their operations will experience these KUKA production-enhancing solutions.
SHELBY TOWNSHIP, Mich., April 3, 2025 - KUKA Robotics will showcase KUKA Digital, the company's digital business segment that drives seamless digitalization of the entire production lifecycle for improved efficiency and performance at Automate 2025, May 12-15 at Huntington Place in Detroit, Michigan. The company will also highlight the versatility of its robot automation portfolio with bin-picking, palletizing, welding, and Autonomous Mobile Robot (AMR) demonstrations. Visitors to booth #4032 looking to automate their operations will experience these KUKA production-enhancing solutions.
Visitors to KUKA's booth will experience KUKA Digital, the company's software and digital business segment that provides end-to-end digitalization of a wide range of production machines and systems for higher productivity, sustainability and resiliency. With digitalization and artificial intelligence (AI), manufacturers can digitally design their factory layout on the cloud-based platform ‘mosaixx' and simulate factory operations offline with Visual Components. KUKA.Sim and the AI-based Microsoft KRL Copilot provide robotic simulation and programming, and robot networking can be accomplished with KUKA.iiQoT for a completely data-driven factory. KUKA Digital effectively combines KUKA's manufacturing heritage with its digital business capabilities for seamless digitalization of the entire production lifecycle from factory layout to final production.
For robotic bin picking, KUKA's booth will feature a KR CYBERTECH-2 robot using a Photoneo vision system with a PhoXi 3D scanner. The KR CYBERTECH-2 series offers high-performance industrial robots designed for handling, assembly, and machining applications with exceptional speed, precision, and flexibility. Featuring compact designs and high payload capacities, these robots are optimized for space-saving operation in various manufacturing environments.
Using Photoneo's Bin Picking Studio software, the KR CYBERTECH-2 will pick partially machined spur gear parts from a randomly assorted bin and place them onto portable part trays. A KR AGILUS-2 machine-tending robot from KUKA will pick the parts from the part trays for simulated processing through a SYIL X7 3-axis vertical milling machine equipped with a SIEMENS SINUMERIK 828D controller and 15" touch panel. After the parts are processed through the CNC mill, an OGP SmartScope SP 332 measurement system will inspect them. The operation uses a PartNR cell designed by System Partner Waybo that is compact and enables high-mix, low volume production. SCHUNK brand tooling, controlled by FESTO brand valves, is utilized on the robot cells for the part gripping operations.
Managed by KUKA's AMR.Fleet software, two KMP 1500P mobile units from KUKA traveling between the part station and machine tending station will handle trays and part totes. The tray-handling KMP 1500P uses an integrated elevating module for unloading and loading trays at both robot cells. The tote-handling KMP 1500P incorporates a conveyor module for unloading and loading of totes at both robot cells and at the tote staging area.
KMP 1500Ps are differential driven, mobile platforms that navigate autonomously and eliminate the need for predefined routes and rigid processes. KUKA's diffDrive technology enables precise and highly maneuverable movement by independently controlling the speed of two or more wheels on either side of the robot. By varying the relative speed of these wheels, the robot can move forward, backward, turn in place, or navigate complex environments with smooth and efficient motion. This drive system enhances agility, making KUKA mobile platforms well-suited for dynamic industrial applications such as autonomous material transport and flexible manufacturing. Banner brand sensors, IO-Link and wireless communication technology is used throughout the cell for discrete control and monitoring of a variety of the system functions.
In an interactive demonstration, KUKA will showcase a KR CYBERTECH-2 integrated into System Partner SISU Industrial Robotics' Cinema Robotics motion control system that allows cinematographers to easily program and achieve precise, complex and repeatable camera movements. The CYBERTECH's optimized controller structures provide cinematographers the smooth, sensitive motion characteristics needed to produce crystal clear shots. SISU's Battery Box will power the system, allowing studios to run any SISU robot system off standard wall power with the added capacity of providing eight hours of unplugged, uninterrupted power.
For shops seeking robotic welding, a KR CYBERTECH nano ARC from KUKA will demonstrate electroslag welding. The KR CYBERTECH nano ARC is especially well suited for simple arc welding and is available with reaches ranging from 1,441 mm and 1,843mm to 2010mm. It features a hollow wrist with bearings on both sides and a repeatability of 0.04 mm. At Automate, the robot will be equipped with a KUKA DKP two-axis positioner. The positioner provides one rotational axis, one tilting axis and a 500-kg payload capacity for flexible workpiece machining. With a duty cycle of 100%, the DKP positioner ensures welding power of up to 500 amps. System Partner and automated systems integrator ARC Specialties designed the electroslag demonstration, which is a joining process using an electric arc to create a molten slag for the joining of thick workpieces.
Two Automate demonstrations will highlight KUKA's capabilities within the palletizing and consumer goods arena. The first will feature a KR QUANTEC-2 high payload robot simulating the manufacture and refurbishment of wooden pallets. The KR QUANTEC-2 family is available in payloads from 120kg to 300kg and reaches of 2700mm to 3900mm. The KR QUANTEC-2 family is the first industrial robot series with digital motion modes. These software add-ons allow manufacturers to select the optimal robot motion for their specific applications. "Path mode" allows greater accuracy and precision while "dynamic mode" increases speed and reduces cycle times. The KR QUANTEC-2 family is also offered in variants where special certifications and product classifications are required such as Hygienic Oil (HO) or Foundry (F).
In the cell, the robotic system will pick up a pallet, scan it, and assess its quality based on customer-defined criteria before directing it to the appropriate stack. Technology partner IVISYS' PALLETAI pallet inspection solution will scan pallets and generate real-time data, assessing compliance with user-defined quality standards. High-resolution images will feed through AI neural networks and transfer to the IVISYS cloud for immediate analysis.
KUKA's second palletizing demonstration will feature the Modular Palletizing System (MPS), designed by System Partner ABCO Automation. The MPS cell showcases a highly adaptable palletizing system equipped with a KR IONTEC robot and KMP 600P mobile platform, both from KUKA, for autonomous material handling. Capable of mounting in virtually any position, the six-axis robot family is offered in variants with payloads from 20-70 kg and reach of 2100-3100mm and with a repeatability of 0.05 mm. The KMP 600P is KUKA's most compact high-performance AMR, ideal for confined production spaces, offering a 600-kg payload for efficient material transport, process linking, and reliable point-to-point delivery. The system utilizes KUKA.PalletTech palletizing software, providing a versatile and user-friendly solution for configuring and executing palletizing tasks across various packaging types, packing patterns, and stations. KUKA.PalletTech enables rapid deployment of complete palletizing applications without requiring extensive programming knowledge, while also offering customization options to meet the specific demands of existing production lines.
As with all the company's automation solutions, those shown at Automate 2025 are backed by KUKA's expert service and support for training, complete system engineering and simulation, readily available spare parts, robot refurbishment and more. All these features are easily accessible through the my.KUKA.com site, and KUKA maintains corporate offices and production operations, along with integration partner facilities, conveniently located throughout North America to provide responsive customer service and support.
KUKA
KUKA is a global automation corporation with sales of around 3.3 billion euro and roughly 14,000 employees. The company is headquartered in Augsburg, Germany. As one of the world's leading suppliers of intelligent automation solutions, KUKA offers customers everything they need from a single source: from robots and cells to fully automated systems and their networking in markets such as automotive, electronics, metal & plastic, consumer goods, e-commerce/retail and healthcare.
Featured Product
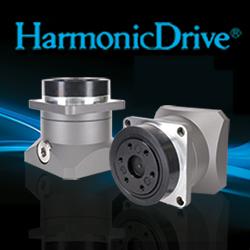