As automation becomes more pervasive in manufacturing, Flex's François Barbier discusses the positive impact robots and other advanced technology solutions have on their human counterparts.
Better Together: the Human and Robot Relationship
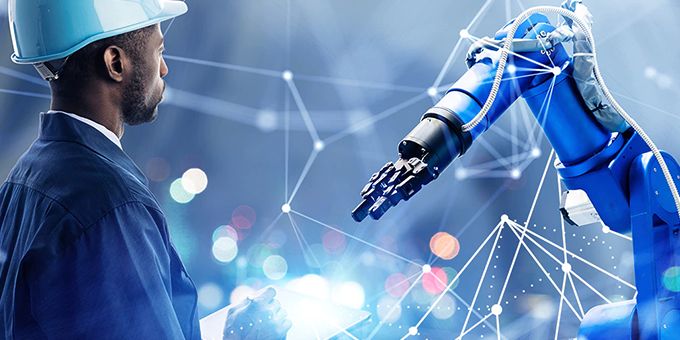
François Barbier | Flex
Science fiction and mass media have done the automation industry a disservice. Today, the mere mention of robots can drum up ideas of all-knowing "beings" capable of replacing human workers in every facet of their job. Admittedly, this type of futuristic thinking can even seep into our industry, with manufacturing organizations pushing the idea of lights out factories. These idealistic environments are entirely automated and seamlessly pump out new products without human intervention.
The problem? Automation doesn't work without human workers. In fact, Elon Musk famously commented on this nearly three years ago, stating "excessive automation at Tesla was a mistake. To be precise, my mistake. Humans are underrated."
And while much of the industry today still thinks mobile robots, cobots, guided vehicles, and other automation technology will replace human workers, we find this thinking backwards. At Flex, we see our employees as the key to deploying automation. We strive to use the most advanced manufacturing technologies to help open new opportunities, drive efficiencies and quality, and keep our people safe.
How automation improves the working experience
When deployed thoughtfully and with the intention to simplify repetitive or difficult to manage processes, automation can make jobs more enjoyable, remove risks and even create opportunities for career advancement:
- More enjoyable work: Robotic solutions are designed to automate routine, repetitive, and sometimes dirty jobs. On the manufacturing floor, that can include line-side replenishment, staging, assembling minuscule parts, and many other tasks. By eliminating these tasks, humans can turn their attention to other work, such as exception handling and creative problem-solving.
And automation doesn't just have a home on the shop floor. Solutions like robotics process automation (RPA) can help office workers with manual data entry. In fact, we've deployed RPA to help our accounts team automate more than 700,000 transactions changes a year, enabling them to focus on more innovative process improvement roles.
-Improved safety: Beyond removing workers from repetitive, and potentially dangerous settings, automation can also help reduce other risks commonly found on the factory floor. These risks can span injuries from lifting heavy items to accidents caused by distracted or disengaged workers. Recent advancements in sensors have enabled robots to react to their human counterparts, shut down, and avoid contact before an accident occurs. During the Covid-19 pandemic, automation even played a critical role in helping spread out the factory floor to maintain social distancing guidelines.
-Career development: The constant evolution of technology drives the need for employees to evolve by upskilling, which creates new job opportunities and fosters personal professional growth.
However, the upskilling journey must be well thought out. At Flex, we've put a keen focus on providing on-the-job training in conjunction with the rollout of automation solutions. This helps engage employees from the start and allows them to be part of our complete advanced manufacturing journey. Fostering system thinking becomes critical as future changes to workflows or automation can affect the entire manufacturing process.
With new automation deployments comes new careers. In fact, we've seen employees progress from working on the line to managing fleets of robots to becoming equipment engineers. Instead of replacing jobs, automation can help create new roles we previously never imagined, leading to further career growth and more opportunities.
The human element in automation
It's apparent automation can drive efficiencies, increase productivity, improve product quality and even reduce risks. However, it's not the end-all solution. Automation is a powerful technology, but it’s often only programmed to focus on a specific set of tasks. While artificial intelligence and machine learning have helped these solutions "learn" on the job, it pales compared to the level of flexibility and exception handling a human can provide.
That's why the combination of humans and robots is better together. It enables both parties to perform tasks they're best suited to perform. And it’s the reason why many of our lines today are joint efforts between human and machine.
The fascinating part is that you don't have to only take my word for it. Advanced manufacturing technologies, like simulation, can provide 3D models that highlight the ways humans and robots interact, what the future workplace could look like, and tap the know-how of human workers on how processes can be performed more efficiently together. A robot can never replace the years of experience and critical thinking of an employee.
In future posts, my colleagues and I will continue to explore the role automation and advanced technology plays in manufacturing and the impact on human workers.
For more blogs on manufacturing from Flex, you can visit:
https://flex.com/company/leadership-insights.
The content & opinions in this article are the author’s and do not necessarily represent the views of RoboticsTomorrow
Comments (0)
This post does not have any comments. Be the first to leave a comment below.
Featured Product
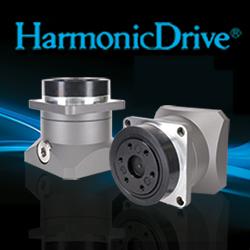