Compared to conventional lift trucks, LGVs provide more consistent throughput of pallets between manufacturing and distribution functions, less damage to racking, raw materials and merchandise, reduced labor requirements, and lower cost of operation.
Laser-Guided Vehicles: Supporting Sustainability in Manufacturing and Distribution
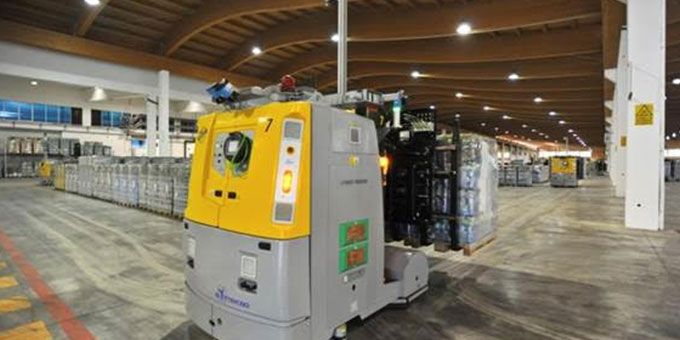
Jim McMahon for | E80 Inc
Technology advances in automated manufacturing and distribution have enabled a more integrated approach for the operation of material handling systems, which, in turn, has provided significant advantages for increased throughput, system uptime and a better ROI. Along with this technological evolution, an accelerated capability for streamlined energy management, energy efficiency and sustainability has also become possible, allowing ambient-temperature, deep-freeze and chilled distribution facilities to better manage their power draw, energy utilization, systems integration and overall operational costs.
In recent years, a number of material handling manufacturers have literally gone back to the drawing board and reengineered many of their material handling systems from the ground up to improve energy efficiency and sustainability, while maintaining these systems' load-carrying capability. One of these systems is laser-guided vehicles (LGVs), which, at least one manufacturer has significantly improved the performance of lithium batteries to keep its LGVs operating on the floor longer, even in challenging deep-freeze temperatures, while increasing battery life, and reducing battery recharging time and energy draw. These LGVs, operating with highly-sophisticated real-time controls, have enabled their integration with plant-wide packaging, storage and distribution functions, effectively optimizing plant footprint and throughput, thereby enhancing sustainability initiatives.
Laser-Guided Vehicles
Laser-guided vehicles enable significant efficiencies to manufacturing and distribution. They improve production flow by bringing material to the operators, thereby cutting cycle times, and eliminating wait, walk and search time. They reduce work-in-progress inventory. They cut labor costs by eliminating simple jobs related to material and movement, and permit reassignment of those workers to areas where they can add more value to the facility. LGVs virtually eliminate product damage with gentle handling of loads, and provide flexibility of process flow and throughput, as needs change.
LGVs are designed to handle various pallet types, with loads up to 3,400 lbs. (Image courtesy E80)
LGVs provide for movement of pallets between integrated functions in manufacturing and distribution. Interfacing with multiple systems, LGVs enable reliable raw material and product handling, with near zero potential for product damage. Utilizing a combination of logic software and wireless navigation, LGVs can perform tasks that are not possible with other transport systems – such as the uniform movement and positioning of pallet loads to within a fraction of an inch of their designated targets, without noise, and with a high degree of safety for workers and their operational environment.
Latest Evolution of LGVs
The most recent automation developments in laser-guided vehicles for pallet movement enable warehouse operators and plant production supervisors to optimize for system flexibility, modularity and scalability.
Many types of LGVs exist for use in different industries, but for a large number of applications in manufacturing and distribution, LGVs are utilized for pallet movement. Four types of LGVs are commonly employed: 1) Fork AGVs; 2) Lift-deck/unit-load AGVs; 3) Conveyor-deck AGVs; and 4) Tugger AGVs.
Designed to handle various pallet types – such as CHEP, EURO, Blockpallet and Stringer, with load requirements up to 3,400 pounds, these LGVs are able to accommodate single-deep and double-deep racking with a telescope fork. Using a satellite remote unit, lane depth can be considerably extended.
LGVs accommodate single- and double-deep racking, and extended depths with satellite remote units. (Image courtesy E80)
Transporting heavy pallet loads, however, imparts huge forces upon these vehicles, resulting in significant maintenance and power requirements to keep LGV fleets functioning. The latest generation of LGVs, however, incorporates design, navigation, sensor, power and controls improvements that significantly streamline their prior operational performance.
An increasing number of supply chain manufacturers require 24-hour operation at maximum throughput in lights-out facilities. Today's latest generation of LGVs have been designed to efficiently meet and exceed these requirements.
An excellent example of this new evolution of laser-guided vehicles is E80's latest LGVs designed for pallet movement. E80 – a multinational leader specialized in creating automated solutions for companies that produce fast-moving consumer goods, particularly in the food, beverage and tissue sectors – has been a leading manufacturer of LGVs for almost three decades. Some of the company's latest technology advances have made LGVs particularly attractive for sustainability, and particularly with reduced energy consumption through enhanced lithium flash-battery technology and wireless induction charging.
