Central to the functionality of AR devices are the optical components, which must meet stringent requirements to ensure clear, undistorted images and seamless digital overlays onto real-world environments
The Role of Micro Molding in the Making of Optics for Augmented Reality Applications
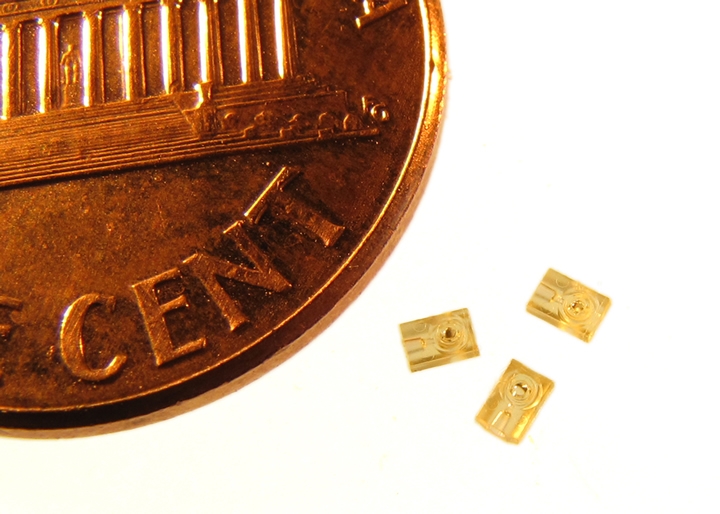
Brett Saddoris, Technical Marketing Manager, | Accumold
Augmented reality (AR) is rapidly advancing across industries, from consumer electronics and entertainment to healthcare and industrial sectors. Central to the functionality of AR devices are the optical components, which must meet stringent requirements to ensure clear, undistorted images and seamless digital overlays onto real-world environments. The production of these micro-optical parts has pushed the boundaries of precision manufacturing, with micro molding emerging as a key technology in meeting these demands.
Optical Requirements of Augmented Reality
Optics used in AR devices, such as tiny lenses, light guides, and diffractive optical elements (DOEs), must adhere to extremely tight tolerances to ensure high image clarity and precise alignment. Given the short optical paths in AR systems, even the slightest deviation in the position or shape of these components can lead to significant image distortions or misalignment. This is particularly crucial in devices like AR smart glasses, where the augmented image must perfectly overlay the user’s view of the physical world.
Micro molding addresses this challenge by offering a level of precision that meets the demanding positional and surface finish requirements of AR optics. The components can be manufactured with micron-level accuracy, which ensures that the optical elements are perfectly aligned and function as intended. Moreover, micro-molded parts can achieve the high surface quality necessary to minimize light scattering, which is essential for maintaining image clarity. Imperfections on the surface of optical elements can degrade image quality, so producing parts with tight profile tolerances is critical to the overall performance of AR systems.
Another important factor is the miniaturization required in AR devices. These systems, especially those worn on the head or integrated into smart glasses, must be lightweight and compact. Micro molding enables the production of extremely small components, often ranging from 20 microns to 1 mm in size, as well as larger components with micron-level features. The ability to produce such tiny, complex parts without compromising on optical performance is one of the key reasons why micro molding is indispensable for AR applications.
Precision in Micro Molding for Micro-Optics
The fabrication of micro-optic components demands an exceptional level of precision that can only be provided by specialized micro molding companies. This process is far more intricate than the molding of typical mechanical parts due to the delicate nature and complexity of micro-optic components. For AR applications, where optical performance is paramount, even the slightest deviation in a part's dimensions or surface quality can render it ineffective or flawed.
Achieving the required tolerances for micro-optic parts involves advanced expertise in molding processes, materials, and tooling. Micro molders must have a deep understanding of the unique challenges posed by optical components, from maintaining tight tolerances during the molding process to ensuring that the final parts meet the high optical standards required. This is particularly true for complex features like surface relief patterns in diffractive optical elements, which can be just a few hundred nanometers in size. These intricate features must be replicated with absolute precision to ensure that the optical component functions as intended.
In addition to the precision of the molding process, micro molders must handle and package these extremely small parts with care, as they are highly fragile and susceptible to damage during post-production handling. This requires specialized knowledge and equipment to ensure that the integrity of the micro-optic components is maintained throughout the manufacturing and packaging process.
Custom Molding Machines for Micro-Optics
Standard injection molding machines are generally not able to produce micro-optic components due to the high level of precision and small scale involved. Micro-optic parts, such as refractive lens arrays and DOEs, often require custom molding machines designed specifically to handle these intricate structures. These machines are equipped with advanced features that allow for the precise replication of small optical elements with micron-level accuracy.
For example, refractive micro lens arrays used in AR applications often measure less than 100 microns, and the production of such components requires specialized techniques that go beyond the capabilities of standard machines. Similarly, DOEs, which are crucial for controlling light in AR devices, have surface features measured in nanometers, and their successful production relies on molding machines that can maintain tight control over process parameters, such as shot size and material flow.
