The success of machine vision in industrial manufacturing is due to the fact that it provides faster, more accurate and more cost-effective QA than manual visual inspection.
Responding to the Market Need for Quality
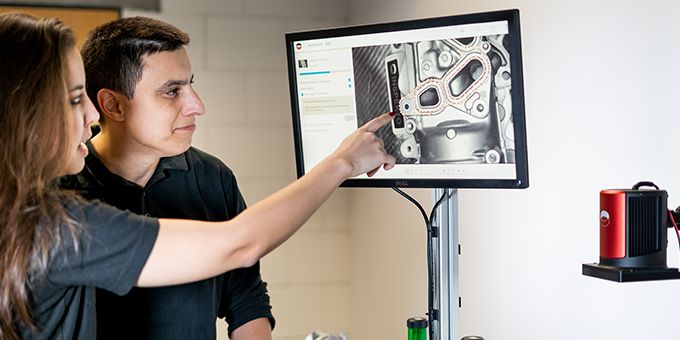
Yonatan Hyatt, CTO and Co-Founder | Inspekto
The current situation means that manufacturers in all industry sectors are modifying their manufacturing processes. Here Yonatan Hyatt, CTO and co-founder of Inspekto, the company that developed Autonomous Machine Vision (AMV), explains how this technology is pushing the boundaries of artificial intelligence (AI) to respond to market needs.
The success of machine vision in industrial manufacturing is due to the fact that it provides faster, more accurate and more cost-effective QA than manual visual inspection. However, traditional machine vision solutions also come with numerous disadvantages, such as cost, complexity and long periods of downtime for installation and training.
Autonomous Machine Vision (AMV)
To overcome these challenges, Inspekto developed Autonomous Machine Vision (AMV), a new category of machine vision for quality inspection.
Autonomous Machine Vision is a hybrid technology that merges computer vision, deep learning and real-time software optimization technologies. Unlike traditional machine vision projects, systems in the AMV category are plug & play, self-contained products that any user can simply install on the production line without relying on a machine vision expert.
During set up, the user simply switches on the controller and ensures that the field of view (FOV) covers the location to be inspected. The user then places a good sample item in the FOV and uses a mouse to mark a region of interest for the system to detect defects in.
Unlike traditional QA solutions, which require hundreds or even thousands of good and defective sample products to be trained, Autonomous Machine Vision systems only require an average of 20 to 30 good samples, and no defective ones.
Autonomous Machine Vision flips the parameters of traditional QA. Instead of memorising what a defective item looks like, systems learn — much like a human being would — what a good one is supposed to look like.
Once in operation, an AMV system compares each image with the ones memorised during set up, verifying both the shape tolerances and surface variations to identify any defects. The system will then communicate the location of a defect to a human operator or to a programmable logic controller (PLC).
The image acquisition process
The autonomy in Autonomous Machine Vision is the result of several AI engines working in tandem. The algorithms developed by Inspekto make AMV systems self-setting, self-learning and self-adjusting.
A Video-Sensor-Optimisation AI engine automatically adjusts the illumination and camera parameters to the product being inspected and the environmental conditions, so the system can obtain the best possible image, with perfect focus, depth-of-field, exposure level and dynamic-range settings.
A Detection-and-Alignment AI engine automatically locates products in the 3D space. This means that the system will recognise products even if they appear in a different location or orientation then the ones it memorised.
While in operation, AMV systems keep learning — if a system flags an abnormality that the manufacturer deems as non-defective, the system will learn and not flag the same defect again in the future.
Maximum flexibility
Systems in the AMV category are not product-specific and can be used to inspect items produced in every industry, with any handling method.
AMV systems can communicate with the manufacturer’s PLCs via all common industrial protocols including PROFINET, Ethercat and Modbus and can be installed in every position along a Bosch profile, present in most manufacturing lines.
Leading manufacturers like Bosch, Pepsico, BSH, Mahle, Geberit, and Dailer are already using Autonomous Machine Vision, and Inspekto’s products now have a global footprint. In the post pandemic scene, more manufacturers across the world may choose to join these global players in embracing Autonomous Machine Vision.
The content & opinions in this article are the author’s and do not necessarily represent the views of RoboticsTomorrow
Comments (0)
This post does not have any comments. Be the first to leave a comment below.
Featured Product
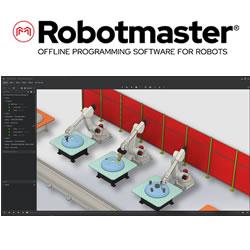