Precise Automation introduces PreciseFlex Sample Handler 4-axis robot
Precise Automation introduced the PreciseFlex (PF) Sample Handler. It features a four-axis SCARA configuration with a servo gripper and is ideal for automating Life Science benchtop processes where price, ease-of-use, space requirements and safety are critical. Typical applications include handling, loading and managing plates, test tubes and microscope slides.
Precise Automation introduced the PreciseFlex (PF) Sample Handler. It features a four-axis SCARA configuration with a servo gripper and is ideal for automating Life Science benchtop processes where price, ease-of-use, space requirements and safety are critical. Typical applications include handling, loading and managing plates, test tubes and microscope slides.
This low-cost, quiet OEM mechanism has its motion controller, harnesses and power supplies embedded within its structure to eliminate extra enclosures and simplify installation. This space saving design, combined with a unique geometry, allows the PF to service many stations in an extremely small workcell. This new product also includes safety features that disable motor power when a minimal, unexpected force is encountered, thus allowing the PF to operate without safety shields in benchtop applications. Combined with absolute encoder motors, which do not require any motion to home during start-up, these safety features greatly reduce the risk of injuring people or damaging equipment during operation.
It has an embedded Vision-Guided Motion Controller. This controller offers unique free mode teaching aids and excellent capabilities for automatically generating elegant and reliable motion sequences. Its features permit the mechanism's gripper to move along smooth, straight line paths or arbitrarily complex motion sequences by simply moving the sample handler by hand to start and end positions and letting the controller handle the rest. Combined with a simple, yet powerful programming language, Ethernet interface (featuring PC control via an open source TCP/IP Command Server), kinematics for Cartesian motions and quiet, high performance servo motors, the PF simplifies programming and reduces cycle times with the most efficient motions possible.
Featured Product
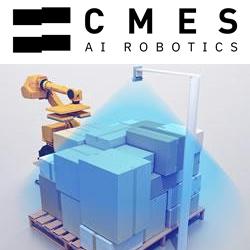