Companies like Accumold have developed custom micro molding machines that are capable of producing high-quality optical parts with the accuracy and consistency needed for AR applications. These machines are specifically designed to meet the challenges of micro-optics manufacturing, ensuring that each part meets the stringent performance standards required in high-tech fields such as AR, medical diagnostics, and advanced imaging systems.
Design and Development in Micro-Optic Manufacturing
The successful production of micro-optics for AR devices goes beyond the molding process itself and involves close collaboration between the micro molder and the product developer from the very beginning of the design phase. Early involvement in the design cycle allows micro molders to optimize the manufacturability of optical components, ensuring that they can be produced to the required specifications and scaled up for mass production.
Design for Manufacturability (DfM) and Design for Micro Molding (DfMM) principles are essential in this process. These design approaches help avoid common pitfalls that can arise when customers present designs that are not optimized for micro molding. For example, minor adjustments to the geometry or material selection of an optical component can significantly improve its manufacturability and reduce production costs.
Micro molders work closely with their customers to guide the design process, using advanced tools such as 3D solid modeling software to refine designs and ensure that they can be produced efficiently. This collaborative approach is crucial for achieving the best possible outcome in the production of AR optics, where precision and functionality are paramount.
Applications of Micro Molding in AR Devices
Micro molding plays a crucial role in various AR applications by enabling the production of the small, precise optical components that these devices rely on. One notable application is head-up displays (HUDs) used in automotive and aviation sectors. These displays project important information, such as speed and navigation data, onto the windshield, allowing the driver or pilot to access vital information without diverting their attention from the road or sky. Micro-molded lenses and light guides are essential for ensuring that the projected image is clear and properly aligned with the user’s line of sight.
Another key application is in AR smart glasses, which are designed to overlay digital content onto the wearer’s real-world view. These devices require optical components that are not only highly precise but also compact and lightweight, as they must be worn comfortably for extended periods. Micro molding enables the production of the tiny lenses and light guides needed to create these devices, all while maintaining the optical quality required for a seamless AR experience.
In medical applications, AR systems are used to overlay imaging data onto a patient during surgery or diagnosis, helping medical professionals to visualize internal structures in real time. The optics used in these systems must be extremely precise, as any distortion in the image could lead to diagnostic errors or surgical complications. Micro molding provides the precision and reliability needed to ensure that these optics function correctly in such critical applications.
Overcoming Challenges in Micro-Optic Production
While micro molding offers many advantages in the production of AR optics, there are also challenges that must be addressed to achieve successful outcomes. One of the primary challenges is tooling, which must be designed with extreme precision to produce the complex geometries and surface features required for micro-optic components. The development of high-precision molds is a critical step in ensuring that the final parts meet the necessary optical standards, and necessitates working with a micro molder that has in-house micro tool fabrication expertise.
Material selection is another challenge, as the polymers used for AR optics must offer both optical clarity and durability. In addition, they must be capable of maintaining their properties over time, even when exposed to environmental factors such as UV light and humidity. Micro molding allows for the use of advanced optical materials, including polymers that are specifically formulated for optical applications.
In addition, the assembly of AR devices that incorporate micro-optic components is often complex, as these parts are extremely small and delicate. To mitigate this challenge, micro molders should use automated assembly techniques that reduce the risk of contamination and ensure precise alignment of the components. Over-molding, a technique in which multiple functions are integrated into a single molded part, is also used to simplify assembly and reduce the need for additional post-production steps.
Summary
Micro molding plays an indispensable role in the production of optics for augmented reality applications. The technology offers the precision, scalability, and material versatility needed to meet the stringent optical requirements of AR devices. As the demand for AR systems continues to grow across industries, the need for high-quality micro-optic components will only increase, making micro molding a critical process in the development of the next generation of AR technologies.
From the production of tiny lenses and light guides to complex diffractive optical elements, micro molding enables the creation of the intricate optical parts that are essential for AR devices. By partnering with experienced micro molders who understand the unique challenges of micro-optic manufacturing, companies can ensure that their AR products deliver the performance and functionality required in today’s fast-paced, technology-driven world.
Brett Saddoris is Technical Marketing Manager at Accumold. The company has grown to a 130,000 square foot fortified facility designed for assurance of supply, employs over 350 staff, and is a net exporter shipping all over the world every day from its Ankeny, IA, USA facility which runs 24 hours a day, 7 days a week.
The content & opinions in this article are the author’s and do not necessarily represent the views of RoboticsTomorrow
Comments (0)
This post does not have any comments. Be the first to leave a comment below.
Featured Product
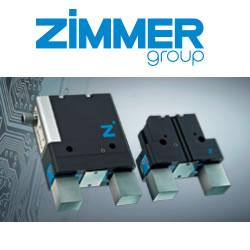