Material handling and the inhouse transportation is often still done manually by humans spending valuable time just pushing carts from A to B. With collaborative mobile robots these tasks can be automated in a simple, efficient, and cost-effective way.
Five Collaborative Mobile Robots Applications
Contributed by | MiR
Using collaborative mobile robots is still a relatively new way of handling internal transportation tasks, and “what can I do with this robot” is a question we often get when meeting customers or doing demos. Many companies are very open towards automation and robotics in general but they are usually focusing on automating production. Material handling and the inhouse transportation is often still done manually by humans spending valuable time just pushing carts from A to B. With collaborative mobile robots these tasks can be automated in a simple, efficient, and cost-effective way.
The mobile robots from Mobile Industrial Robots have an open interface, meaning that they can be mounted with customized top modules whatever the customer application demands. We have listed five common applications of mobile robots:
Shelf Units: The shelf units are often used to transport semi-finished or finished goods between productions, between production and warehouse and/or in warehouse logistics. Shelf modules are often used in semi-automated installations, where an employee summons the mobile robot via the robot’s interface, or an installed button, fills up the robot with the goods and send it on its way with just one click on a button.
The shelf units can also be used with a shelf lift module, so the robot can pick up and unload entire shelves with wheels.
Conveyor band/belts: The mobile robots can be deployed with a conveyor top module, so they can transport items between fixed conveyor band/belts. These are often seen in fully automated solutions where the mobile robots move items between production lines or from production line to delivery. The mobile robots are the adaptable link between the traditional conveyor bands and enable companies to be more efficient because they can transport items flexibly between several production lines.
Automated Pallet Fork: Within logistics, a solution we often see mobile robots towing a pallet with a pallet fork. The mobile robot can locate the pallet fork and transport it to it's destination autonomously. In this way the employees only have to load and unload the pallet from the pallet fork and they save valuable time, because they do not need to do the transportation themselves.
Robotic Arm: The mobile robots add mobility to the robotic arms, and are used in productions and in warehouse logistics where the process of repeatedly picking products from warehouse shelves and carrying them back and forth location points can be automated. It is also relevant for retail warehouses where the robots can pick up orders from different locations and deliver them at a shipping area. These are monotonous tasks that robots can perform, and it frees up the staff for more valuable tasks. Both the mobile robots and the robotic arms are collaborative and can work alongside humans without any extra safety.
Safety units: The safety units are mostly used in hospital where they transport medicine that needs to be locked in, autonomously. Hospitals are usually large facilities and therefore, the mobile safety units save employees from walking long distances with the medicine. Being able to open communicate with doors and elevators the mobile robots can transport items over long distances with no need for human interference. The safety units can also be used for transporting other confidential items in other industries.
The content & opinions in this article are the author’s and do not necessarily represent the views of RoboticsTomorrow
Comments (0)
This post does not have any comments. Be the first to leave a comment below.
Featured Product
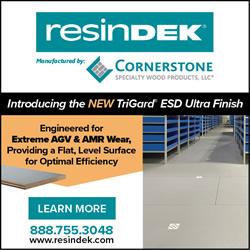