Lithium Flash Battery® Technology
A key factor in LGV operation is battery performance, which directly influences energy usage. Some of the latest technology advances in lithium-ion chemistries have made LGVs particularly attractive with reduced energy consumption. One of these is lithium Flash-Battery® technology.
Introduced for use with LGVs by E80, lithium Flash Battery technology, developed by Flash Battery Srl, provides a higher level of performance than other batteries for industrial vehicles. Flash Battery technology uses the safest and most stable chemistry available, lithium iron phosphate (LiFePO4), which is cobalt-free (material with high environmental impact) and delivers well-defined performance and long-term stability. Having a very constant discharge voltage, Flash Battery technology allows the LGV to maintain the same performance at every state of charge.
The cells in a lithium battery are not all the same and have small differences in capacity, internal resistance and self-discharge. These differences lead to an imbalance among them. The response of conventional systems is to perform long balancing charges several times a week, which translate into dozens of hours a week of LGV downtime at charging stations. To avoid these problems and keep efficiency high, Flash Battery electronics employs a patented high-power balancing system, with active and passive mode, 20 times faster than conventional balancing. This allows the cells to be equalized in just a few tens of minutes once every 2-3 weeks. Only one lithium Flash Battery is required for each LGV, with an expected lifetime ranging from 6 to 10 years depending on the consumption of the specific plant.
Supporting the performance of LGVs using Flash Battery technology, E80's Flash Data Center daily monitors and controls every battery of the fleet integrated system to ensure the LGV network maintains its battery potential in peak performance to maintain plant uptime and efficiency.
Lithium Flash Battery technology, a better solution for LGV operation. (Image courtesy E80)
Reduced Energy Usage
The importance of reducing energy consumption and better management of energy utilization becomes a more critical issue as energy costs escalate, and manufacturing and logistics operations are pressured to lower operating costs without loss of productivity. This is driving the evolution of more energy-efficient material handling systems, along with the analytic tools and controls to optimize their operation.
LGVs with lithium flash-battery technology, combined with wireless induction charging, can deliver a considerable reduction in energy usage, when compared to LGVs using lead acid batteries.
Compared to pallet conveyors which require considerable energy to power their motors, the power requirements for LGVs using flash-battery technology are up to 30 percent less to move the same load weight over the same distance in a manufacturing or distribution facility.
Integrated-Plant Supports Sustainability
The smooth functioning of LGVs is dependent on their controls system, which has the task of coordinating the orders received from the plant's process system or warehouse management system, or ERP, then directing the work for the automated guided vehicles.
But the latest-generation of LGV control systems can do much more. For example, Smart Integrated Logistics (SM.I.LE80®) from E80, ensures the integrated and automated management of systems and flows, communicating with production lines, palletizers and wrappers, as well as coordinating the movement of pallets in the warehouse, through to shipping. The entire logistics flow of the manufacturing and distribution environment can be centrally managed from an integrated-logistics software platform that ensures the efficient integration and optimization of all operations. Such a controls system also guarantees total product traceability and safety throughout the facility's supply chain.
Optimizing LGVs for energy efficiency. (Image courtesy E80)
These controls optimize for system flexibility, modularity and scalability. The net result is better utilization of the facility's footprint. Off-site storage, so common in manufacturing, can now be consolidated back into the main plant, reducing vehicle travel and energy needed to power the off-site locations, particularly so in chilled and deep-freeze storage. This supports sustainability.
Control systems like SM.I.LE80 also enhance predictive maintenance and cloud-based condition-based maintenance by providing better visibility to the operating state of every machine within the integrated environment, in real time. This not only means improved system uptime, but supports sustainability. More efficiently operating machines make better use of energy consumption, and reduce leakages of lubricants and other chemicals into the environment, particularly so with rotating equipment which is so prevalent is manufacturing and distribution facilities.
These latest high-performance LGVs for pallet movement, and their controls systems, pack extreme improvements in battery performance, energy utilization and vehicle uptime. These factors make LGVs serious systems in any manufacturing or distribution facility seeking to upgrade its sustainability initiatives.
About E80 S.P.A.
The tailor-made automated solutions developed by E80 Group ensure a significant gain in factory and DC efficiency. Starting from in-depth analysis of customers’ business needs through proprietary simulation software providing 95 percent accuracy, E80’s innovative technologies automate all material flow movements from inbound of packaging material all the way to automated trailer loading of finished goods.
The content & opinions in this article are the author’s and do not necessarily represent the views of RoboticsTomorrow
Comments (0)
This post does not have any comments. Be the first to leave a comment below.
Featured Product
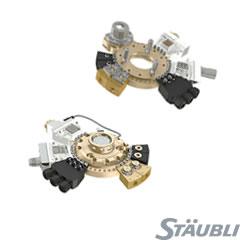