Diakont Awarded for Nuclear Industry Innovation for Robotic Buried Pipe Inspection
Diakont received an innovation award for robotic buried pipe inspection during this years Nuclear Energy Assembly, hosted by the Nuclear Energy Institute in Atlanta, Georgia. The Nuclear Energy Institute is the nuclear energy industrys policy organization.
Diakont received an innovation award for robotic buried pipe inspection during this years Nuclear Energy Assembly, hosted by the Nuclear Energy Institute in Atlanta, Georgia. The Nuclear Energy Institute is the nuclear energy industrys policy organization.
As part of the Top Innovative Practice (TIP) Awards, the innovation award was granted to the team for Volumetric Inspections of Inaccessible Piping via Robotic Crawler. The Diakont team tasked with inspecting auxiliary service water (ASW) piping applied an innovative approach to determine the health of certain sections of buried piping. The approach used a robotic crawler to conduct ultrasonic examination inside critical, but uniquely configured, sections of the pipe. These line segments are a pipe-in-pipe configuration. Because these ASW line portions are sleeved, conventional excavation and ultrasonic testing cannot be completed to assure wall thickness meets minimum ASME Code compliance. By using the robotic crawler, the inspection of the ASW piping sections eliminated any human occupancy of the piping while yielding a complete volumetric examination; its use also reduced a cost of up to $3 million, including excavation, to less than $200,000.
"Diakonts innovative buried pipeline inspection service provided real integrity data on 300 of coated auxiliary service water lines without having to put personnel in confined spaces" Jonny Minder, director of energy services at Diakont, "increasing plant safety and efficiency is Diakonts primary goal."
"Innovations like the ones celebrated today help ensure nuclear power plants continue to run safely and stay competitive in todays marketplace," Sue Perkins-Grew, senior director of nuclear security and incident response, said at the TIP awards ceremony.
The TIP awards celebrate industry leaders for new practices, enhanced processes, and improved technology. To be considered for an award, the process or practice must be implemented and address one or more of the following criteria: innovations, safety, cost-savings impact, productivity/efficiency, transferability, communications, or vision and leadership.
Diakont was one of 12 awardees recognized at the awards luncheon in Atlanta. The award-winning team includes Exelon Corporation, Tennessee Valley Authority, Exelon Nuclear, North American Young Generation in Nuclear, and more.
Diakont was also nominated for a TIP award for innovative robotic underwater decontamination service provide during Spring 2017 outage. Diakont developed a hybrid ROV-crawler tool with a built-in brush assembly that swam throughout the plants refueling cavity and adhered to floors and walls to decontaminate the surfaces. The cutting-edge method was so effective that no additional manual cavity decontamination was required after drain down. Preliminary surveys indicated that all contamination levels were reduced to <50K dpm/100 cm2, helping the utility meet their INPO/Industry collective radiation exposure goals
About Diakont
Diakont is a leading designer, manufacturer and provider of high-technology products and services for the nuclear power industry, providing radiation-tolerant cameras and robotics, as well as inspection, maintenance and repair services for plants of all designs. With a mission of enhancing safety while improving the overall efficiency of the nuclear industry, Diakont has been deploying state-of-the-art robotics and world-class service to solve inspection and repair challenges for over 25 years.
Featured Product
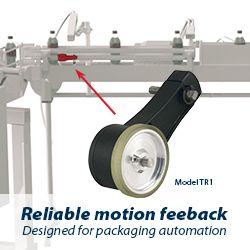
Model TR1 Tru-Trac
The Model TR1 Tru-Trac® linear measurement solution is a versatile option for tracking velocity, position, or distance over a wide variety of surfaces. An integrated encoder, measuring wheel, and spring-loaded torsion arm in one, compact unit, the Model TR1 is easy to install. The spring-loaded torsion arm offers adjustable torsion load, allowing the Model TR1 to be mounted in almost any orientation - even upside-down. The threaded shaft on the pivot axis is field reversible, providing mounting access from either side. With operating speeds up to 3000 feet per minute, a wide variety of configuration options - including multiple wheel material options - and a housing made from a durable, conductive composite material that minimizes static buildup, the Model TR1 Tru-Trac® is the ideal solution for countless applications.