UltraFlex using induction heaters to preheat Inconel for the aerospace industry
] In a recent test application UltraFlex Power Technologies proved the efficiency of using induction heaters in the manufacturing process for aerospace components.
In a recent test application UltraFlex Power Technologies proved the efficiency of using induction heaters in the manufacturing process for aerospace components. UltraFlex is a leading induction heating manufacturer and frequently performs complimentary testing with provided materials from current and potential customers.
The recent test scenario had been set up per request of an UltraFlex customer - a research facility working with a manufacturer of components for the aerospace industry to provide an efficient solution for abrasive testing of materials at high temperatures and rotation speed.
An Inconel blade and an UltraFlex 15 kW induction heater from the UltraHeat W series had been used for this induction heating scenario requiring heating at a target temperature of 1832°F (1000°C)! UltraHeat W are advanced, cost-effective 5 kW to 15 kW Induction Heating systems utilizing the latest switching power supply technology. They feature adaptive digital phase control providing very efficient operation in a wide frequency range. To ensure efficient heating, UltraFlex also designed a custom, C-shaped induction coil with a "channel" profile for the blade and clearance of ~2mm (0.07 inch) between the coil and the blade.
UltraFlex engineers managed to achieve a complete custom solution that concentrated the electromagnetic field and successfully heated the edge of the blade to 1000°C (1832°F) while the blade was rotating at high RPM. The material passed this heating test successfully, using a precise heating process that had been energy-, time- and cost-efficient. In addition to being resource-efficient, this had also been a completely green process - due to the lack of open flame, there was no smoke or noxious emissions. Last but not least, in this process the operator skills had been removed from the equation completely, which would ensure consistent heating and hence, reliable induction heating results every time.
Find out more at:
https://ultraflexpower.com/
Contact us at:
+1.631.467.6814
uptnews@ultraflexpower.com
About UltraFlex Power Technologies:
UltraFlex Power Technologies (ultraflexpower.com) offers the most advanced and innovative digitally controlled induction heating equipment in the industry. Its compact modular and flexible systems are suitable for a wide variety of induction heating, casting and melting applications.
Featured Product
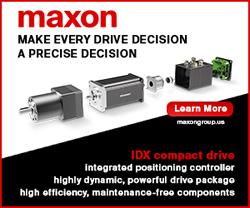
The maxon IDX Compact Drive with Integrated Positioning Controller
The compact brushless EC-i motor combined with an EPOS4 positioning controller delivers a highly dynamic, powerful drive package with field-oriented control (FOC), high efficiency, and maintenance-free components in a high-quality industrial housing. The maxon IDX drives are suitable for use across the entire speed range (from standstill to maximum speed) and have an extremely high overload capability. Together with a positioning controller, the integrated sensor (single turn) enables absolute positioning.